Jak optymalizować procesy intralogistyczne?
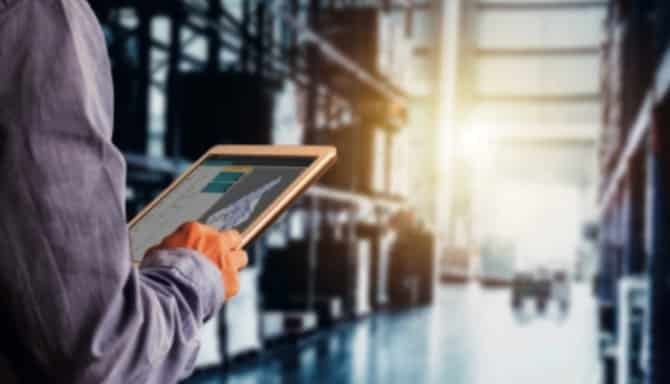
Wyzwaniem dla producentów robotów klasy AMR (ang. Autonomous Mobile Robot) nie jest już tylko zbudowanie niezawodnej, wydajnej i bezpiecznej maszyny. Konstrukcje oraz możliwości autonomicznych robotów są na tyle zaawansowane, aby mogły zdominować procesy intralogistyczne w halach produkcyjnych i magazynach. Na przeszkodzie staje problem organizacji ruchu robotów, co w praktyce objawia się m.in. korkami do złudzenia przypominającymi uliczne. Rozwiązaniem są optymalizatory procesów intralogistycznych.
Nasze roboty z serii VERSABOT 500 i VERSABOT 1000 doskonale radzą sobie z samodzielnym, w pełni autonomicznym budowaniem mapy środowiska – mówi Jakub Michalski, Chief of Sales & Business Development w VersaBox. – Samodzielnie wytyczają trasy, wymieniają się informacjami i sprawnie pokonują przeszkody. Naszym celem jest maksymalne wykorzystanie możliwości nie tylko poszczególnych maszyn, lecz potencjału floty robotów, traktowanej jako jeden mechanizm. W tym celu stworzyliśmy system Autonomy@Work – optymalizator, a dokładnie wyspecjalizowane narzędzie do projektowania i modelowania multirobotycznych procesów intralogistycznych.
Celem optymalizacji jest udrożnienie systemu, rozładowanie korków i zapobieganie ich powstawaniu. Wszystko po to, aby robot jak najdłużej był w ruchu oraz miał jak najmniej przestojów wynikających z:
- oczekiwania na ładowanie baterii,
- możliwość pobrania czy zdania ładunku,
- możliwość ominięcia przeszkody na trasie przejazdu.
Jak powstaje optymalizator ruchu robotów?
Optymalizator to rodzaj oprogramowania, które umożliwia stworzenie wirtualnego bliźniaka realnej hali magazynowej czy produkcyjnej. Po odwzorowaniu layoutu przestrzeni, która ma być optymalizowana, konstruuje się odpowiedniki realnych robotów i innych pojazdów.
Po przygotowaniu „sceny” i „aktorów” należy rozdać wszystkim role, a następnie rozpocząć reżyserowanie „spektaklu”. Im lepszy był scenariusz (dane na temat realnego funkcjonowania transportu wewnętrznego w analizowanym środowisku), tym lepsze będą wyniki „spektaklu”, czyli symulacji funkcjonowania procesów na wirtualnym modelu. Odpowiednio „nauczony” wirtualny model udzieli odpowiedzi związanych z funkcjonowaniem realnych procesów logistycznych – pozwoli np. określić liczbę niezbędnych robotów (w tym szczególnie w pikach) czy optymalną szybkość ich poruszania się. Na modelu będzie można sprawdzić współzależność poszczególnych czynników i wpływ wprowadzanych zmian na cały system logistyczny.
Jakie są cele działania optymalizatorów ruchu robotów?
Zadaniem wirtualnych modeli jest optymalizacja już działających procesów intralogistycznych, projektowanie oraz testowanie i optymalizacja nowych rozwiązań przed ich wdrożeniem. Przed tego typu oprogramowaniem stawia się trzy rodzaje zadań:
- modelowanie i projektowanie multirobotycznych procesów intralogistycznych – stworzenie wirtualnego modelu pozwala oszacować efektywność robotów, określić ich optymalną liczbę do wykonania określonych zadań oraz wskazać wąskie gardła systemu,
- ocena możliwości systemu intralogistycznego – ocena dotyczy nie tylko właściwości mechanicznych czy możliwości autonomicznego wykonywania zadań przez poszczególne roboty, lecz przede wszystkim możliwości zastosowania i efektywności systemów wielorobotycznych oraz szans wykorzystania drzemiącego w nich potencjału emergencji,
- ocena elastyczności systemu intralogistycznego – testowanie możliwości wprowadzania zmian oraz szybka ocena ich wpływu na funkcjonowanie całego systemu.
Modelowanie dotyczy nie tylko wyznaczania tras, szybkości jazdy, czasu czy miejsca ładowania. Jest też doskonałym narzędziem tworzenia scenariuszy awaryjnych, czyli np. działania systemu w pikach (w dużym przeciążeniu pracą) czy w przypadku awarii maszyn. Można opracować reguły postępowania na wypadek awarii, zanim do niej dojdzie. Cyfrowy model jest bardzo przydatnym narzędziem w pracy służb utrzymania ruchu.
Dlaczego modelowanie procesów intralogistycznych przynosi duże oszczędności?
Wdrożenia flot złożonych z kilkudziesięciu lub kilkuset robotów klasy AMR są bardzo skomplikowane. Przy dużych flotach robotów opracowanie precyzyjnego wdrożenia „ręcznie”, bez wirtualnego modelu, jest praktycznie niemożliwe. Implementacja zmian i obserwacja ich następstw, a następnie wprowadzanie korekt oraz powtarzanie tej pętli aż do osiągnięcia pożądanych efektów pociągają za sobą – w realnych warunkach przemysłowego środowiska pracy – gigantyczne koszty. Jeżeli uda się zbudować model dobrze odzwierciedlający realne środowisko pracy, można zbudować i testować system logistyczny bez konieczności uruchamiania procesów w realu. Korzyścią z takiego rozwiązania jest ogromna oszczędność czasu, pracy i wydatków na nietrafione modernizacje.
Raz stworzony cyfrowy bliźniak może towarzyszyć realnej hali produkcyjnej czy magazynowej już na stałe. Uzupełniany na bieżąco danymi, wirtualny model będzie coraz doskonalszym narzędziem optymalizacyjnym – pozwoli przetestować wszystkie planowane zmiany, ocenić ich wpływ na system oraz precyzyjnie oszacować koszty i potencjalne zyski. Co ciekawsze, obserwacja działania transportu wewnętrznego na wirtualnym modelu pozwala wychwycić prawidłowości, które umykają w obserwacji realnych procesów. Dzieje się tak m.in. dlatego, że modele potrafią przyspieszać procesy. Sprawdzenie, jaki efekt będzie miało wprowadzenie większej liczby robotów czy zmiana lokalizacji stacji ładowania baterii, w rzeczywistości zajmie godziny, czasem dni, a nawet tygodnie. Testowanie na modelu pozwala otrzymać wyniki w bardzo krótkim czasie, liczonym w minutach czy w godzinach. Przeprowadzenie analogicznych badań tradycyjnymi metodami jest rzadko stosowane z powodu gigantycznych kosztów. Korzystanie z możliwości wirtualnych bliźniaków jest nie tylko tanie, ale też komfortowe.
– Obecnie sami wprowadzamy dane i dostarczamy klientom wyniki w postaci rekomendacji optymalizacyjnych. Jednak docelowo nasz system będzie udostępniany w technologii chmurowej w modelu Software as a Service – mówi Jakub Michalski. – W zamian za opłatę abonamentową nasi klienci końcowi i podwykonawcy otrzymają możliwość samodzielnego przeprowadzania testów oraz monitorowania systemu. Stworzymy warunki do prowadzenia dowolnych analiz na podstawie danych procesowych – zarówno historycznych, jak też zbieranych i wprowadzanych do systemu w czasie rzeczywistym. Obsługa systemu będzie możliwa bez rozbudowy własnej sieci IT – wprost z poziomu dowolnego urządzenia z dostępem do Internetu.
Optymalizacja istniejących i projektowanie nowych obiektów
System modelowania procesów logistycznych można z powodzeniem zastosować nie tylko wobec istniejących obiektów, ale także na etapie projektowania nowych. Można zbudować system wewnętrznej logistyki opartej na robotach VERSABOT 500 i VERSABOT 100, przetestować je i zoptymalizować, a wyniki wykorzystać do tworzenia realnych przestrzeni. System opracowany przez Versabox pozwala sprawdzić działanie systemu intralogistyki na długo przed tym, zanim przerzucona zostanie pierwsza łopata ziemi na budowie nowego magazynu czy fabryki.