AMR ARE ALREADY HERE, TIME FOR EFFICIENT MANAGEMENT
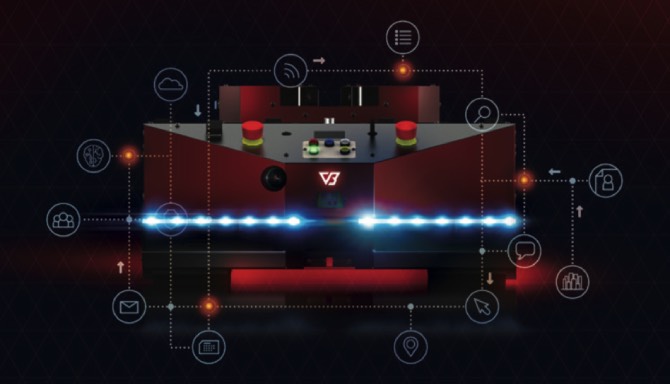
Robotisation of intralogistics. The challenge of traffic and fleet management.
When Benz-Patent Motorwagen Nummer 1 was created in 1886, everyone was excited about the fact that ‘it’ can develop a speed of 16 km/h without the help of a horse. Modern cars are able to travel 10 to 20 times faster. However, the average speed at which they travel through large city centres is not that much different from the speed achieved by the first internal combustion vehicle. The modern car, which has been perfected over the last 130 years, is inefficient because… it’s stuck in traffic jams. The producers of Autonomous Mobile Robots (AMRs) are trying to avoid making the same mistake.
The main challenge facing road traffic and intralogistics is no longer how to improve machines, but how to manage traffic itself. More efficient power sources (smaller and higher-capacity traction batteries), more precise sensors, more efficient mapping systems, and more durable suspension systems will undoubtedly get developed in the near future. AMR-class machines will be perfected over time. However, making full use of the huge potential of autonomous transport robots will depend on the efficiency of fleet and traffic management systems. This is not a task for the distant future, but a current and increasing problem.
Robot density in the industry in 2022
The need to develop effective methods of traffic management and overall performance management of robots in various sectors of the industry, in transport and other areas of the economy, is due to the exponential increase in the number of intelligent and increasingly autonomous machines.
According to the report published by the International Robotics Federation (IFR) at the end of 2019, the European average in 2018 was 114 robots per 10,000 employees. Germany has been a European leader for years, with 338 robots per 10,00 people. The global leader, Singapore, has reached an average of 831 robots per 10,000 industrial employees.
The authors of the report forecast annual increases in the number of robots at 12%, estimating that in 2022 the number of “employed” robots, including autonomous machines, will reach nearly 4 million units globally. However, it’s not known how the coronavirus pandemic will influence these numbers. It may turn out that the interest in robotisation, intensified by COVID-19, will translate into a more intense and long term saturation of various branches of the global economy with robots than predicted by the authors of the IFR report.
AMRs are already here, time for efficient management
Not so long ago, Automated Guided Vehicles (AGVs) caused a great stir by showing up in warehouses and production halls, and by being able to move along fixed routes, delivering and collecting various goods from established pickup and dropoff points. AGV trolleys and trucks orient themselves in their surroundings thanks to various types of markers installed in the hall floor. The robot knows where to go because it can recognise the colour of the line drawn on the floor, detect magnetic strips, and markers.
This kind of system is robust but not very flexible – every change in the production process requires adjusting or even creating new routes. In addition, AGVs are only able to move along previously designated paths. This means that, for example, if the route gets blocked by an abandoned load, the only thing an AGV can do is stop and wait for the obstacle to be removed.
AMRs, such as VERSABOT 500 and VERSABOT 1000, are the solution to the problem of navigating along a predefined path. They map the area themselves, create a virtual map and orient themselves in space without having to read floor markers. However, their autonomy is much broader than that. AMRs can make decisions independently, choose the best route to their destination, and avoid obstacles along their path. They can solve complex problems, such as whether it is better to choose the shortest route and get stuck in traffic, or a longer but less frequented one. The problem of organising robot traffic can be solved relatively easily when there are only several robots in an entire warehouse or production hall. However, as the number of AMRs in a warehouse increases, their movement throughout the facility starts to resemble road traffic, with all the consequences that come with this.
Robotisation of intralogistics: Intelligent road traffic and warehouse traffic management
The latest solution to decongesting cities is smart traffic management systems, which control traffic lights at intersections, suggest the best routes to drivers, map bottlenecks, and anticipate traffic problems caused by weather changes.
It’s possible to increase the number of cars that can pass through a set of roads by up to 40 %, without the need to build new roads or expand existing ones, all thanks to the use of appropriate algorithms that take advantage of ready-made operating patterns, historical data, and ongoing monitoring of the transport network. Since traffic light changes are managed by a smart algorithm, road traffic safety also increases. The algorithm prevents reckless driving and speeding between intersections.
Industrial facilities face traffic problems very similar to those plaguing big cities. Traffic jams, blocked routes, waiting for pickup and delivery point access, time loss associated with recharging – these are all problems present in warehouses and production halls. The difference, and above all the superiority of warehouse traffic over road traffic, is that robots are not guided by emotions. Therefore, they are completely predictable and safe. The same cannot be said for handling equipment operated by people. Besides, the biggest advantage of robots — autonomy — can also create serious traffic problems.
Autonomous route selection by one robot can overlap the equally autonomously selected route of another machine. The more AMRs there are, the greater the chance of repeating the situation in big city centres – during intralogistics peak times (rush hours), robots could spend most of their time in traffic jams, which they will create if not managed properly.
Let’s make a twin in the cloud
Traffic simulators have become the answer to the problems of intralogistics management based on autonomous robots. VersaBox has developed such a system. It allows you to create models based on the layout of a warehouse or a factory floor, and to “let loose” digital equivalents of AMRs and other vehicles involved in intralogistics processes. If the model is supplied with the right amount of data, we end up with a digital twin of the real facility. This solution will enable virtual testing and modelling of AMR traffic before any of them enter a real production hall or warehouse. Thanks to the ability to detect errors in the virtual model, the cost and time needed for implementation will be dramatically reduced.
Ultimately, the robot traffic modelling system will find its place in the cloud and will be made available in the Software as a Service (SaaS) model. The customer will purchase an appropriate subscription which will enable them to manage their robot fleet, including independently carrying out simulations of changes or even virtual implementations before the real ones take place. The system works well both in existing facilities and when designing new ones. It is worth noting that the use of cloud solutions does not require an investment in your own IT infrastructure – all you need is a mobile device.