Jak drogi robot obniża koszty pracy?
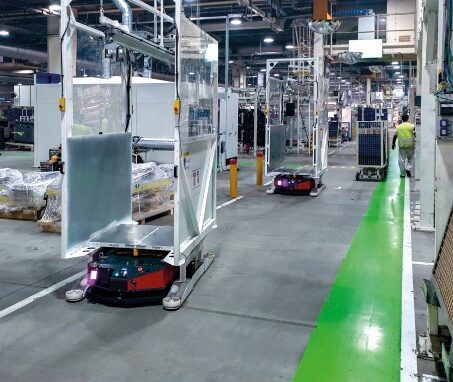
Roboty nie są tanie. Zakup i wdrożenie robota klasy AGV oznacza wydatki, które mogą wydać się niewspółmiernie wysokie w stosunku do kosztów pracy robotnika niewykwalifikowanego lub nawet operatora wózka widłowego. Jeżeli jednak policzymy całościowe koszty pracy, łatwo zauważymy, że drogie roboty (w zakupie i wdrożeniu) mają bardzo niskie koszty pracy. Inwestycja w robotyzację amortyzuje się w okresie dwóch lat, a pierwsze korzyści pojawiają się tuż po wdrożeniu.
Wbrew wizjom oferowanym przez kino z gatunku SF, jeszcze długo roboty nie zastąpią fryzjerów, dentystów, dyrygentów czy malarzy (nawet pokojowych). Czynności wymagające interakcji z otoczeniem, umiejętności negocjowania swoich decyzji czy wyczucia estetycznego nie są bynajmniej poza zasięgiem inteligentnych maszyn. Jednak koszty ich stworzenia są niewspółmierne do potencjalnych zysków. Całkowicie odmiennie przedstawia się sytuacja wykorzystania robotów w przemyśle i logistyce.
Co robot zrobi lepiej od człowieka?
Zastosowanie robotów daje największe korzyści wszędzie tam, gdzie konieczne jest wykonywanie czynności powtarzalnych, monotonnych lub wymagających dużej siły fizycznej. Zatrudniony przy wykonywaniu takich prac człowiek ulega naturalnemu zmęczeniu, ma problemy z utrzymaniem tempa pracy i zachowaniem wymaganej precyzji wykonywanych czynności. Efektem jest rosnąca liczba błędów, co w praktyce przekłada się na straty w mieniu, a także groźne dla życia i zdrowia ludzi wypadki. Remedium na te zjawiska jest coraz szersza automatyzacja i robotyzacja, które już teraz są w wielu branżach produkcji przemysłowej niezbędnym warunkiem zapewnienia ciągłości i wysokiej jakości produkcji.
Zastosowanie robotów daje najlepsze efekty w przypadku następujących typów czynności:
- czynności wykonywane w niekorzystnych warunkach środowiska pracy – w niskich i wysokich temperaturach, przy dużym zapyleniu czy obecności substancji toksycznych,
- czynności powtarzalne – wszelkie rodzaje pracy „przy taśmie”, wymagające wielogodzinnego wykonywania tych samych czynności lub ich sekwencji,
- czynności, których wykonanie wymaga dużej precyzji – na przykład montaż bardzo małych elementów,
- praca w miejscach trudno dostępnych – robot może pracować na dużych wysokościach, w wąskich kanałach czy niskich pomieszczeniach,
- prace wymagające użycia dużej siły – roboty mogą przemieszczać bez trudu ciężkie ładunki i powtarzać tę czynność dowolną liczbę razy.
W przypadku wymienionych czynności, roboty nie tylko są wydajniejsze i dokładniejsze, ale też zapewniają niemal stuprocentową powtarzalność gotowych wyrobów lub jakości wykonanej pracy. W przypadku robotów transportowych klasy AGV (Autonomous Guided Vehicle), wykorzystywanych do transportu wewnętrznego, oznacza to, że – poza nadzwyczajnymi sytuacjami – towar zawsze dotrze na wyznaczone miejsce o właściwej porze, części znajdą się na stanowisku montażowym, a materiały na stanowisku produkcyjnym.
Maszyna pracuje za najniższe stawki
Roboty oferują nieosiągalną dla ludzi jakość pracy, za którą nie musimy płacić. Koszty pracy inteligentnych maszyn sprowadzają się do zasilania i napraw. Roboty nie tylko nie otrzymują pensji, ale też nie potrzebują urlopów, nie biorą zwolnień lekarskich. Nie cierpią też na wypalenie zawodowe i nie wymagają stosowania systemów motywacyjnych. Z punktu widzenia pracodawcy fundamentalne znaczenie ma też to, że roboty nie zmieniają i nie porzucają pracy. To sprawy oczywiste, ale często pomijane przy zestawianiu kosztów zakupu i wdrożenia robotów z kosztami pracy ludzi.
O zaletach stosowania robotów najlepiej świadczy zachowanie międzynarodowych koncernów. Jeszcze niedawno oczywiste było, że najlepszym sposobem redukcji kosztów pracy jest przeniesienie produkcji do kraju, w którym ochrona pracowników jest słaba lub nie istnieje, a bezrobocie zmusza do podejmowania pracy za drastycznie niskie stawki. Obecnie powstała alternatywa: budowa fabryki w kraju rozwijającym się (czytaj: biednym) lub robotyzacja produkcji. I nie jest to alternatywa pozorna, lecz coraz częściej rzeczywistość globalnej gospodarki.
Jak AGV amortyzuje się w magazynie i fabryce?
Największą przeszkodą w robotyzacji są koszty zakupu i wdrażania inteligentnych maszyn. Drugą barierę stanowi niedostateczna wiedza o możliwościach robotów oraz wynikająca z niej rezerwa wobec ich wdrażania do produkcji czy logistyki.
– Mając tego świadomość, organizujemy regularnie szkolenia w ramach VersaBox Academy, które poświęcone są robotyzacji, Przemysłowi 4.0 czy inteligentnej intralogistyce – mówi Mateusz Wiśniowski, CTO VersaBox. – Oferujemy też nieodpłatne prezentacje działania naszych robotów typu AGV, szczególnie flagowego modelu VERSABOT 500. Pozwalają one osobiście ocenić, jaki potencjał biznesowy posiadają roboty.
Dotychczasowe doświadczenia VersaBox wyraźnie wskazują, że inwestowanie w robotyzację jest opłacalne. Średni okres amortyzacji w przypadku Versabot 500 wynosi od 6 miesięcy do dwóch lat. To, jak szybko robot zacznie przynosić konkretne zyski, zależy od typu produkcji oraz rodzaju wykonywanych czynności. Warto podkreślić, że na pierwsze efekty nie musimy czekać latami: robot oferuje natychmiastowy wzrost jakości pracy, poprawienie jej wydajności i bezpieczeństwa.