Intralogistyka „Data Driven”
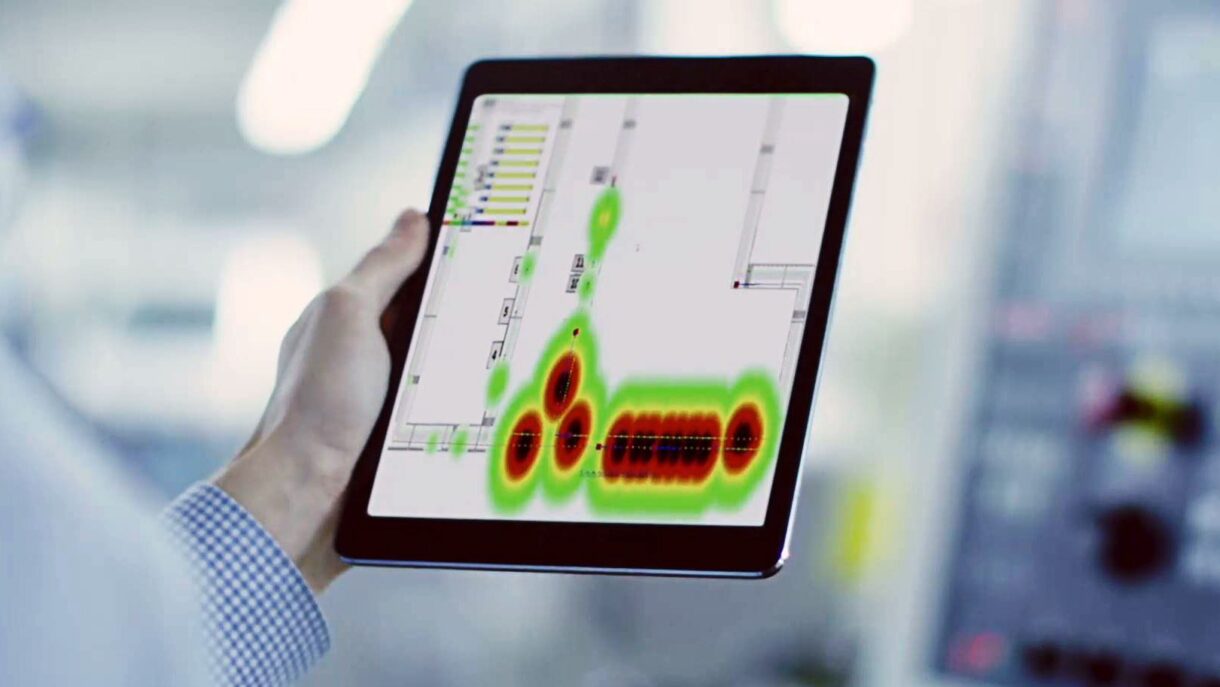
Data-driven to jeden z gorących trendów w gospodarce, w tym szczególnie w przemyśle. Chodzi w nim o to, aby zarządzanie procesami biznesowymi oprzeć na analizie danych. Celem jest monetyzacja danych, czyli w praktyce optymalizacja kosztów produkcji (oszczędności) i poprawienie wyników sprzedaży (maksymalizacja zysku). Oferowany przez Versabox system transportowy Autonomy@Work umożliwia zarządzanie flotą robotów VERSABOT klasy AMR w modelu data-driven. Istotnym komponentem systemu jest VersaBox Virtual Factory – narzędzie do modelowania pracy systemów intralogistycznych. Roboty i platforma programowa tworzą kompletne rozwiązanie intralogistyczne o ogromnym potencjale optymalizacyjnym.
Każdy zakład przemysłowy, każda linia produkcyjna i każda maszyna produkuje ogromne ilości danych. Tylko niewielka ich część jest wykorzystywana w procesach zarządzania produkcją. Metodologia data-driven ma na celu gromadzenie i przetwarzanie danych do postaci, w której staną się one podstawą do podejmowania decyzji biznesowych.
Przeczytaj czym jest intralogistyka
Czego dowiesz się od systemu autonomy@work?
Wykorzystując roboty AMR czy uruchamiając symulację, uzyskujemy dostęp do precyzyjnych danych na temat parametrów procesów intralogistycznych, a w efekcie również produkcyjnych. Możemy na bieżąco monitorować czas realizacji poszczególnych etapów przepływu materiałów i produktów:
- Minimalne, maksymalne oraz uśrednione czasy dostawy i odbioru – wiedząc, ile czasu upływa od złożenia zamówienia do fizycznej realizacji dostawy, możemy z odpowiednim wyprzedzeniem składać zamówienia na dostawy potrzebnych komponentów i zlecać odbiór gotowych produktów;
- czas trwania cyklów pracy linii produkcyjnych – otrzymujemy informacje na temat realnego czasu trwania jednego cyklu pracy linii, a w efekcie możemy na bieżąco dostarczać potrzebne komponenty i odbierać gotowe wyroby bez konieczności tworzenia zapasów. Możemy też badać efektywność pracy każdej linii produkcyjnej, dzięki zestawieniu volumenu transportów do/z linii produkcyjnej per zmiana/pracownik
- potrzebna wielkość pól buforowych – bufory są niezbędne do sprawnego działania dostaw i utrzymania płynności produkcji – określenie optymalnej wielkości buforów usprawnia i znacząco skraca realizację całego łańcucha.
Wymienione parametry w tradycyjnych systemach intralogistycznych są trudne do uchwycenia i standaryzacji. Jeżeli zastosujemy roboty AMR, nie tylko otrzymamy łatwy dostęp do danych, ale także pełną przewidywalność procesów. Autonomiczne maszyny gwarantują bardzo dokładną powtarzalność czynności, co pozwala wyeliminować rozbieżności czasowe. Określony proces jest wykonywany zawsze w niemal identycznym czasie. Dzięki temu zyskujemy realną kontrolę nad łańcuchami dostaw. Wykorzystanie danych pozwala zoptymalizować cały system transportu wewnętrznego w fabryce czy magazynie.
Wirtualne modele zastępują arkusze kalkulacyjne
W stosowanych obecnie metodach zarządzania intralogistyką i projektowania systemów transportu wewnętrznego podstawowym narzędziem ciągle jest arkusz kalkulacyjny. Tradycyjny model projektowania systemów intralogistycznych opiera się na wiedzy i doświadczeniu, a także na intuicji osób budujących systemy transportowe. Nie bez znaczenia jest też aspekt emocjonalny, czyli np. forsowanie własnych pomysłów i rozwiązań, o których słuszności jesteśmy przekonani. Proces decyzyjny opiera się o subiektywną, nie zawsze racjonalną, ocenę sytuacji. Efektem jest duże ryzyko błędów, a w konsekwencji nietrafionych decyzji biznesowych, np. związanych z zakupami maszyn czy środków transportu wewnętrznego. Bazując na arkuszu kalkulacyjnym nie przewidzimy i nie rozwiążemy problemów interakcji, w które wchodzą autonomiczne roboty ze sobą, innymi środkami transportu czy personelem ludzkim. Trudno na przykład ocenić, gdzie powstanie kolejka robotów i jaką będzie miała długość. A już całkowicie niemożliwe będzie przeanalizowanie wpływu czasu oczekiwania w kolejce na ruch w innych rejonach hali.
Model data-driven intralogistic zmierza do oparcia procesu decyzyjnego na danych, czyli na obiektywnych informacjach na temat realnych warunków panujących w hali produkcyjnej. Zebrane informacje wykorzystywane są do stworzenia wirtualnego modelu hali wraz z pracującymi w niej maszynami i ludźmi. Jest on doskonałym środowiskiem do testowania wszystkich planowanych zmian, zanim zostaną wdrożone w realnej przestrzeni produkcyjnej.
Ostatecznym celem tworzenia modelu jest powstanie tzw. wirtualnego bliźniaka (digital twin), czyli odtworzenia hali produkcyjnej w świecie wirtualnym. Model, zasilany na bieżąco danymi procesowymi, ulega stałemu doskonaleniu. W pewnym momencie staje się niemal idealnym odzwierciedleniem wszystkich procesów zachodzących w realnej przestrzeni. W tak wykreowanym środowisku można przeprowadzić dowolne testy. Na odpowiedzi nie trzeba długo czekać. W świecie wirtualnym czas przestaje być barierą, bo procesy można dowolnie przyspieszać. W ciągu kilku godzin model dostarcza informacji, których uzyskanie w rzeczywistości mogłoby trwać kilka miesięcy. Wyniki są tym wiarygodniejsze, im więcej danych wprowadziliśmy do modelu. W praktyce oznacza to, że im dłużej istnieje wirtualny bliźniak, tym cenniejszych informacji może dostarczyć na temat swojego realnego pierwowzoru.
Do przestawienia tradycyjnego zarządzania intralogistyką na model data-driven potrzebne są autonomiczne wózki transportowe (roboty AMR) oraz odpowiedni system do modelowania procesów i zarządzania flotą.
VersaBox Virtual Factory
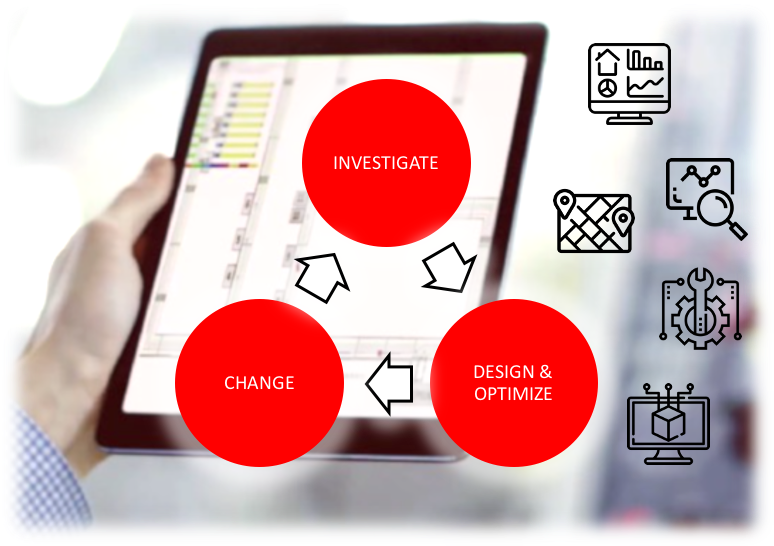
VersaBox oferuje kompletne rozwiązanie intralogistyczne, którego składnikami są roboty AMR VersaBot oraz platforma Autonomy@Work. Możliwości wykorzystania systemu dotyczą wszystkich etapów organizacji i zarządzania transportem wewnętrznym:
- analiza przedwdrożeniowa –VVF pozwala wymodelować i przetestować system transportu wewnętrznego, zanim jakiekolwiek działania zostaną przeprowadzone w fizycznej przestrzeni produkcyjnej, a w efekcie zredukować ryzyko inwestycyjne skrócić czas i obniżyć koszty wdrożenia,
- monitorowanie i optymalizacja w trakcie eksploatacji – platforma stworzona przez VersaBox umożliwia monitoring pracy floty robotów AMR w czasie rzeczywistym i natychmiastowe wprowadzanie korekt,
- testowanie modyfikacji przed implementacją – planowane modyfikacje i rozszerzenia systemu transportu wewnętrznego można przetestować na wirtualnym modelu, co pozwala uniknąć kosztownych błędów i niepotrzebnych inwestycji.
Możliwości systemu można poszerzyć poprzez wprowadzenie elektronicznych znaczników. Pozwolą one wprowadzić do wirtualnego modelu hali produkcyjnej czy magazynowej informacje o ruchach wszystkich obiektów – robotów AMR, wózków widłowych, pociągów logistycznych i ludzi. Dzięki temu przy obliczeniach nie będziemy operować zakładaną średnią prędkością poruszania się obiektów, lecz wykorzystamy dane z realnego środowiska pracy. Efekt? Nieosiągalna innymi sposobami precyzja modelowania procesów. Algorytm samouczący będzie mógł przeanalizować tysiące realnych sytuacji. W oparciu o nie odpowie na pytania o następstwa każdej zmiany, którą zechcemy wdrożyć. Podsunie nam najlepsze rozwiązania optymalizacyjne.
Już pierwsze praktyczne wykorzystania systemu VVF dowiodły, że modelowanie zmian oraz ich optymalizacja na wirtualnym modelu daje do 30% redukcji kosztów wdrożeń.
Wirtualny model hali produkcyjnej czy magazynowej zainstalowany jest w chmurze (cloud computing). Klient może dostarczyć dane i zlecić odpowiednie testy lub przeprowadzić cały proces samodzielnie. Wszystko zależy od wykupionego zakresu usług.
Konserwacja realnie predykcyjna
VersaBox Virtual Factory pozwala modelować pracę robotów AMR i innych elementów sytemu intralogistycznego w długich okresach. Oznacza to, że możliwe staje się np. dokładne policzenie liczby motogodzin, które maszyna dopiero wypracuje w danym przedziale czasowym. Z kolei bieżący monitoring pracy pozwoli wychwycić rozbieżności pomiędzy modelem, a rzeczywistą eksploatacją. Nic nie stoi też na przeszkodzie, aby roboty same informowały o swoim stanie technicznym. Dane procesowe z czujników temperatury czy wibracji mogą zostać przetworzone do postaci raportów dla służb utrzymania ruchu.
Wspomniane wyżej dane stanowią doskonałą bazę do stworzenia precyzyjnych planów konserwacji robotów. Będą one oparte na realnym stanie maszyn, a nie na ustalonym z góry harmonogramie, jak to ma miejsce w przypadku typowej konserwacji prewencyjnej. Prowadząc bieżący monitoring możemy podjąć z odpowiednim wyprzedzeniem działania zapobiegawcze i nie dopuścić do wystąpienia awarii. Te same dane można wykorzystać do precyzyjnego budżetowania wydatków na konserwację. W efekcie nowe podejście do zarządzania intralogistyką pozwala przestawić również utrzymanie ruchu na model data-driven.