System produkcyjny – podstawa efektywności operacyjnej
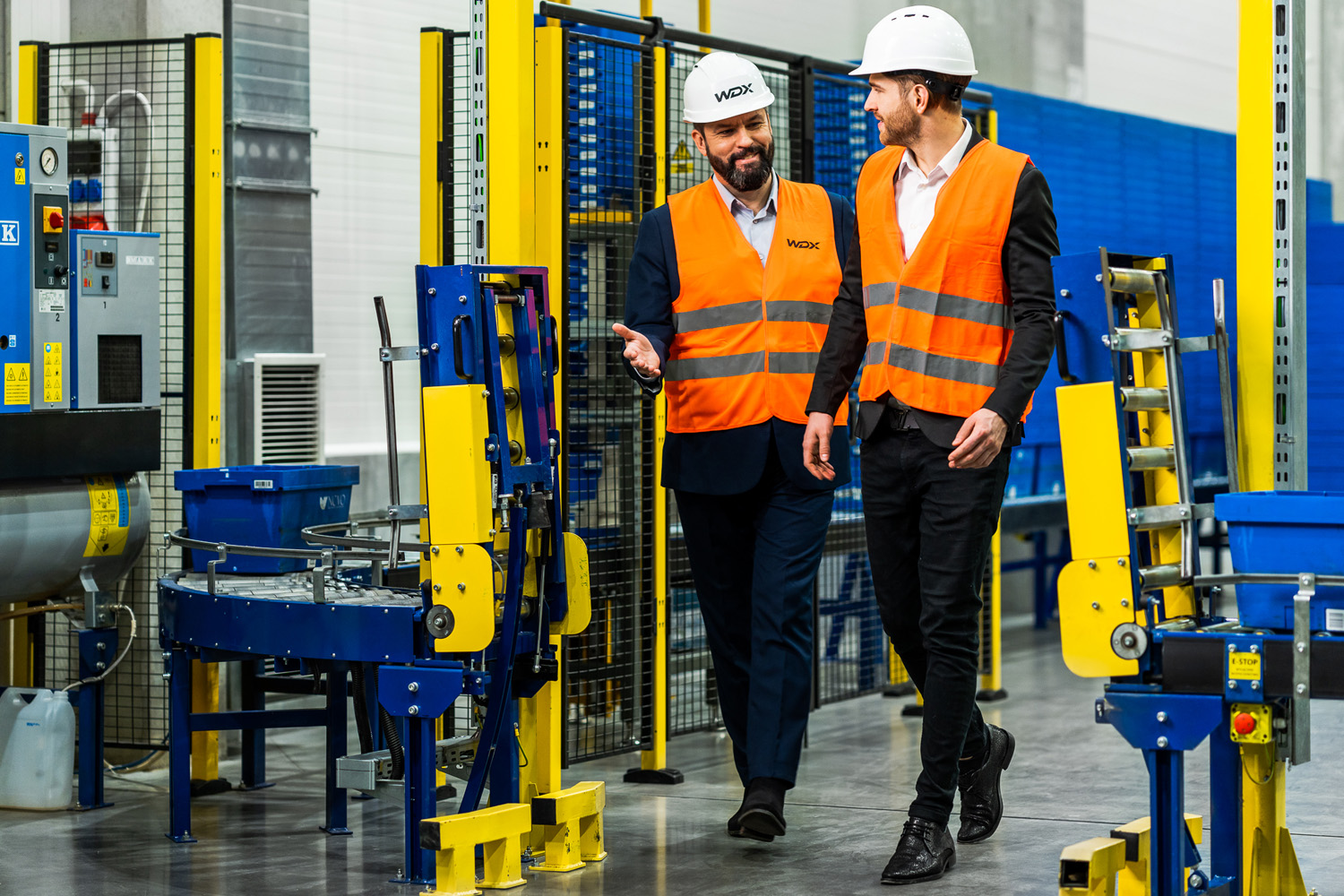
Prawidłowo działający system produkcyjny jest fundamentem efektywności i przewagi konkurencyjnej każdej organizacji. To właśnie on przekształca zasoby wejściowe w produkty, które idealnie odpowiadają na potrzeby klientów. Wspiera codzienne działania i jednocześnie otwiera drzwi do innowacji i rozwoju. System produkcyjny przepuszcza zasoby przez różnorodne procesy, by na końcu dostarczyć gotowe produkty. Bez tego firma nie mogłaby sprawnie funkcjonować.
Dobrze zaprojektowany system produkcyjny przekłada się na:
- optymalizację procesów,
- redukcję kosztów,
- podniesienie jakości oferowanych produktów,
- osiągnięcie przewagi konkurencyjnej.
Aby jednak system produkcyjny mógł spełniać swoją rolę, musi nieustannie ewoluować i dostosowywać się do zmieniających się warunków rynkowych oraz technologicznych. Wdrożenie nowoczesnych rozwiązań, takich jak:
- automatyzacja,
- zaawansowane systemy zarządzania produkcją,
- integracja inteligentnych technologii,
- autonomiczne systemy produkcyjne,
może znacząco zwiększyć jego wydajność. Ale czy jesteśmy gotowi na przyszłość, w której systemy produkcyjne staną się jeszcze bardziej zintegrowane, inteligentne i autonomiczne? Sprawdzimy w niniejszym artykule.
Czym jest system produkcyjny? Definicja i podstawowe założenia
System produkcyjny to złożony, zintegrowany mechanizm, który przekształca zasoby wejściowe – takie jak surowce, energia czy praca ludzka – w produkty materialne i niematerialne. Jego główne założenie to maksymalnie efektywne i zrównoważone wykorzystanie dostępnych zasobów.
Przykładem systemu produkcyjnego może być branża motoryzacyjna, gdzie system produkcyjny obejmuje:
- zaawansowane linie montażowe,
- precyzyjne systemy kontroli jakości,
- zautomatyzowane procesy logistyczne,
- oraz systemy zarządzania zasobami.
Wszystkie te elementy współpracują, aby zapewnić maksymalną wydajność i niezawodność.
Podstawowe cechy systemu produkcyjnego to:
- elastyczność – możliwość sprawnego dostosowania się do zmieniających się warunków rynkowych, na przykład fluktuacji sprzedaży,
- nieustanne doskonalenie procesów – fundament współczesnych strategii zarządzania produkcją,
Gdy nagle wzrasta popyt na dany produkt, dobrze zaprojektowany system produkcyjny potrafi zwiększyć wydajność bez kompromisów w zakresie jakości. To właśnie dzięki temu przedsiębiorstwa mogą skutecznie reagować na zmiany rynkowe.
Rola systemu produkcyjnego w przedsiębiorstwie
Dzięki systemom produkcyjnym możliwe jest efektywne wytwarzanie produktów o określonej jakości, w odpowiedniej ilości i w założonym czasie. Nie jest to jedynie fundament realizacji celów produkcyjnych, ale także kluczowy czynnik wpływający na ogólną efektywność firmy.
Korzyści wynikające z optymalizacji systemu produkcyjnego:
- obniżenie kosztów operacyjnych,
- zwiększenie konkurencyjności na rynku,
- poprawa stosunku efektów do nakładów,
- budowanie długoterminowej wartości dla firmy.
Efektywność systemu mierzy się stosunkiem wyników do nakładów, co pozwala ocenić, czy procesy produkcyjne są prowadzone w sposób ekonomiczny i zrównoważony. W praktyce oznacza to, że dobrze funkcjonujący system produkcyjny nie tylko generuje zyski, ale także wspiera w dłuższej perspektywie rozwój przedsiębiorstwa.
Elementy systemu produkcyjnego
Co stanowi składową każdego systemu produkcyjnego? Jego elementy, które determinują sposób działania i poziom efektywności. Możemy wyróżnić trzy główne grupy:
- zasoby wejściowe i wyjściowe,
- procesy produkcyjne,
- otoczenie systemu.
Każdy z tych komponentów pełni istotną rolę w przekształcaniu surowców w gotowe produkty. Zrozumienie ich znaczenia to podstawa, jeśli zależy ci na optymalizacji systemu i dostosowywaniu go do zmieniających się wymagań.
W dalszej części artykułu omówimy je szczegółowo.
Zasoby wejściowe i wyjściowe
Zasoby wejściowe to punkt początkowy każdego systemu produkcyjnego. Obejmują:
- materiały,
- energię,
- kapitał,
- informacje.
Bez tych elementów żaden proces produkcyjny nie może się rozpocząć. Z kolei zasoby wyjściowe to efekt końcowy całej pracy, czyli:
- gotowe produkty,
- usługi,
- odpady.
To właśnie te dwa pierwsze czynniki trafiają do odbiorców i decydują o sukcesie systemu produkcyjnego. Widoczne efekty pracy to nie tylko satysfakcja, ale także motywacja do dalszego działania.
Procesy produkcyjne i pomocnicze
Procesy produkcyjne są osią systemu, ponieważ to one przekształcają zasoby wejściowe w gotowe produkty. Ich efektywność i jakość mają kluczowe znaczenie dla całego systemu. Jednak równie ważne są procesy pomocnicze, które wspierają główne działania. Należą do nich:
- transport,
- składowanie,
- kontrola jakości.
Te procesy zapewniają płynność i niezawodność działania całości systemu. Współpraca między procesami głównymi i pomocniczymi jest nieodzowna.
Otoczenie systemu produkcyjnego
Każdy system produkcyjny funkcjonuje w określonym otoczeniu, które ma ogromny wpływ na jego działanie. Otoczenie to można podzielić na:
- czynniki wewnętrzne – pracownicy, organizacja produkcji,
- czynniki zewnętrzne – sytuacja gospodarcza, zmiany technologiczne.
Elementy te mogą być zarówno wsparciem, jak i wyzwaniem. Dlatego tak istotne jest ich zrozumienie oraz umiejętne zarządzanie nimi. Tylko w ten sposób system może elastycznie reagować na dynamiczne warunki rynkowe i technologiczne.
Rodzaje systemów produkcyjnych
Istnieje wiele metod organizacji procesów produkcyjnych, które różnią się stopniem automatyzacji, elastycznością oraz zdolnością do adaptacji. Rodzaje systemów produkcyjnych obejmują takie modele jak:
- produkcja liniowa,
- produkcja modułowa,
- produkcja maszynowa,
- produkcja jednostkowa.
Każdy z tych systemów charakteryzuje się unikalnymi cechami, które mogą znacząco wpłynąć na efektywność przedsiębiorstwa, szczególnie w obliczu dynamicznych zmian rynkowych i technologicznych. Omówmy każdy z nich:
Produkcja liniowa – sekwencyjność i wydajność
Produkcja liniowa opiera się na starannie zaplanowanych, następujących po sobie etapach, które minimalizują straty czasu i zasobów. Każdy krok w procesie jest zoptymalizowany, co przekłada się na:
- wysoką wydajność,
- powtarzalność procesów,
- utrzymanie stałego tempa produkcji,
- jednolitą jakość wyrobów.
To rozwiązanie idealnie sprawdza się w masowej produkcji, gdzie kluczowe jest zachowanie efektywności. Przykładem może być przemysł motoryzacyjny, w którym taśmy produkcyjne umożliwiają szybkie i efektywne wytwarzanie pojazdów. Prosto, skutecznie, bez zbędnych przestojów.
Produkcja modułowa – elastyczność i rekonfiguracja
Produkcja modułowa wyróżnia się możliwością jednoczesnego wykonywania różnych operacji, co znacząco zwiększa elastyczność całego systemu. Dzięki modułowej strukturze przedsiębiorstwa mogą:
- szybko dostosowywać linie produkcyjne do zmieniających się wymagań rynku,
- skutecznie reagować na trendy,
- oszczędzać czas i zasoby.
To podejście jest szczególnie cenione w branżach takich jak elektronika czy moda, gdzie różnorodność produktów i szybka reakcja na zmiany są najważniejsze. Przykładem może być producent smartfonów, który dzięki modułowej produkcji może wprowadzać nowe modele bez konieczności gruntownej przebudowy linii produkcyjnej.
Produkcja maszynowa – automatyzacja i precyzja
W produkcji maszynowej kluczową rolę odgrywa automatyzacja, która zapewnia:
- wyższą wydajność,
- większą precyzję,
- powtarzalność procesów,
- redukcję błędów,
- obniżenie kosztów operacyjnych.
Minimalny udział człowieka w tym systemie pozwala na osiągnięcie równocześnie wysokiej jakości i tempa produkcji, co jest szczególnie istotne w obliczu globalnej konkurencji. Przykładem może być przemysł farmaceutyczny, gdzie automatyczne linie produkcyjne gwarantują nie tylko dokładność, ale także bezpieczeństwo wytwarzania leków.
Produkcja jednostkowa – indywidualizacja i elastyczność
Produkcja jednostkowa to model, który umożliwia pełne dostosowanie procesów do indywidualnych zamówień klientów. Każdy produkt może być unikalny, co czyni ten system idealnym dla branż, w których personalizacja odgrywa kluczową rolę, są to:
- meblarstwo,
- produkcja luksusowych zegarków,
- inne branże wymagające indywidualnego podejścia.
Jednak tak wysoka elastyczność wiąże się z większymi wymaganiami w zakresie koordynacji i zarządzania, aby zapewnić terminowość oraz efektywność realizacji zamówień. Przykładem może być warsztat stolarski, który tworzy meble na zamówienie. Każdy projekt wymaga indywidualnego podejścia, ale efekt końcowy zawsze spełnia unikalne oczekiwania klienta.
System Produkcyjny Toyoty (TPS)
System Produkcyjny Toyoty (TPS) to kompleksowe podejście do produkcji, które opiera się na eliminowaniu marnotrawstwa oraz optymalizacji procesów. Dwie główne zasady TPS – Jidoka (automatyzacja z ludzką kontrolą, umożliwiająca wykrywanie problemów i ich natychmiastowe rozwiązywanie) oraz Just-In-Time (produkcja „na czas”, dostosowująca produkcję do rzeczywistego zapotrzebowania) – są integralną częścią Modelu 4P Toyoty. Model ten, składający się z Filozofii, Procesu, Ludzi i Partnerów, stanowi fundament TPS, kierując organizację na ścieżkę ciągłego doskonalenia. Filozofia opiera się na dążeniu do eliminowania marnotrawstwa, Proces koncentruje się na optymalizacji produkcji, Ludzie to kluczowy element umożliwiający skuteczne wdrożenie metod takich jak Lean Manufacturing i Six Sigma, które mają na celu poprawę jakości i wydajności. Te wspólnie zasady pozwalają Toyocie osiągnąć wysoką efektywność i jakość produkcji.
Nowoczesne technologie w systemach produkcyjnych
Współczesne systemy produkcyjne coraz częściej wykorzystują nowoczesne technologie, które rewolucjonizują zarządzanie procesami w przedsiębiorstwach. Kluczowe rozwiązania, takie jak zintegrowane systemy komputerowe (CIM) oraz elastyczne systemy produkcji (FMS), stanowią fundament zaawansowanej automatyzacji. Dzięki nim firmy nie tylko zwiększają swoją wydajność, ale także szybciej reagują na dynamiczne zmiany rynkowe. To właśnie zdolność adaptacji jest kluczem do sukcesu.
System CIM (Computer Integrated Manufacturing) to kompleksowe narzędzie, które integruje projektowanie, produkcję i dystrybucję w jeden spójny proces. Dzięki temu wszystkie etapy produkcji są ze sobą ściśle powiązane, co pozwala na optymalizację działań i redukcję kosztów. Z kolei System FMS (Flexible Manufacturing System) to elastyczne podejście do produkcji, wykorzystujące technologie takie jak obrabiarki CNC, roboty przemysłowe czy systemy transportowe. Ta elastyczność umożliwia firmom szybkie dostosowanie się do zmieniających się wymagań rynku – co w dzisiejszych czasach jest nieocenione.
Oba systemy, CIM i FMS, są przykładami zaawansowanych technologii produkcyjnych, które wspierają automatyzację i integrację procesów. Ich wdrożenie przekłada się na większą precyzję, krótszy czas produkcji i minimalizację błędów, co w efekcie podnosi jakość produktów.
Lean Manufacturing i Kaizen – filozofie ciągłego doskonalenia
Lean Manufacturing oraz Kaizen to dwie fundamentalne filozofie wspierające ciągłe doskonalenie procesów produkcyjnych. Lean Manufacturing koncentruje się na eliminacji marnotrawstwa i optymalizacji procesów, co prowadzi do wzrostu efektywności i jakości. Z kolei Kaizen, będący integralną częścią Lean Manufacturing, skupia się na systematycznym doskonaleniu i rozwiązywaniu problemów w procesach produkcyjnych.
Obie filozofie promują kulturę zaangażowania, w której każdy pracownik odgrywa aktywną rolę w procesie doskonalenia. Dzięki temu firmy mogą szybko reagować na zmieniające się warunki, co jest ważne dla utrzymania przewagi konkurencyjnej.
Systemy MES i ERP – monitorowanie i zarządzanie produkcją
Coraz więcej przedsiębiorstw wdraża systemy MES (Manufacturing Execution Systems) oraz ERP (Enterprise Resource Planning), które wspierają monitorowanie i zarządzanie produkcją. Systemy MES umożliwiają bieżące śledzenie i kontrolowanie procesów produkcyjnych, co pozwala na szybkie reagowanie na wszelkie odchylenia od planu. Natomiast systemy ERP integrują różne obszary działalności firmy – od zarządzania zasobami, przez finanse, aż po logistykę – co znacząco ułatwia planowanie i koordynację działań. Dzięki wdrożeniu systemów MES i ERP przedsiębiorstwa mogą znacząco poprawić efektywność swoich procesów. To z kolei przekłada się na wyższą jakość produktów i niższe koszty operacyjne. Czy przyszłość przyniesie jeszcze bardziej zaawansowane systemy, które będą w stanie przewidywać i zapobiegać problemom produkcyjnym, zanim te się pojawią? Wszystko wskazuje na to, że takie rozwiązania są już na horyzoncie.
W poniższej tabeli zestawiliśmy wszystkie wymienione wyżej systemy i narzędzia wraz z korzyściami jakie ze sobą niosą:
System | Funkcje | Korzyści |
CIM FMS | Integracja projektowania, produkcji i dystrybucji. Elastyczność dzięki technologiom, takim jak obrabiarki CNC i roboty przemysłowe. | Optymalizacja działań, redukcja kosztów, szybsze dostosowanie do rynku. |
Lean Manufacturing Kaizen | Eliminacja marnotrawstwa, optymalizacja procesów. Systematyczne doskonalenie i rozwiązywanie problemów. | Wzrost efektywności, zaangażowanie pracowników, szybka reakcja na zmiany. |
MES | Monitorowanie i kontrola procesów produkcyjnych. | Szybka reakcja na odchylenia od planu. |
ERP | Integracja obszarów działalności firmy (zasoby, finanse, logistyka). | Ułatwienie planowania i koordynacji działań. |
Efektywność i optymalizacja systemu produkcyjnego
Efektywność systemu produkcyjnego odgrywa ogromną rolę w budowaniu przewagi konkurencyjnej. To właśnie ona odzwierciedla zdolność firmy do sprawnego przekształcania zasobów w gotowe produkty. Im wyższa efektywność, tym lepsze wykorzystanie dostępnych środków. Nic więc dziwnego, że optymalizacja procesów produkcyjnych staje się nieodzownym elementem strategii każdej organizacji, która dąży do zwiększenia wydajności przy jednoczesnym obniżeniu kosztów operacyjnych.
Efektywność systemu produkcyjnego to jednak nie stała wartość. Wpływa na nią wiele czynników – od wydajności maszyn, przez kompetencje zespołu, aż po jakość dostarczanych surowców. Każdy z tych elementów może znacząco wpłynąć na końcowy wynik. Zrozumienie tych zależności i umiejętne zarządzanie nimi to fundament utrzymania konkurencyjności na wymagającym rynku.
Efektywność systemu produkcyjnego zależy od wielu współzależnych elementów, które mogą zarówno wspierać, jak i ograniczać jego wydajność:
- wydajność maszyn – bez sprawnie działających urządzeń produkcja może zostać sparaliżowana, a przestoje i awarie generują dodatkowe koszty,
- kompetencje pracowników – doświadczenie i umiejętności zespołu obsługującego maszyny mają ogromny wpływ na płynność oraz efektywność całego procesu,
- jakość materiałów – surowce niskiej jakości mogą prowadzić do powstawania wadliwych produktów, co zwiększa koszty i negatywnie wpływa na zadowolenie klientów. Zarządzanie jakością materiałów to absolutna podstawa optymalizacji.
Metody optymalizacji procesów produkcyjnych
Optymalizacja procesów produkcyjnych to fundament skutecznego zarządzania, który pozwala zwiększyć efektywność i jednocześnie obniżyć koszty. Wśród najważniejszych metod optymalizacji wyróżniają się:
- planowanie – precyzyjne określenie zasobów i czasu potrzebnego do realizacji produkcji. Dzięki temu minimalizuje się ryzyko przestojów i nadprodukcji,
- kontrola – bieżące monitorowanie procesów i szybkie reagowanie na wszelkie odchylenia od planu, co pomaga utrzymać wysoką jakość produktów,
- eliminacja marnotrawstwa – identyfikacja i usuwanie nieefektywnych elementów procesu, co pozwala zaoszczędzić czas i zasoby.
Redukcja marnotrawstwa i poprawa jakości to dwa filary, które mogą znacząco obniżyć koszty i zwiększyć efektywność systemu produkcyjnego. Marnotrawstwo – takie jak nadprodukcja, zbędne procesy czy defekty – generuje niepotrzebne wydatki, które obciążają budżet firmy. Dlatego identyfikacja i eliminacja tych strat to milowy krok w kierunku optymalizacji.
Poprawa jakości produktów to z kolei nie tylko większa satysfakcja klientów, ale także mniejsze koszty związane z reklamacjami i naprawami. Wdrożenie systematycznych kontroli jakości oraz inwestycje w nowoczesne technologie mogą znacząco pomóc w realizacji tych celów.
Elastyczność systemów produkcyjnych stała się fundamentem, bez którego trudno sprostać rosnącym oczekiwaniom klientów oraz zmiennym warunkom rynkowym. Przedsiębiorstwa, które potrafią błyskawicznie dostosować swoje procesy, zyskują przewagę konkurencyjną, która jest najważniejsza w globalnej gospodarce. Równie istotna jest współpraca z dostawcami, która umożliwia sprawne zarządzanie łańcuchem dostaw i minimalizację ryzyka związanego z przerwami w produkcji.
W dobie szybkiego rozwoju technologii firmy muszą być gotowe na wdrażanie nowoczesnych rozwiązań, które zwiększają efektywność i wspierają zrównoważony rozwój. Czy jesteśmy przygotowani na przyszłość, w której innowacyjność i elastyczność staną się fundamentem sukcesu w produkcji?
Sprawdź: Cyfrowa fabryka przyszłości.
Elastyczne systemy produkcyjne – adaptacja do zmieniających się potrzeb rynku
W czasach, gdy rynek zmienia się w zawrotnym tempie, elastyczne systemy produkcyjne stają się nieodzownym elementem strategii każdej firmy. Ich zdolność do szybkiego reagowania na nowe potrzeby klientów pozwala przedsiębiorstwom zachować konkurencyjność i efektywność. Dzięki elastyczności możliwe jest:
- wprowadzanie nowych produktów na rynek w krótkim czasie,
- modyfikowanie istniejących linii produkcyjnych w odpowiedzi na zmieniające się potrzeby,
- optymalne zarządzanie zasobami przynoszące oszczędności.
Nowoczesne technologie, takie jak automatyzacja i cyfryzacja, odgrywają w tym procesie ogromną rolę. Pozwalają one nie tylko zwiększyć wydajność, ale także lepiej dostosować się do zmieniających się preferencji konsumentów. Wdrażanie elastycznych systemów to nie tylko odpowiedź na bieżące potrzeby rynku, ale także inwestycja w przyszłość, która może przynieść długoterminowe korzyści. To krok w stronę budowania przewagi konkurencyjnej.
Jakie kroki mogą podjąć firmy, aby jeszcze bardziej zwiększyć elastyczność swoich systemów produkcyjnych i sprostać przyszłym wyzwaniom rynkowym? To pytanie, które wymaga ciągłego poszukiwania odpowiedzi.
Bezpieczeństwo pracy w systemach produkcyjnych
Bezpieczeństwo pracy w systemach produkcyjnych to fundament, który chroni zdrowie pracowników i minimalizuje ryzyko wypadków. Współczesne przedsiębiorstwa muszą nieustannie dążyć do poprawy warunków pracy, tworząc bezpieczne i zdrowe środowisko dla swoich zespołów. Bezpieczeństwo pracy nie tylko chroni ludzi, ale także wpływa na efektywność operacyjną i buduje pozytywną reputację firmy. To inwestycja, która przynosi wymierne korzyści.
Kluczowe działania, które mogą znacząco poprawić bezpieczeństwo w systemach produkcyjnych, obejmują:
- wdrożenie odpowiednich procedur bezpieczeństwa,
- regularne szkolenia pracowników w zakresie BHP,
- inwestycje w nowoczesne technologie zwiększające bezpieczeństwo,
- ścisłą współpracę między działami produkcji a zespołami odpowiedzialnymi za zarządzanie bezpieczeństwem.
Identyfikacja potencjalnych zagrożeń i wdrażanie skutecznych rozwiązań wymagają zaangażowania na każdym poziomie organizacji.
Zrównoważony rozwój i ekologiczne podejście
Współczesne systemy produkcyjne coraz częściej koncentrują się na zrównoważonym rozwoju i ekologicznym podejściu, w celu zminimalizowania swojego negatywnego wpływu na środowisko. Firmy wdrażają praktyki, które nie tylko zwiększają efektywność produkcji, ale także promują odpowiedzialność ekologiczną. Zrównoważony rozwój w produkcji to już nie tylko moda, ale konieczność, która przynosi korzyści zarówno środowisku, jak i przedsiębiorstwom.
Elastyczność systemów produkcyjnych odgrywa znaczącą rolę w realizacji celów zrównoważonego rozwoju. Dzięki zdolności do szybkiego wdrażania nowych technologii i procesów firmy mogą:
- efektywnie redukować zużycie zasobów,
- minimalizować emisję zanieczyszczeń,
- wprowadzać ekologiczne praktyki produkcyjne,
- budować pozytywny wizerunek odpowiedzialnego przedsiębiorstwa,
Wprowadzenie ekologicznych praktyk produkcyjnych to inwestycja w przyszłość, która przynosi długoterminowe korzyści zarówno przedsiębiorstwom, jak i społeczeństwu. Jakie innowacyjne technologie mogą jeszcze bardziej wspierać zrównoważony rozwój w systemach produkcyjnych, jednocześnie zwiększać ich elastyczność i efektywność? To pytanie, które otwiera drzwi do nowych możliwości.
Jak zaprojektować wydajny system produkcyjny?
Projektowanie wydajnego systemu produkcyjnego to złożone wyzwanie, które wymaga zarówno wiedzy, jak i strategicznego podejścia. Kluczowym elementem jest dogłębne zrozumienie specyfiki działalności firmy oraz optymalizacja najważniejszych procesów. Bez solidnej analizy potrzeb i celów przedsiębiorstwa trudno stworzyć system, który sprosta zarówno obecnym, jak i przyszłym wymaganiom. Wydajny system to taki, który efektywnie przekształca zasoby w produkty, jednocześnie minimalizując koszty i podnosząc jakość. Firmy muszą stale dostosowywać swoje systemy produkcyjne do nowych realiów rynkowych i technologicznych. Automatyzacja, zaawansowane systemy zarządzania czy integracja procesów – to tylko niektóre z rozwiązań, które mogą zrewolucjonizować produkcję.
Tworzenie wydajnego systemu produkcyjnego to proces wieloetapowy, który wymaga precyzyjnego planowania. Oto najważniejsze kroki, które trzeba uwzględnić:
- określenie celów – zastanów się, czy priorytetem jest zwiększenie wydajności, redukcja kosztów, czy poprawa jakości produktów. Jasno zdefiniowane cele pozwalają skupić się na tym, co najważniejsze.
- analiza zasobów – oceń dostępne maszyny, materiały i pracowników. Zrozumienie potencjału tych elementów umożliwia ich optymalne wykorzystanie.
- wybór technologii – dobierz technologie wspierające procesy produkcyjne, które są zgodne z celami firmy. To klucz do maksymalnej efektywności.
- wdrożenie i doskonalenie – nawet najlepszy system wymaga ciągłej adaptacji do zmieniających się warunków. Regularne ulepszanie procesów to podstawa sukcesu.
Zarządzanie zasobami i optymalizacja kosztów
Efektywne zarządzanie zasobami oraz optymalizacja kosztów to fundamenty każdego nowoczesnego systemu produkcyjnego. Najważniejsze jest maksymalne wykorzystanie dostępnych zasobów – maszyn, materiałów i ludzi – w sposób, który przynosi firmie największe korzyści. Każdy element systemu powinien działać jak precyzyjnie zaprojektowany mechanizm, eliminując marnotrawstwo i zwiększając efektywność.
Optymalizacja kosztów to proces, który wymaga zarówno analizy, jak i odwagi w podejmowaniu decyzji. Jak można to osiągnąć? Oto kilka przykładów:
- eliminacja nieefektywnych procesów,
- wdrożenie innowacyjnych rozwiązań, takich jak automatyzacja,
- wykorzystanie analizy danych w czasie rzeczywistym do podejmowania lepszych decyzji.
Takie działania mogą znacząco obniżyć koszty operacyjne, zwiększając jednocześnie rentowność firmy.
Przykłady wdrożeń i najlepsze praktyki
Analiza wdrożeń i najlepszych praktyk to nieocenione źródło inspiracji dla firm, które chcą usprawnić swoje procesy. Przykłady udanych implementacji pokazują, jak przedsiębiorstwa wykorzystały nowoczesne technologie i metody zarządzania, by osiągnąć wyższą efektywność i jakość produkcji.
Jedną z najczęściej stosowanych filozofii w optymalizacji systemów produkcyjnych jest Lean Manufacturing. Jej głównym celem jest eliminacja marnotrawstwa i ciągłe doskonalenie procesów. Wdrożenie takich praktyk może przynieść znaczące oszczędności oraz poprawić jakość produktów.
Wyzwania i trendy w systemach produkcyjnych – podsumowanie
Tradycyjnie na koniec każdego wpisu zastanawiamy się nad przyszłością i kierunkami rozwoju dla każdego opisywanego elementu procesów produkcyjnych i logistycznych. Tym razem skupimy się na wyzwaniach, przed którymi stoją współczesne systemy produkcyjne, oraz na sposobach ich adaptacji do szybko zmieniającego się otoczenia biznesowego. W dobie globalizacji, cyfryzacji oraz zmieniających się oczekiwań konsumentów i przepisów prawnych, przedsiębiorstwa muszą nieustannie wprowadzać innowacje, aby utrzymać konkurencyjność. Kluczowe w tym kontekście jest przekształcenie systemów produkcyjnych w kierunku większej elastyczności i zdolności adaptacji do nowych warunków rynkowych. Oznacza to konieczność wprowadzenia bardziej dynamicznych metod planowania produkcji, które pozwalają szybko reagować na zmiany popytu, a także optymalizować zasoby w czasie rzeczywistym. Równocześnie, systemy produkcyjne muszą stawiać na efektywną współpracę z dostawcami, co obejmuje zarówno poprawę procesów komunikacji, jak i integrację technologii, takich jak systemy ERP, które pozwalają na szybszą wymianę danych i lepszą synchronizację łańcuchów dostaw.
Współczesne systemy produkcyjne muszą także zmierzyć się z rosnącym naciskiem na zrównoważony rozwój i odpowiedzialność środowiskową. Firmy są coraz bardziej zobowiązane prawem do stosowania zielonych technologii, które nie tylko minimalizują negatywny wpływ na środowisko, ale także poprawiają efektywność energetyczną procesów. Z kolei automatyzacja i robotyzacja stanowią nieodłączny element transformacji, umożliwiając osiągnięcie wyższej wydajności, precyzji oraz bezpieczeństwa pracy. Z kolei rozwój sztucznej inteligencji (AI) i analizy danych pozwala na precyzyjne prognozowanie popytu, optymalizację procesów produkcyjnych oraz identyfikację potencjalnych problemów zanim staną się one krytyczne.
Na poziomie operacyjnym, wschodzącym trendem jest personalizacja produkcji, która wymaga od systemów produkcyjnych dostosowania się do indywidualnych potrzeb klientów przy jednoczesnym zachowaniu wysokiej efektywności kosztowej. Wzrost znaczenia modeli produkcji elastycznej oraz przemysłu 4.0, z naciskiem na Internet Rzeczy (IoT), pozwala na lepszą kontrolę nad całym procesem produkcji, a także na uzyskiwanie informacji na temat stanu maszyn w czasie rzeczywistym, co umożliwia proaktywne działania serwisowe.
W obliczu tych wszystkich wyzwań, przedsiębiorstwa muszą inwestować w ciągłe doskonalenie procesów oraz rozwój kompetencji pracowników, którzy będą w stanie efektywnie zarządzać nowoczesnymi technologiami i reagować na dynamiczne zmiany w otoczeniu biznesowym. Współczesne systemy produkcyjne stają się zatem bardziej skomplikowane, ale również bardziej zintegrowane i elastyczne, co pozwala na szybsze dostosowanie się do wymagań rynku i oczekiwań konsumentów. A jak wygląda sytuacja w Twojej firmie? Czy jesteście gotowi na wprowadzenie innowacyjnych rozwiązań, które mogą przynieść długoterminowe korzyści i umocnić Waszą pozycję na rynku? Warto o tym pomyśleć.