Procesy produkcyjne – kompleksowy przewodnik
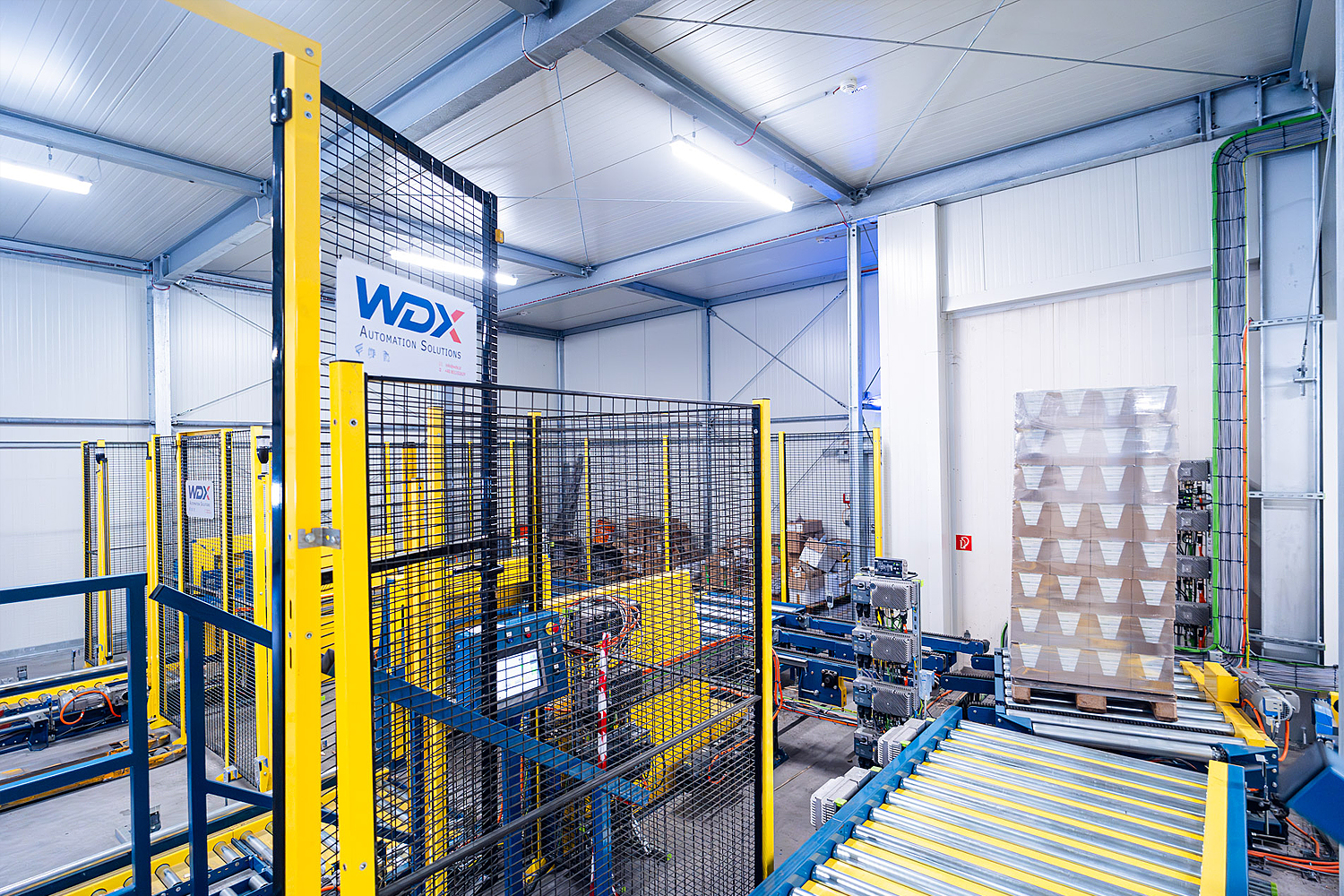
Dobrze zorganizowane procesy produkcyjne to podstawa działania każdej firmy, która zajmuje się wytwarzaniem produktów. To właśnie na tym etapie surowce zamieniają się w gotowe towary, które trafiają do sklepów i w ręce klientów. Skuteczne zarządzanie procesami produkcyjnymi to ważny element sukcesu, bo ma bezpośredni wpływ na to, jak firma radzi sobie na rynku oraz czy jest w stanie utrzymać rentowność i szybko reagować na zmiany.
Optymalizacja procesów produkcyjnych to coś więcej niż tylko poprawa wydajności. To także obniżenie kosztów operacyjnych osiągane przez eliminację niepotrzebnych działań i lepsze wykorzystanie dostępnych zasobów, mniejsze straty materiałowe dzięki dokładnemu planowaniu i lepszej kontroli jakości oraz sprawniejszy łańcuch dostaw poprzez lepszą koordynację działań i przepływ informacji. W praktyce można wyróżnić kilka podstawowych rodzajów procesów produkcyjnych. Wybór konkretnego z nich zależy od charakteru działalności firmy i specyfiki wytwarzanego produktu. Każdy typ ma swoje unikalne cechy i najlepiej sprawdza się w określonych branżach.
Podstawy procesów produkcyjnych
Procesy produkcyjne polegają na przekształcaniu surowców w produkty, które spełniają określone wymagania jakościowe i funkcjonalne. Wszystko zaczyna się od zaplanowania, czyli ustalenia, co i kiedy należy wyprodukować oraz jakie zasoby będą do tego potrzebne. Kolejnym krokiem jest zaopatrzenie, czyli pozyskanie odpowiednich materiałów w odpowiednim czasie i jakości. Gdy wszystko jest gotowe, zaczyna się właściwa produkcja fizyczna obróbka surowców według określonej technologii. Gotowy produkt trzeba jeszcze odpowiednio zapakować, by był bezpieczny w transporcie i dobrze się prezentował. Ostatnim etapem jest dystrybucja, czyli dostarczenie produktu do odbiorcy. I co najważniejsze, wszystkie te działania muszą być ze sobą dobrze skoordynowane. Nawet niewielki błąd w jednym miejscu może wpłynąć na całą linię, opóźnić produkcję, obniżyć jakość lub zwiększyć koszty. Na przykład w branży spożywczej spóźniona dostawa surowców może oznaczać, że produkt straci świeżość i nie trafi na rynek na czas.
Warto też rozróżnić pojęcie procesu produkcyjnego i technologicznego, choć często są używane zamiennie. Proces technologiczny dotyczy samego przekształcania surowców w produkt. Jest to etap, na którym surowce są obrabiane, formowane czy składane. Proces produkcyjny natomiast to coś znacznie więcej. Obejmuje wszystkie działania towarzyszące, takie jak transport, magazynowanie, kontrola jakości czy logistyka. Proces technologiczny odpowiada za samo wytwarzanie produktu. To wtedy surowce zamieniają się w gotowy wyrób, ale żeby wszystko działało tak, jak trzeba, potrzebne są też inne elementy, czyli dobre planowanie, sprawna logistyka, kontrola jakości i organizacja całego przebiegu pracy, bo dopiero wtedy tworzą dobrze działający system, dzięki któremu firma może produkować skutecznie i bez zbędnych przestojów.
Sprawdź też: System produkcyjny – podstawa efektywności operacyjnej.
Najważniejsze elementy procesu produkcyjnego
Proces produkcyjny to organizacja działań, które muszą ze sobą współgrać, żeby z surowców powstał gotowy produkt. Najważniejsze z nich to przetwarzanie materiałów, kontrola jakości, logistyka i magazynowanie. Każdy z tych elementów ma swoje zadanie – od obróbki i pomiarów, przez zapewnienie dostępności surowców, aż po sprawne przemieszczanie ich w odpowiednim czasie i miejscu. Dobrze dobrane technologie i narzędzia wpływają nie tylko na jakość produktu, ale także na to, czy firma będzie w stanie konkurować na rynku.
Proces technologiczny jako centrum całej produkcji
To właśnie w procesie technologicznym surowce zmieniają się w produkt końcowy. W zależności od branży mogą to być takie działania jak cięcie, formowanie, obróbka cieplna, fermentacja czy suszenie. Coraz częściej wykorzystywane są też nowoczesne technologie i automatyzacja, które nie tylko przyspieszają produkcję, ale też zmniejszają straty materiałowe i poprawiają jakość. Dobrze zaprojektowana linia produkcyjna potrafi znacząco zwiększyć wydajność, co przynosi przedsiębiorstwu realne oszczędności i przewagę konkurencyjną.
Procesy wspierające – ciche zaplecze produkcji
Oprócz samego wytwarzania ważną rolę odgrywają procesy, które wspierają główną produkcję. To m.in. transport wewnętrzny, który pozwala szybko przemieszczać surowce i półprodukty między stanowiskami oraz magazynowanie, dzięki któremu wszystko znajduje się na swoim miejscu i jest dostępne wtedy, gdy potrzeba. Nie można też pominąć kontroli jakości, ponieważ to ona pozwala wyłapać błędy na wczesnym etapie i dbać o zgodność wyrobów z normami i oczekiwaniami klientów.
Jakość i logistyka w nowoczesnej produkcji
W nowoczesnym zakładzie produkcyjnym sprawna logistyka, dobrze zorganizowane magazyny i precyzyjna kontrola jakości są nie mniej ważne niż sama linia produkcyjna. Transport wewnętrzny i zewnętrzny pozwala utrzymać ciągłość pracy, a dokładne pomiary i nadzór nad jakością chronią przed reklamacjami i stratami. Coraz więcej firm sięga też po inteligentne systemy monitorujące, które w czasie rzeczywistym analizują dane i pomagają szybko reagować na problemy. To inwestycja, która może znacząco poprawić wydajność i stabilność całego procesu.
Typy organizacji procesów produkcyjnych
W przemyśle organizacja procesów produkcyjnych przybiera różne formy, zależnie od charakteru działalności, metod pracy oraz zastosowanych technologii. Każdy z tych elementów wpływa na tempo, elastyczność i koszty produkcji. Wybór odpowiedniego modelu nie może być przypadkowy. To strategiczna decyzja, która może zapewnić firmie przewagę konkurencyjną lub doprowadzić do jej porażki.
Linia produkcyjna i jej zastosowanie
Jednym z najczęściej stosowanych modeli jest linia produkcyjna. W tym układzie produkt przemieszcza się przez kolejne, ściśle zaplanowane stanowiska robocze. Taka sekwencyjna struktura umożliwia standaryzację procesów, co skutkuje wysoką powtarzalnością i efektywnością. Model ten sprawdza się szczególnie w produkcji masowej, np. w przemyśle motoryzacyjnym, gdzie najważniejsze są tempo, jakość i niskie koszty jednostkowe. Dzięki automatyzacji i precyzyjnemu harmonogramowi możliwe jest ograniczenie błędów oraz redukcja strat materiałowych.
Przepływ ciągły i jego wpływ na efektywność
Przepływ ciągły to sposób produkcji, w którym wszystko idzie płynnie i bez przerw. Nie można zatrzymać procesu ani wyjąć produktu w trakcie. Sprawdza się tam, gdzie liczy się ciągłość, np. w hutnictwie, przemyśle chemicznym czy produkcji szkła. Dzięki temu unika się przestojów, marnotrawstwa i lepiej wykorzystuje zasoby. Ten model pasuje do firm nastawionych na niezawodność, precyzję i dużą skalę.
Rodzaje produkcji – która dla kogo?
W zależności od potrzeb rynku firmy mogą wybrać różne modele produkcji:
- na zamówienie – zaczyna się dopiero, gdy klient czegoś chce. Daje pełną personalizację. Na przykład meble na wymiar,
- na miejscu – produkcja lub montaż odbywa się tam, gdzie ma być efekt końcowy. Model typowe np. w budownictwie,
- jednostkowa – tworzenie pojedynczych sztuk, często bardzo złożonych. Model, w którym potrzebna jest duża elastyczność,
- seryjna – robienie partii produktów. Dobry balans między różnorodnością a kosztami,
- masowa – ogromna skala, automatyzacja, powtarzalność. Najlepsza do rzeczy codziennego użytku, jak napoje czy kosmetyki.
Planowanie i przygotowanie produkcji
Dobrze zaplanowana produkcja to podstawa. Na tym etapie zapadają najważniejsze decyzje: co robimy, kiedy i jak. Bez konkretnego planu łatwo o opóźnienia, chaos, marnowanie materiałów i niezadowolenie klientów. Planowanie to nie biurokracja tylko strategia, która wpływa na cały proces, aż po dostawę gotowego produktu.
Planowanie produkcji i harmonogramowanie operacji
Planowanie produkcji polega na ustaleniu kolejności i terminów działań. Dobry harmonogram sprawia, że wszystko idzie sprawnie, bez przestojów i strat. Tam, gdzie wszystko musi być idealnie zsynchronizowane, nawet małe opóźnienie może sporo kosztować. Dlatego plan to przewaga, ponieważ pozwala lepiej zarządzać czasem, ludźmi i zasobami.
Projektowanie technologii produkcji i marszruty
Na tym etapie tworzy się szczegółową instrukcję wykonania produktu – krok po kroku. Marszruta to mapa całego procesu:
- co robimy i w jakiej kolejności,
- gdzie się to odbywa,
- ile trwa każda czynność,
- jakie narzędzia i materiały są potrzebne.
Dzięki temu każdy produkt powstaje według tych samych standardów, a to ma ogromne znaczenie tam, gdzie liczy się precyzja i jakość, np. w elektronice, medycynie czy lotnictwie.
Techniczne przygotowanie produkcji
Na tym etapie zapadają decyzje dotyczące wszystkich aspektów produkcji: dobierane są odpowiednie maszyny, urządzenia, narzędzia oraz technologie. Ważne jest również ustawienie właściwych parametrów produkcji. Dobrze dobrane rozwiązania, takie jak odpowiednia frezarka czy system chłodzenia, mogą znacznie skrócić czas pracy oraz zmniejszyć zużycie materiałów, co przekłada się na oszczędności i poprawę niezawodności procesu.
Zarządzanie jakością w procesach produkcyjnych
W dzisiejszych czasach skuteczne zarządzanie jakością jest absolutną koniecznością, nie opcją. Firmy, które nie dbają o jakość, nie mają szans na długotrwały rozwój. System jakości działa w cyklu: planowanie, kontrola, analiza i usprawnianie, co pozwala na ciągłe doskonalenie procesu. Dzięki temu firma może ograniczyć liczbę błędów, poprawić efektywność operacyjną, budować silną markę i utrzymywać wysoką satysfakcję klientów. To właśnie nieustanne usprawnianie sprawia, że firma może się wyróżnić i utrzymać lojalność klientów.
Kontrola jakości i jej znaczenie
Kontrola jakości to element, który dba o to, by produkcja przebiegała zgodnie z ustalonymi normami. W jej ramach przeprowadza się różne działania, jak inspekcje wizualne, testy funkcjonalne i badania wytrzymałościowe. Celem jest wychwycenie wszelkich niezgodności jeszcze przed wysłaniem produktu do klienta, aby uniknąć reklamacji i zachować dobrą reputację. Coraz częściej pomocne w tym zadaniu stają się nowoczesne technologie, takie jak kamery wizyjne, które automatycznie wykrywają mikropęknięcia w częściach silników. Maszyny wykonują te zadania szybciej i precyzyjniej niż ludzie, co poprawia jakość i bezpieczeństwo produktów.
Procesy pomiarowo-kontrolne w praktyce
W codziennej produkcji procesy pomiarowo-kontrolne mają kluczowe znaczenie dla zapewnienia jakości. Polegają na systematycznym porównywaniu parametrów produktów z ustalonymi normami i szybkim reagowaniu na wszelkie odchylenia. Precyzja jest tu niezbędna, ponieważ nawet najmniejsze różnice mogą wpływać na funkcjonalność i bezpieczeństwo produktów. Dlatego coraz częściej stosuje się zautomatyzowane systemy, które w czasie rzeczywistym zbierają dane, analizują wyniki i umożliwiają natychmiastową reakcję na wykryte nieprawidłowości. W produkcji seryjnej, gdzie liczy się każda sekunda, takie rozwiązania są nieocenione.
Optymalizacja i doskonalenie procesów produkcyjnych
W dzisiejszych czasach nie wystarczy produkować – trzeba produkować mądrze. Firmy, które chcą się utrzymać na rynku, muszą stale poprawiać swoje procesy. Automatyzacja to jedno z narzędzi, które nie tylko przyspiesza produkcję, ale też zmniejsza liczbę błędów, ogranicza straty i poprawia satysfakcję klientów. Mniej poprawek, mniej marnotrawstwa, szybsze dostawy – to wszystko wpływa na to, jak firma jest postrzegana i jak radzi sobie na konkurencyjnym rynku.
Optymalizacja procesów produkcyjnych – cele i metody
Chodzi przede wszystkim o to, by produkować sprawniej, taniej i lepiej. Zwiększenie wydajności, obniżenie kosztów i poprawa jakości to cele, które dzisiaj są już nie tyle ambicją, co koniecznością. I choć brzmi to jak wyzwanie, wiele firm z powodzeniem wdraża podejścia, które im to umożliwiają. Najpopularniejsze to Lean Manufacturing i Just-in-Time – obie metody skupiają się na eliminowaniu marnotrawstwa i lepszym wykorzystaniu dostępnych zasobów. W efekcie łatwiej uporządkować pracę, szybciej reagować na zmiany i uniknąć chaosu w procesie produkcji.
Lean Manufacturing – eliminacja marnotrawstwa
Lean to sposób myślenia, który uczy, jak usuwać z procesu wszystko, co zbędne. Mowa tu o nadprodukcji, przestojach, niepotrzebnym transporcie czy zbyt dużych zapasach. Kluczem jest podejście „krok po kroku” – czyli ciągłe, drobne usprawnienia, które w dłuższej perspektywie robią ogromną różnicę. Czasem wystarczy przestawić stanowiska pracy, żeby skrócić czas przejścia między operacjami. Efekty? Mniej strat, więcej porządku i większa wydajność – niezależnie od branży.
Just-in-Time (JIT) – produkcja bez zapasów
Just-in-Time to podejście, w którym materiały i komponenty trafiają na produkcję dokładnie wtedy, gdy są potrzebne – ani wcześniej, ani później. Dzięki temu firma może ograniczyć zapasy w magazynie, zmniejszyć koszty ich przechowywania i poprawić swoją płynność finansową. Zyskuje też większą elastyczność i łatwiej dostosowuje się do zmieniających się zamówień czy potrzeb klientów. W szybko zmieniającym się otoczeniu biznesowym JIT pozwala działać zwinnie i sprawnie. Gdy połączy się go z filozofią Lean, powstaje wyjątkowo skuteczne podejście do zarządzania produkcją – takie, które pomaga ograniczać koszty, poprawiać jakość i szybciej dostarczać gotowe wyroby.
Procesy utylizacyjne i gospodarka odpadami
Ekologia stała się stałym elementem strategii firm, a odpowiedzialne zarządzanie odpadami i procesy utylizacyjne są tego ważną częścią. Wdrażanie nowoczesnych rozwiązań w tym obszarze przynosi wiele korzyści:
- ochronę środowiska naturalnego,
- możliwość odzyskiwania wartości z odpadów,
- obniżenie kosztów zakupu surowców,
- wzmacnianie pozytywnego wizerunku firmy.
Dobrym przykładem jest ponowne wykorzystanie odpadów poprodukcyjnych, co zmniejsza zapotrzebowanie na nowe materiały. Coraz częściej stosuje się też inteligentne systemy segregacji czy recykling chemiczny, które otwierają nowe perspektywy dla zrównoważonej produkcji.
Automatyzacja i cyfryzacja produkcji
Firmy coraz śmielej inwestują w automatyzację i technologie cyfrowe, chcąc nadążyć za wymaganiami współczesnego rynku. To nie chwilowa moda, lecz realna konieczność. Automatyzacja nie tylko zwiększa tempo i precyzję produkcji, ale też ogranicza błędy i obniża koszty operacyjne. Cyfrowe rozwiązania stają się podstawą nowoczesnych strategii – pozwalają działać szybciej, elastyczniej i bardziej efektywnie. W erze Przemysłu 4.0 brak inwestycji w rozwój technologiczny oznacza jedno: zostanie w tyle za konkurencją.
Automatyzacja procesów produkcyjnych – korzyści i wyzwania
Automatyzacja to prawdziwa rewolucja na hali produkcyjnej. Wprowadzenie nowoczesnych maszyn i systemów sterowania pozwala firmom osiągać znacznie lepsze wyniki w codziennej pracy. Do najważniejszych korzyści należą:
- zwiększenie wydajności dzięki redukcji przestojów i lepszemu wykorzystaniu maszyn,
- zmniejszenie kosztów operacyjnych przez ograniczenie strat materiałowych i zużycia energii,
- poprawa jakości produktów dzięki precyzji i powtarzalności procesów,
- większe bezpieczeństwo pracowników, którzy są mniej narażeni na ryzykowne czynności.
Dobrym przykładem jest przemysł motoryzacyjny, gdzie roboty spawalnicze wykonują tysiące takich samych operacji każdego dnia niemal bez błędów, co przekłada się na wysoką jakość i powtarzalność wyrobów.
Jednocześnie wdrożenie automatyzacji to nie tylko zyski, ale także konkretne wyzwania:
- konieczność przeszkolenia pracowników, którzy muszą nauczyć się obsługi nowych technologii,
- zmiany w organizacji pracy i strukturze decyzyjnej firmy,
- konieczność inwestowania w nowoczesną infrastrukturę, co może być trudne zwłaszcza dla mniejszych przedsiębiorstw.
Mimo tych barier, firmy, które decydują się na automatyzację, zyskują dostęp do zupełnie nowych możliwości rozwoju – a to często decyduje o ich przewadze konkurencyjnej.
Systemy ERP i ich rola w zarządzaniu produkcją
Systemy ERP (Enterprise Resource Planning) to fundament nowoczesnego zarządzania produkcją. Integrują dane z całej organizacji – od zaopatrzenia, przez produkcję, aż po logistykę – umożliwiając sprawne planowanie, kontrolę i optymalizację działań.
Korzyści z wdrożenia ERP są konkretne i odczuwalne:
- dokładniejsze harmonogramowanie zleceń i lepsze planowanie produkcji,
- efektywniejsze wykorzystanie zasobów – ludzi, maszyn i materiałów,
- szybsza reakcja na zmiany popytu lub awarie,
- mniej błędów dzięki eliminacji ręcznego przetwarzania danych.
ERP często współpracuje z innymi systemami, np. MES, tworząc spójne środowisko zarządzania produkcją w czasie rzeczywistym. To nie tylko technologia – to sposób na podejmowanie trafnych decyzji w oparciu o dane, a nie przeczucia.
Systemy MES – monitorowanie produkcji w czasie rzeczywistym
MES (Manufacturing Execution Systems) to systemy, które pozwalają śledzić to, co dzieje się na hali produkcyjnej w czasie rzeczywistym. Pokazują postęp prac, wychwytują wąskie gardła i umożliwiają natychmiastową reakcję na nieprawidłowości.
Przykład? Gdy zatrzymuje się linia montażowa, MES natychmiast powiadamia odpowiednie osoby i rejestruje zdarzenie. Połączony z ERP czy systemem CAD/CAM, tworzy spójny przepływ danych, który wspiera płynność i elastyczność produkcji.
Dostęp do bieżących informacji stał się dziś standardem. Bez niego trudno mówić o efektywnym zarządzaniu procesami.
Integracja CAD/CAM – od projektu do wykonania
Systemy CAD/CAM (Computer-Aided Design / Computer-Aided Manufacturing) łączą projektowanie z produkcją, umożliwiając szybkie przejście od koncepcji do realizacji. Dzięki nim można tworzyć dokładne projekty i bezpośrednio sterować maszynami, minimalizując błędy i oszczędzając czas.
W branżach takich jak lotnictwo, medycyna czy precyzyjna mechanika, gdzie margines błędu praktycznie nie istnieje, CAD/CAM to podstawa. Automatyczne generowanie ścieżek obróbki i integracja z CNC pozwalają znacząco podnieść jakość produktów i skrócić czas produkcji.
System meldunków zwrotnych – kontrola postępu produkcji
System meldunków zwrotnych to coś w rodzaju pulpitu sterowniczego – pozwala śledzić, co się dzieje na hali i na bieżąco reagować. Kierownictwo widzi, czy wszystko idzie zgodnie z planem i może szybko zareagować, jeśli coś odbiega od normy. Działa to w praktyce tak: MES zbiera dane prosto z maszyn i stanowisk roboczych. Dzięki temu:
- łatwiej zrozumieć, co dzieje się w procesie,
- lepiej kontrolować wykonanie planu,
- od razu widać, gdzie coś poszło nie tak,
- szybciej podejmuje się decyzje, co poprawia wydajność.
To proste – jeśli chcesz mieć pełną kontrolę nad produkcją, musisz wiedzieć, co się dzieje w czasie rzeczywistym.
Procesy okołoprodukcyjne i ich znaczenie
Współczesny przemysł to nie tylko maszyny i linie produkcyjne. Równie ważne – a czasem ważniejsze – są działania, które dzieją się wokół samej produkcji. Nazywamy je procesami okołoprodukcyjnymi. Choć często nie rzucają się w oczy, to właśnie one decydują o tym, czy produkcja działa sprawnie, bez przestojów i strat.
Do najważniejszych procesów należą:
- logistyka – odpowiada za to, żeby surowce dotarły na czas, a gotowe produkty szybko trafiły do odbiorcy,
- konserwacja – zapobiega awariom, usuwa drobne usterki, zanim zamienią się w poważne problemy,
- zarządzanie magazynem – dba o porządek, optymalne wykorzystanie przestrzeni i sprawne wydawanie towaru,
- kontrola jakości – wychwytuje błędy, zanim produkty opuszczą firmę. Dzięki temu nie wracają jako reklamacje.
Bez tych działań nawet najlepsza linia produkcyjna może stanąć. Procesy okołoprodukcyjne to zaplecze, które pozwala produkcji działać równo, bez niespodzianek i zbędnych kosztów.
Logistyka, konserwacja i inne działania wspierające
Wśród procesów wspierających szczególne znaczenie mają logistyka i konserwacja. To one utrzymują produkcję w ruchu i zapobiegają kosztownym przestojom.
Logistyka odpowiada za to, by odpowiednie komponenty trafiały na linię produkcyjną dokładnie wtedy, gdy są potrzebne. To nie tylko kwestia punktualności – to także:
- redukcja czasu oczekiwania,
- optymalizacja przestrzeni magazynowej,
- obniżenie kosztów operacyjnych.
W branżach takich jak motoryzacja, opóźnienie jednego elementu może zatrzymać całą linię montażową, co prowadzi do poważnych strat finansowych.
Konserwacja pełni funkcję „systemu odpornościowego” zakładu. Dzięki regularnym przeglądom, diagnostyce i szybkiej reakcji na usterki:
- maszyny pracują bez zakłóceń,
- produkcja nie traci tempa,
- minimalizowane są ryzyka awarii,
- wydłuża się żywotność sprzętu.
Nie można też pominąć znaczenia zarządzania magazynem i kontroli jakości. Pierwsze wpływa na sprawność kompletowania zamówień i dostępność komponentów, drugie – na eliminację błędów i utrzymanie wysokiego standardu produktów. Każdy z tych procesów ma realny wpływ na końcowy wynik produkcji.
Wpływ procesów okołoprodukcyjnych na efektywność produkcji
Procesy okołoprodukcyjne są fundamentem efektywnej produkcji. To one sprawiają, że cały system działa płynnie, bez zakłóceń i nieprzewidzianych przestojów. Gdy logistyka przebiega bez zarzutu, konserwacja zapobiega awariom, kontrola jakości wyłapuje błędy, a magazyn funkcjonuje jak dobrze naoliwiona maszyna – cała produkcja staje się bardziej przewidywalna, wydajna i opłacalna. W praktyce zapewnia to mniej marnotrawionych materiałów, szybszą realizację zamówień, zadowolonych klientów i lepsze wykorzystanie dostępnych zasobów. To nie są drobne korzyści – to realna różnica, którą czuć w wynikach. Firmy, które świadomie rozwijają obszary wspierające produkcję, budują sobie silną przewagę nad konkurencją. Zyskują nie tylko dzięki niższym kosztom – równie ważna jest elastyczność, umiejętność szybkiego reagowania na zmiany w otoczeniu rynkowym, a także większa kontrola nad jakością i terminowością realizacji zleceń.
Przyszłość procesów produkcyjnych
W dobie dynamicznych przemian przemysłowych, przyszłość produkcji opiera się na trzech filarach: cyfryzacji, automatyzacji oraz zrównoważonym rozwoju. To właśnie one wyznaczają nowe standardy i kierunki rozwoju, którymi podążają nowoczesne przedsiębiorstwa. Dzięki nim możliwa jest transformacja, która jeszcze dekadę temu wydawała się nierealna.
Cyfryzacja to precyzyjne zarządzanie danymi, optymalizacja procesów w czasie rzeczywistym oraz pełna kontrola nad każdym etapem produkcji. Automatyzacja zwiększa nie tylko wydajność, ale również zapewnia powtarzalność i niezawodną jakość. Zrównoważony rozwój natomiast stał się koniecznością. Firmy, które chcą liczyć się na rynku, muszą działać odpowiedzialnie – nie tylko dla zysku, ale również z poszanowaniem środowiska i przyszłych pokoleń.
Innowacje i rozwój technologii w produkcji
Technologia nie zwalnia, przemysł zmienia się z dnia na dzień. Innowacje takie jak sztuczna inteligencja (AI), robotyzacja czy Internet Rzeczy (IoT) rewolucjonizują sposób planowania i realizacji produkcji. Otwierają drzwi do nowych możliwości, które jeszcze niedawno wydawały się odległe. Przykładem są czujniki IoT, które umożliwiają bieżące monitorowanie stanu maszyn, przewidywanie awarii, minimalizowanie przestojów.
Zdolność do wdrażania innowacji to atut, bo jeśli nie idziesz na przód to zostajesz w tyle. A konkurencja nie czeka.
Sprawdź również: Co to jest Robot AMR?
Wyzwania i kierunki rozwoju procesów produkcyjnych – podsumowanie
Przyszłość nie będzie łatwa. Przedsiębiorstwa muszą przygotować się na coraz bardziej złożone i dynamiczne warunki rynkowe. Elastyczność w zarządzaniu produkcją to już nie przewaga konkurencyjna tylko warunek przetrwania. Nowe technologie, takie jak druk 3D (produkcja addytywna) czy systemy predykcyjne oparte na analizie danych, wymagają nie tylko inwestycji finansowych, ale również zmiany mentalności. Dodatkowo rośnie presja na odpowiedzialność środowiskową. Redukcja emisji CO₂, efektywne zarządzanie zasobami, troska o planetę, to już nie tylko elementy strategii CSR, ale konkretne wyzwania, które trzeba podjąć tu i teraz.
Fabryki przyszłości? Być może będą bezemisyjne, w pełni zautomatyzowane i zarządzane przez inteligentne algorytmy. Brzmi jak science fiction? Może trochę. Ale wiele firm już dziś stawia pierwsze kroki w tym kierunku i to z sukcesem. Co będzie najważniejsze? Umiejętność łączenia innowacyjnych rozwiązań z odpowiedzialnym podejściem. Tylko wtedy rozwój procesów produkcyjnych będzie miał sens zarówno dla gospodarki, jak i dla środowiska, w którym żyjemy.