Roboty AGV vs przenośnik taśmowy w magazynie, sortowni, fabryce
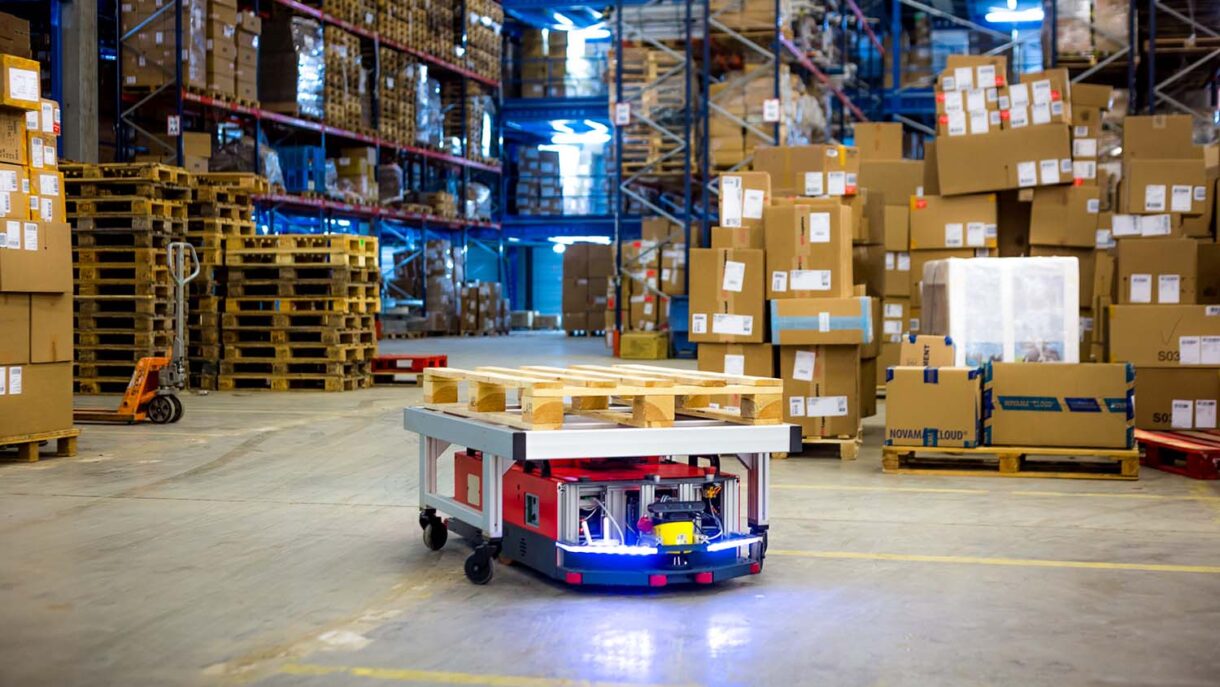
Roboty AGV są często zestawiane z przenośnikami taśmowymi oraz systemami jednoszynowymi (ang. monorail). W niektórych sytuacjach można je traktować jako komplementarne rozwiązania. Wybór pomiędzy tymi dwoma rodzajami transportu jest w praktyce uzależniony od tego, czy priorytetem jest szybkość, czy elastyczność zarządzania transportem.
Zastanawiając się nad wyborem konkretnego rozwiązania, należy mieć świadomość zalet i ograniczeń trzech wymienionych systemów intralogistycznych.
Roboty AGV: niezrównana elastyczność
Największą zaletą robotów AGV (Automated Guided Vehicle), w tym szczególnie maszyn autonomicznych AMR (Autonomous Mobile Robots), takich jak VERSABOT 500 i VERSABOT 1000, jest wieloaspektowa elastyczność. Dotyczy ona przede wszystkim łatwego dopasowania się do zastanych warunków realnego miejsca pracy. Wdrożenie robotów AMR jest możliwe bez konieczności dokonywania daleko idących zmian w architekturze i wyposażeniu obiektu. Maszyna mapuje teren i dzięki temu może sprawnie nawigować bez umieszczania żadnych znaczników oraz punktów orientacyjnych. Jedyną ingerencją jest zainstalowanie stacji ładowania, a także przygotowanie stanowisk do pobierania i zdawania towaru.
Elastyczność robotów klasy AMR dotyczy również zmiany tras oraz przezbrajania do realizacji nowych zadań. Zmiana miejsc poboru i zdawania transportowanych ładunków odbywa się bardzo szybko, a koszty przezbrojenia są minimalne. Dzięki temu można elastycznie dostosowywać logistykę do zmieniających się warunków produkcji.
W przypadku awarii robota, proces transportowy nie ustaje – zadania niesprawnej maszyny przejmuje inna. Operacja możliwa jest do przeprowadzenia „w locie”. Wszelkie zabiegi naprawcze i konserwacyjne we flocie robotów AMR możliwe są do wykonania bez wpływu na realizację procesów logistycznych. Utrzymanie ruchu staje się dzięki temu niezwykle skuteczne – zapewnienie realizacji procesów w cyklu ciągłym, praktycznie bez przerw nie stanowi problemu.
Niezwykle ważną cechą wdrożenia robotów AMR jest też zapewnienie bezpieczeństwa pracy. Autonomiczne wózki mogą pracować wraz z ludźmi, ale także z innymi środkami transportu, takimi jak wózki widłowe czy ciągniki przemysłowe. Są tak zaprojektowane, że nie wymagają wydzielania zamkniętych dla ludzi stref w magazynach i halach fabrycznych.
Przenośniki taśmowe i systemy monorail: bezkonkurencyjna wydajność
Przenośników taśmowych, podobnie jak systemów monorail, nie da się nazwać rozwiązaniami elastycznymi. Zestawienie linii przenośnikowej to duża i kosztowna inwestycja, która pochłania mnóstwo czasu. Wymaga precyzyjnego zaprojektowania, zestawienia stacji transferowych, przetestowania całego układu. Wysokie koszty wdrożenia rekompensuje szybkość działania. Intralogistyka oparta na przenośnikach taśmowych oraz systemach monorail odznacza się bardzo wysoką wydajnością.
Zdecydowanie słabą stroną taśmociągów i linii monorail jest to, że awaria jednego elementu wstrzymuje pracę całej linii. Służby utrzymania ruchu muszą działać niezwykle sprawnie, aby utrzymać ciągłość obsługi procesów logistycznych. Podobnie trudne jest przezbrojenie linii transportowej. Nawet najdrobniejsze zmiany wymagają dużych nakładów finansowych – przede wszystkim kosztownych przestojów w transporcie, a w konsekwencji również w produkcji.
Jednym z ważniejszych aspektów działania linii przenośnikowych jest problem zapewnienia bezpieczeństwa. W pełni zautomatyzowane przenośniki taśmowe wymagają fizycznych zabezpieczeń dostępu, a także monitorowania pracy całego systemu pod kątem zakłóceń pracy oraz stwarzania ewentualnych zagrożeń dla pracujących w sąsiedztwie ludzi.
Kiedy AMR, a kiedy przenośnik taśmowy?
Jeżeli głównym celem jest zapewnienie szybkości działania i wydajności transportu na stałych trasach, to zdecydowanie lepszym rozwiązaniem będą przenośniki taśmowe oraz systemy monoirail. Dodatkowym argumentem za ich zastosowaniem jest duże prawdopodobieństwo, że raz zestawiona linia przesyłowa nie będzie wymagała modyfikacji i przezbrojenia w wystarczająco długim czasie, aby możliwe było zamortyzowanie kosztów inwestycji.
Zastosowanie robotów AMR sprawdza się doskonale wszędzie tam, gdzie zainstalowanie przenośników taśmowych byłoby niemożliwe z powodów technicznych, zbyt kosztowne lub nieuzasadnione ze względu na konieczność stosowania częstych modyfikacji procesów logistycznych. Roboty AMR są wolniejsze od przenośników taśmowych, lecz zapewniają regularność i pewność dostaw w takich sytuacjach, jak transport detali pomiędzy gniazdami produkcyjnymi czy pomiędzy magazynem a halą produkcyjną
Podsumowanie
Wszystkie wymienione właściwości systemów intralogistycznych opartych na robotach AMR wpływają na relatywnie szybki zwrot inwestycji. Wysoka zdolność adaptacji robotów AMR do bieżących potrzeb zakładu produkcyjnego jest ważnym elementem budowania przewagi konkurencyjnej. Niskie koszty przezbrojenia umożliwiają łatwe zestawianie nowych linii i opłacalne wytwarzanie nawet krótkich serii określonego typu produktu. Jest to niezwykle ważne, bo zgodnie z aktualnymi prognozami, to właśnie umiejętność błyskawicznej reakcji na zmiany popytu oraz dostosowywania produkcji do zmian oczekiwań klientów będzie podstawowym warunkiem utrzymania się na rynku w warunkach globalnej, coraz silniej zautomatyzowanej produkcji przemysłowej.