DON’T FEAR THE ROBOT
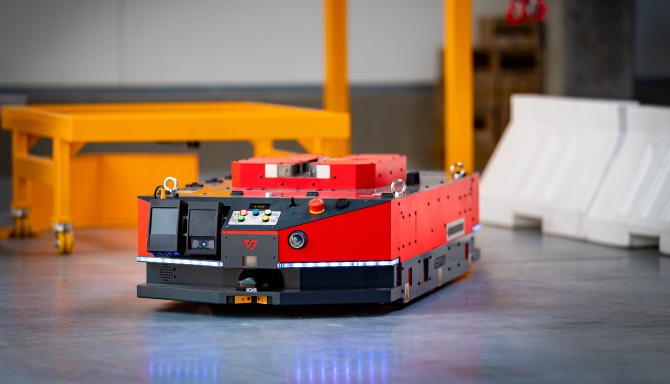
Why are autonomous machines used in intralogistics safer than people?
Robots are steadily increasing their presence in intralogistics. They take over the most burdensome and repetitive activities in warehouses and production plants, connected with the transport of loads when completing orders or delivering parts and components to production stations. Autonomous machines take on more and more tasks that have been so far performed exclusively by people. Although they are becoming more common, they still raise many doubts. The most serious of these concern the issue of security-property but, above all, people in the vicinity of robots. Should we fear robots?
It is no coincidence that many transport robots work in entirely separate areas of warehouses or production plants, to which access is limited or even prohibited for people. At the same time, work on improving and refining robots able to function safely in a shared environment is developing dynamically.
AMR – mobile, autonomous transport unit
AMR (Autonomous Mobile Robot) denotes autonomous robots used for moving various types of cargo in internal transport. The robot executes transport assignments between designated points. Its purpose is exactly the same as for a human equipped with a pallet truck or for a forklift operator. The robots operate based on guidelines similar to human workers: they receive load specifications (coordinates of its location) and coordinates of the delivery place. Both humans and robots try to use the shortest path possible. If an obstacle appears en route, the reactions of robots and humans are similar: they try to avoid it, and if that’s not possible, they look for an alternative route to their desig- nated target. They try to complete the task as quickly as possible, and at the same time fulfill all safety requirements to avoid material losses and accidents involving people. Experience shows that robots perform their tasks in a much more predictable and therefore incomparably safer way. How is this possible?
A machine is safe because it doesn’t make mistakes
Before we ask about the safety systems used in AGV robots, let’s consider the most common causes of accidents in internal transport. Research conducted in the USA shows that over 80% of accidents involving forklifts are due to insufficient visibility*. The most common accidents are collisions with pedestrians and other forklifts, forklifts getting caught on storage shelving, tipping over after driving over abandoned objects on its route or getting the mast caught on a low gate while passing under it. The causes of these accidents are inattention, noticing an obstacle too late, driving “blind” with a visibility obstructing load, and reversing without making sure there isn’t anyone or anything behind the forklift.
Would a robot make similar mistakes? An autonomous machine constantly scans its surroundings, so it can’t overlook anything. It has a programmed safety zone, i.e. the distance from obstacles that appear on its route, below which the machine executes a „safety stop”. The safe distance is dynamically determined: the higher the speed of the robot, the further from the obstacle the braking will start. All this to ensure that the braking distance is always safe. This eliminates the risk of collisions.
“VERSABOT 500 robots can also interpret the type of obstacle, distinguish a human from a loaded pallet or a forklift,” says Mateusz Wiśniowski, VersaBox CTO. “Depending on the type of obstacle, the robot waits for a change in circumstances to continue driving or calculates a new route leading to its target destination.”
Small objects, such as metal screws scattered along the route, will also not disturb the robot: it will drive over the smaller ones, and sweep aside the bigger ones using special brushes (which can be attached if necessitated by the working environment). The robot responds effectively even when we suddenly cross its path. And if you have any doubts whether everything is OK, all you have to do is hit the power button on the robot housing which halts the machine.
It is worth noting that AGV robots not only monitor their surroundings, but also inform them of their presence through sound and light signals. They see us and do everything they can to make us see them.
Can a robot “break free”?
A robot will never have a delayed reaction – its reflexes are measured in milliseconds. It doesn’t get tired or distracted, doesn’t rage at the boss or contemplate the love of its life – emotions do not interfere with its work. It doesn’t act on impulse, it’s one hundred percent predictable, and thus incomparably safer than a human and any transport ma- chines operated by them. However, like any machine, it can break down. Does a robot malfunction pose a threat to people? Can a damaged machine “break free” and, for example, ram into obstacles in its path?
“As a safety precaution, every malfunction makes the robot stops,” assures Mateusz Wiśniowski, VersaBox CTO. “Failure of any of the safety systems and even physical interference with the control systems, for example intentional damage, results in an immediate stop of the robot. This does not meen that the Robots are fragile. On the contrary – they are designed and built as truly heavy duty machines. Robots that work in warehouses and production facilities are sometimes heavily battered. This is because they are slower than forklifts and can’t run away from them, but we are already working on it,” Wiśniowski jokes.
*Causes of accidents involving forklift trucks, http://archiwum.ciop.pl/22387.html