Top 3 procesy do zautomatyzowania za pomocą AMR
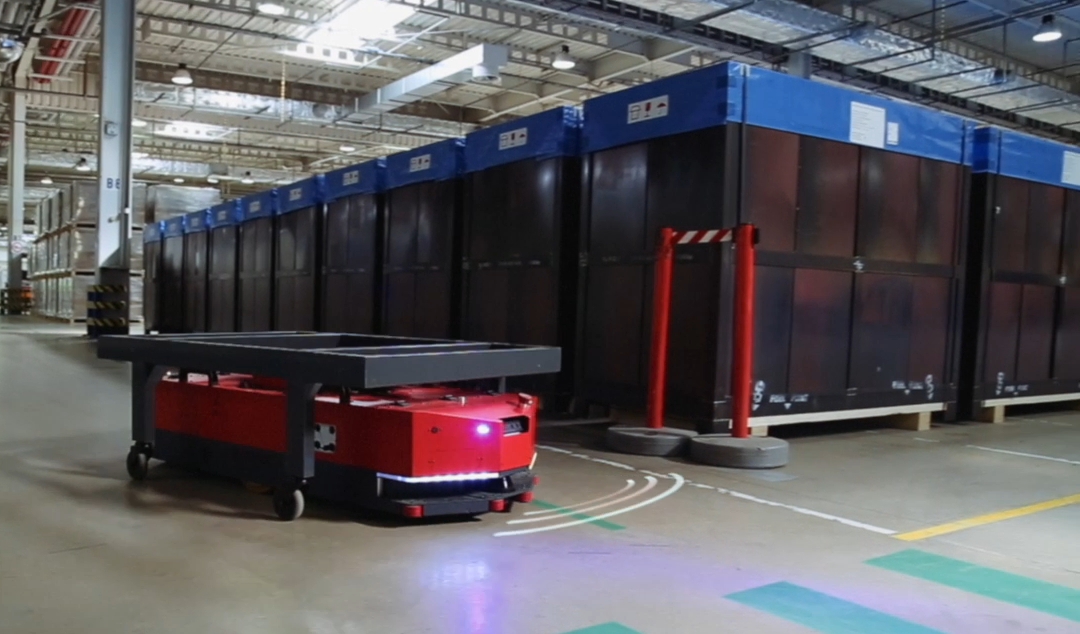
Roboty klasy AMR (Autonomous Mobile Robots) najczęściej wykonują to samo zadanie – pobierają ładunek w punkcie A, transportują go, a następnie odkładają w punkcie B. Ta prosta sekwencja działań jest kluczowa dla wielu procesów produkcyjnych i magazynowych. W tekście omówimy 3 najważniejsze procesy, których automatyzacja przy użyciu robotów AMR najsilniej wpływa na poprawę wskaźnika ROI.
Nasze roboty nie wyjadą zimą na zaśnieżony parking. Nie ma też sensu wdrażanie ich do transportu ładunków na odległość kilku metrów. Natomiast są bezkonkurencyjne wszędzie tam, gdzie mamy do czynienia z równą podłogą i koniecznością zapewnienia płynnego przemieszczania ładunków o zróżnicowanej masie czy gabarytach – mówi Mateusz Wiśniowski, CTO Robotics Expert w firmie VersaBox produkującej roboty klasy AMR.
3 obszary automatyzacji intralogistyki przemysłowej
Autonomiczne wózki transportowe coraz częściej wypierają z hal produkcyjnych wózki widłowe i ręczne paleciaki. Przyczyną jest to, że wózki widłowe stwarzają duże zagrożenie dla ludzi oraz innych pojazdów transportu bliskiego. Ograniczona widoczność, duża masa własna czy pośpiech w realizacji zadań transportowych kończą się wieloma kolizjami i groźnymi w skutkach wypadkami. W odróżnieniu od wózków widłowych, roboty AMR doskonale radzą sobie w środowisku, w którym pracują zarówno ludzie, jak i inne maszyny. Ich systemy bezpieczeństwa gwarantują pełną bezkolizyjność (ze strony robota). Małe gabaryty pozwalają robotom AMR na operowanie ciasnych w przestrzeniach, w których niemożliwe byłoby użycie innych środków transportu.
Najważniejsze procesy intralogistyczne w zakładach produkcyjnych, które można zautomatyzować przy użyciu robotów AMR, dotyczą trzech stref:
- Transport materiałów z magazynu do hali produkcyjnej
To obszar o największym potencjale optymalizacji. Organizacja dostaw z użyciem AMR jest w pełni bezobsługowa. W efekcie staje się płynna, przewidywalna, niezawodna oraz mierzalna. Zależnie od potrzeby robot może dostarczać do gniazd produkcyjnych jeden rodzaj materiału lub oferować różnorodny asortyment i zaopatrywać w czasie jednego przejazdu wiele gniazd produkcyjnych.
- Transport pomiędzy gniazdami produkcyjnymi
Konieczność wytwarzania wielu wariantów jednego produktu sprawia, że współczesne procesy przemysłowe są w coraz większym stopniu nieliniowe. Wędrówka powstającego wyrobu pomiędzy określonymi gniazdami produkcyjnymi jest zależna od tego, jaki efekt finalny chcemy uzyskać. Inną drogę odbywa samochód z silnikiem benzynowym, inną z jednostką wysokoprężną, a jeszcze inną z napędem hybrydowym. Często nowy pakiet wyposażenia czy nowa jednostka napędowa pojawia się po uruchomieniu produkcji seryjnej i trzeba szybko stworzyć nowe gniazdo produkcyjne. Modyfikacje mogą być też wymuszone zmiennością zapotrzebowania rynku na określone modele czy wersje wyposażenia.
Szybkie oraz relatywnie tanie przezbrojenie linii produkcyjnej jest możliwe tylko wtedy, gdy za transport powstającego produktu i dostarczanie potrzebnych komponentów odpowiadają roboty AMR. Ta sama operacja w przypadku transportu opartego na przenośnikach taśmowych byłaby bez porównania bardziej czasochłonna i kosztowna. Dzięki niewielkim rozmiarom roboty AMR mogą docierać głęboko do gniazd produkcyjnych. Podobnych wyników nie da się osiągnąć przy użyciu dużych i ciężkich wózków widłowych. Z kolei pociągi logistyczne są w praktyce niezwrotne – nie cofają i nie są w stanie wykonać nawrotu w miejscu. Pozostaje użycie transportu ręcznego, który jest obarczony wieloma ograniczeniami. Wynikają one z przepisów prawa pracy oraz trudności z pozyskaniem kadry.
- Transport pomiędzy halą produkcyjną a magazynem wyrobów gotowych
Zadania są bardzo podobne, jak w przypadku transportu materiałów z magazynu do hali produkcyjnej. Robot lub grupa robotów AMR może realizować transport w modelu przypominającym milk run – może odbierać towary z wielu gniazd produkcyjnych i dostarczany do magazynu wyrobów gotowych. Możliwe jest śledzenia numerów referencji i aktualnego położenia każdej transportowanej palety. Natomiast od systemu WMS (Warehouse Management Software) zależy skierowanie palety do odpowiedniego magazynu albo bezpośrednio do strefy kompletacji lub na spedycję.
3 typy transportu wewnętrznego najbardziej podatne na automatyzację
Autonomiczne wózki transportowe mają coraz mniejszą konkurencję w transporcie poziomym. Bez trudu przejmują zadania innych maszyn transportu bliskiego. Oto trzy procesy, które idealnie nadają się do automatyzacji przy użyciu robotów AMR:
- transport palet pobieranych z podajnika – roboty VERSABOT doskonale nadają się do tego zadania ze względu na niewielkie gabaryty. Szerokość robota jest mniejsza niż szerokość standardowego podajnika rolkowego, dzięki czemu wdrożenie VERSABOTÓW nie wymaga kosztownego rozszerzania stanowisk,
- transport na wózkach – ładunek nie jest umieszczony bezpośrednio na robocie, lecz na wózku, dla którego robot AMR jest jednostką napędową. Jeden robot może obsługiwać dużą liczbę różnych wózków, co jest bardzo ekonomicznym rozwiązaniem przy dużej różnorodności i częstych zmianach asortymentu transportowanych towarów, a jednocześnie niewielkich ilości transportowanych ładunków – robot może dostarczać wózek pełny, a odbierać pusty i w ten sposób ograniczyć liczbę pustych przejazdów bez wózka,
- transport elementów podwieszanych na ramach – specjalna zabudowa do transportu wieszaków, które robot automatycznie pobiera ze standardowych szyn podwieszanych wykonanych ze stali: w ten sposób można transportować ciężkie elementy stalowe, ale równie dobrze robot AMR może „zatrudnić się” w przemyśle odzieżowym i przewozić ubrania na wieszakach.
Doskonały ROI i niskie ryzyko inwestycyjne
W przypadku robotów klasy AMR nie musimy wdrażać od razu floty złożonej z kilkunastu czy kilkudziesięciu maszyn. Można zacząć od jednego robota. Ponadto wdrożenie nie wymaga zmian w architekturze obiektu. W efekcie ryzyko inwestycyjne jest znacząco mniejsze niż przy innych rozwiązaniach logistycznych. Mniejsze jest też prawdopodobieństwo powstania zakłóceń w procesach produkcyjnych. Wszystko to sprawia, że testowanie możliwości robota AMR staje się w pełni bezpieczne w kontekście finansów firmy i zachowania ciągłości produkcji.
Nie mniej atrakcyjnie przedstawia się sytuacja z ROI, czyli zwrotem inwestycji. Jeżeli fabryka czy magazyn pracuje w systemie trójzmianowym, to jeden AMR zastępuje co najmniej trzech pracowników. Do tego należy doliczyć koszty leasingu lub zakupu wózka widłowego oraz wydatki na jego utrzymanie i serwis. W takich warunkach czas zwrotu inwestycji w transport oparty na wózkach AMR waha się w przedziale zaledwie 18-24 miesięcy.