Roboty AMR działają zespołowo, czyli jak symulacja wspiera procesy intralogistyczne
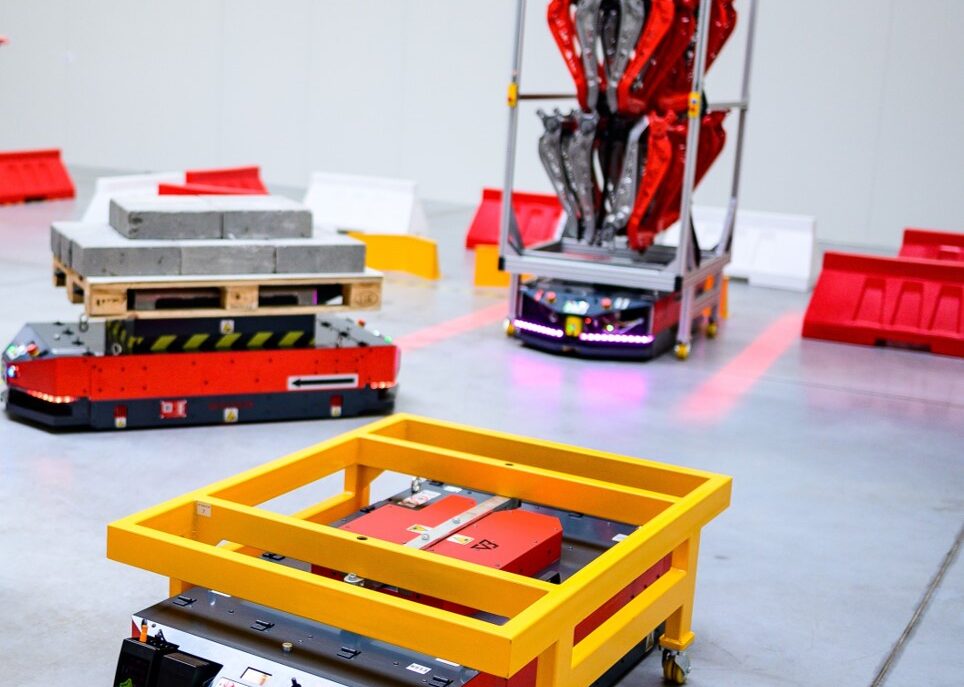
Roboty AMR w hali fabrycznej, które działają jak zgrany zespół, czy rój pracowitych owadów, to wizja przypominająca kadr z filmu science fiction. Maszyny wymieniają się między sobą informacjami, negocjują pierwszeństwo przejazdu czy wyznaczają objazdy na podstawie bieżącej analizy danych.
Podejmowanie całkowicie autonomicznych decyzji mieści się w zakresie możliwości robotów AMR. I może być bardzo przydatne. Jednak przestrzenie magazynowe nie są na tyle skomplikowane, aby konieczna była tak daleko posunięta samodzielność. Większą wartość praktyczną mają „gotowe” rozwiązania.
Jeżeli trasa A jest zablokowana, to wybierz trasę B
Robot AMR może podejmować samodzielnie decyzje w oparciu o bieżącą analizę danych, które wymienia z innymi robotami. Ale może też wybierać spośród zdefiniowanych tras – jeżeli trasa A jest zablokowana, to wybiera trasę B i podąża do celu. A jeżeli trasa B też jest nieprzejezdna, to czy wówczas wybiera trasę C? Mógłby, ale najczęściej nie ma takiej możliwości lub konieczności.
W praktyce transport z punktu do punktu może odbywać się po dowolnej liczbie tras. jednej lub dwóch trasach. W momencie zablokowania jest wybrana przez AMR trasa główna, robot za każdym razem od nowa analizuje napływające z innych maszyn dane i na ich podstawie planuje alternatywną ścieżkę.
Wybór optymalnej trasy to wybór najkrótszego czasu przejazdu, a nie najmniejszej odległości w przestrzeni. Wynika to stąd, że w konkretnych warunkach środowiska pracy może się okazać, że dłuższą trasę da się pokonać szybciej. Przejazd na krótszym dystansie może zająć więcej czasu, bo jest to odcinek bardziej zatłoczony lub wymagający poruszania się ze znacznie mniejszą prędkością.
Jeżeli roboty są zespołem, to system pełni funkcję szefa
Jeżeli robot sam nie może zebrać danych i podjąć decyzji, np. o sposobie ominięcia przeszkody, to komunikuje się z systemem, który decyduje, jakie działanie należy przedsięwziąć. Na przykład podjeżdżając do przeszkody, której ominięcie wymaga wjechania na przeciwny pas ruchu, robot dostaje od systemu informację, czy z naprzeciwka nadjeżdża inny robot (inny pojazd), czy nie. Zamiast zbierać dane od innych robotów i negocjować przejazd, od razu podejmuje działanie – przejeżdża lub ustępuje pierwszeństwa przejazdu.
Początkowo stosowaliśmy schemat komunikacyjny wiele do wielu. Roboty dzieliły się danymi między sobą bez pośrednictwa żadnego centrum decyzyjnego – mówi Paweł Oziębło, Business Development Manager w VersaBox. – Jednak w przypadku większych flot, znacznie większą wydajność i przewidywalność działania robotów zapewnia architektura gwiazdy – wszystkie roboty komunikują się z centralnym systemem, który dystrybuuje informacje do poszczególnych maszyn. Nie oznacza to jednak, że w przypadku utraty łączności cały system staje. Przeciwnie – roboty w dalszym ciągu realizują swoje zadania. Versaboty są maszynami autonomicznymi nie tylko z nazwy.
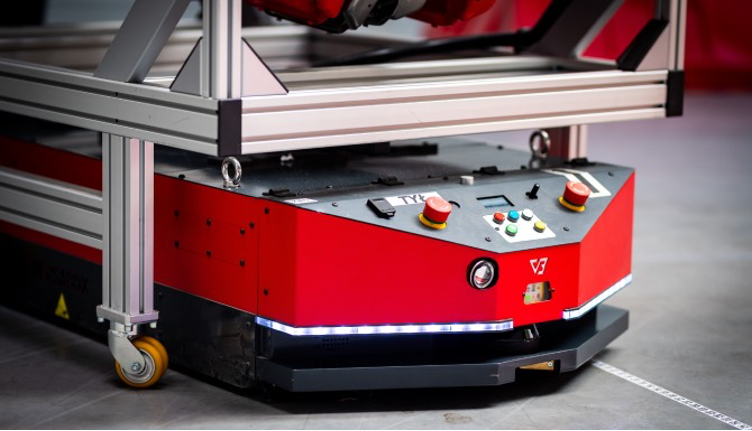
Podstawowa zasadą w ustawianiu kolejki zadań jest zasada „kto pierwszy, ten lepszy”. Decyduje ona o ustalaniu pierwszeństwa przejazdu na skrzyżowaniach, kolejności w punktach poboru i zdawania ładunków czy miejsca w kolejce do stacji ładowania. Można też określić priorytety ustawiając na sztywno które z robotów, w zależności ich obecnego statusu (np. z towarem lub bez ) mają zawsze pierwszeństwo.
Kolejkę można rozładować, zanim powstanie
Stosowanie narzędzi opracowanych przez VersaBox pozwala uniknąć powstawania nadmiernych kolejek i tworzenia się zatorów. Wynika to stąd, że system intralogistyczny tworzony jest najpierw jako wirtualny model. Na takim prototypie testowane są wszystkie rozwiązania, zanim rozpocznie się ich fizyczne wdrożenie. Możliwe jest sprawdzenie wielu wariantów i alternatywnych sytuacji. Korzystając z symulacji można nie tylko zaprojektować czy przetestować, ale także zoptymalizować system transportu wewnętrznego przed wprowadzeniem robotów na halę produkcyjną lub magazynową.
Wymienione działania można przeprowadzić dzięki narzędziu VersaBox Virtual Factory. Umożliwia ono modelowanie procesów intralogistycznych, ich testowanie oraz zarządzanie zmianami. Niezwykle ważne jest to, że wszystkie operacje może wykonać personel klienta końcowego. Użytkowanie systemu nie wymaga specjalistycznego przygotowania czy umiejętności programowania.
Dzięki zastosowaniu VersaBox Virtual Factory na wirtualnym modelu można przepracować w zasadzie każdą sytuację, jaka może zaistnieć w rzeczywistości. Odwołując się do analogii pochodzących ze świata pracy ludzi, można powiedzieć, że flota VERSABOTów jest zespołem autonomicznych, cyfrowych współpracowników, zarządzanych przez centralny system. Jednostki realizują autonomicznie swoje zadania, natomiast system centralny dba o bezkolizyjne działanie wszystkich procesów intralogistycznych. Dzięki temu zarządzanie flotą staje się w pełni przewidywalne.