Intralogistyka 4.0. Słownik pojęć – część II
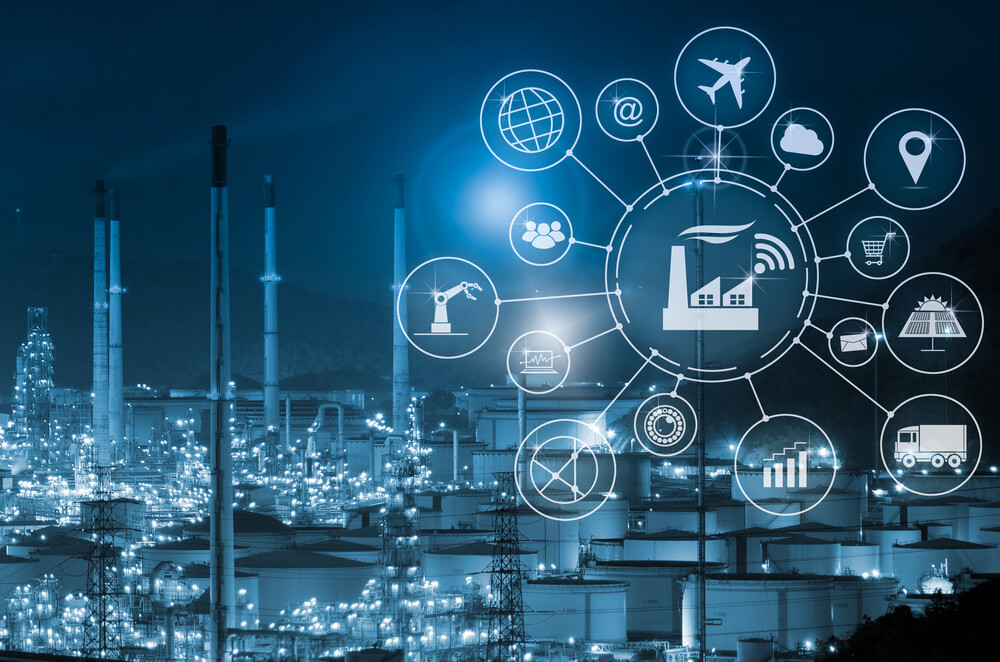
Kolejna odsłona słownika intralogistycznego to przegląd definicji pojęć, jakie pojawiają się w publikacjach na blogu VersaBox. Wszystkie w sposób bezpośredni powiązane są z możliwością zastosowania robotów klasy AMR (Autonomous Mobile Robots) w realizacji zadań transportu wewnętrznego. Tym razem skupiamy się na objaśnieniu terminologii związanej z modelem lean management.
Sprawdź co to jest intralogistyka
Dowiedz się również co to jest AMR – autonomiczne roboty mobilne
Lean management
Zbiór zasad organizacji produkcji przemysłowej, którego pierwowzorem były modele zarządzania produkcją rozwijane od poł. XX w. przez japoński koncern Toyota Motor Company. Lean management to w dużej mierze sformalizowane i naukowo opisane zasady TPS, czyli Toyota Production System. Po II wojnie światowej Japończycy poszukiwali rozwiązań, które pozwolą na realne podniesienie jakości produkcji oraz redukcję strat. Po kilku dekadach udało się stworzyć model zarządzania, w którym zminimalizowano zbędną nadprodukcję, ograniczono tworzenie zapasów, wyeliminowano oczekiwanie i puste przejazdy (zbędny transport) oraz jakikolwiek niepotrzebny ruch. Kluczowe pojęcia TPS to just-in-time (czyli dokładnie na czas) oraz kaizen (nieustanne doskonalenie, które jest nie tylko sposobem poprawy jakości, ale filozoficzną podstawą myślenia o procesie produkcji). TPS został dostrzeżony w USA i Europie po opublikowaniu w 1991 r. książki The Machine That Changed the World. Jej autorzy opisali system jakości Toyoty i po raz pierwszy użyto terminu lean management.
Milk run
Termin tłumaczony na język polski jako kurs mleczarza, pętla mleczarza. Określa model realizacji dostaw komponentów z magazynu na linie produkcyjne (lub do gniazd produkcyjnych) i gotowych wyrobów z gniazd produkcyjnych do magazynu (lub do klienta). Jego głównym założeniem jest płynność dostaw, zapewnienie przepływu transportowanych ładunków w taki sposób, aby uniknąć powstawania nadmiernych zapasów. W praktyce milk run oznacza stworzenie systemu cyklicznych dostaw, w których jeden zestaw transportowy (np. pociąg intralogistyczny czy robot AMR) odwiedza kolejne punkty pętli transportowej. Jeden z modeli kursu mleczarza przewiduje dostarczanie do kolejnych punktów zamówionych komponentów czy odbieranie pustych pojemników wielorazowych. Inną możliwością jest dostarczanie pustych pojemników i odbieranie pełnych. Trasy dostaw są stałe, a kursy realizowane w dokładnie określonych terminach. Dostawy komponentów oraz odbiory gotowych produktów są niewielkie, ściśle dopasowane do aktualnych potrzeb.
Gniazdo produkcyjne
Pojęcie to służy do zbiorczego określenia zestawu ustawionych obok siebie maszyn, komponentów i stanowisk dla personelu. Gniazdo produkcyjne może być zorganizowane technologicznie lub przedmiotowo. W pierwszym przypadku w gnieździe wykonywany jest określony typ operacji (np. spawanie, obróbka skrawaniem, malowanie). Z kolei w gnieździe zaprojektowanym przedmiotowo powstają określone wyroby lub całe grupy wyrobów. Gniazda typu przedmiotowego pozwalają na znaczącą redukcję transportu wyrobów w przestrzeni hali produkcyjnej. Poprawia się też kontrola jakości, bo ewentualne usterki wychwytywane są natychmiast po ich powstaniu, a nie dopiero po przemieszczeniu do kolejnego obszaru produkcji. System gniazd produkcyjnych jest jednym z głównych modeli organizacji produkcji, obok modelu produkcji liniowej oraz produkcji potokowej.
5W (5 Whys)
Metoda 5 whys to jednym z elementów kaizen (systemu poprawy jakości), który jest filarem lean management. Metodę opracował Taiichi Ohno, główny twórca Toyota Production System (TPS, lean management). Podobno pomysł zaczerpnął z rozmów ze swoją kilkuletnią córką – dziecko zadawało pozornie naiwne pytania, zaczynające się od słowa “dlaczego…”. Ohno zdał sobie sprawę, że przymus tłumaczenia komuś, kto nie rozumie, pozwala wykryć prawdziwe źródło problemu. Dotarcie do źródła problemu nie powinno wymagać więcej niż pięciu pytań. Jeżeli pytań jest więcej, a problem dalej nieuchwytny, oznacza to, że pytania nie zostały właściwie sformułowane. 5W może być bardzo skutecznym sposobem optymalizacji procesów intralogistycznych, w tym np. rozładowywania kolejek do punktów poboru czy zdawania ładunków.
Kanban
Pojęcie funkcjonujące w ramach lean management. Pierwotnie był to system czytelnie opisanych papierowych kart wyrobów, które umieszczano na specjalnej tablicy. Obecnie tablice mają postać elektroniczną. Są powszechnie stosowane nie tylko w przemyśle, logistyce i intralogistyce, ale także w wielu innych dziedzinach gospodarki. Każdy proces wytwarzania wartości, np. produkcji określonego wyrobu (może to być wyrób fizyczny, ale też koncepcyjny) czy transportu ładunku można rozbić na trzy etapy: to do, doing i done (czyli: do zrobienia, w trakcie i zrobione). Rozpoczęcie oraz zakończenie każdego etapu procesu odnotowywane jest w postaci umieszczenia karty na tablicy lub jej odpowiedniego przemieszczenia (zmiany statusu). Dzięki temu możliwy jest stały wgląd w sytuację i natychmiastowe wykrywanie miejsc, w których dochodzi do:
- powstania braków (materiałów, komponentów gotowych wyrobów),
- powstawanie opóźnień (przetrzymanie produktu, wstrzymanie procesu),
- gromadzenia niepotrzebnych zapasów
- tworzenia się kolejek.
Pozwala też szybko zlokalizować miejsca, w których maszyny i/lub personel pozostają w bezczynności lub – przeciwnie – wykonywane są operacje zbędne, bezproduktywne. W przypadku procesów intralogistycznych, kanban pozwala jasno określić jaki ładunek, w jakiej ilości, dokąd i skąd ma być przetransportowany.
Pociąg intralogistyczny
Pociąg składa się z ciągnika przemysłowego i „wagoników”, czyli różnego typu wózków transportowych. Ciągnik obsługiwany jest przez operatora. Organizacja logistyki wewnętrznej (intralogistyki, transportu bliskiego), która wykorzystuje metodologię milk run, wymaga użycia pociągów intralogistyczych. Alternatywą dla pociągów są roboty AMR, które realizują zadania transportowe autonomicznie. Zapewniają jeszcze większą elastyczność skalowania wielkości dostaw i elastycznego reagowania na zmiany zapotrzebowania ilościowego oraz pod względem rodzaju przewożonych ładunków. Zamiast tworzyć skład transportowy, można dynamicznie przydzielać pojedyncze wózki do realizacji określonych procesów produkcyjnych.