AUTONOMOUS TROLLEYS IN A WAREHOUSE
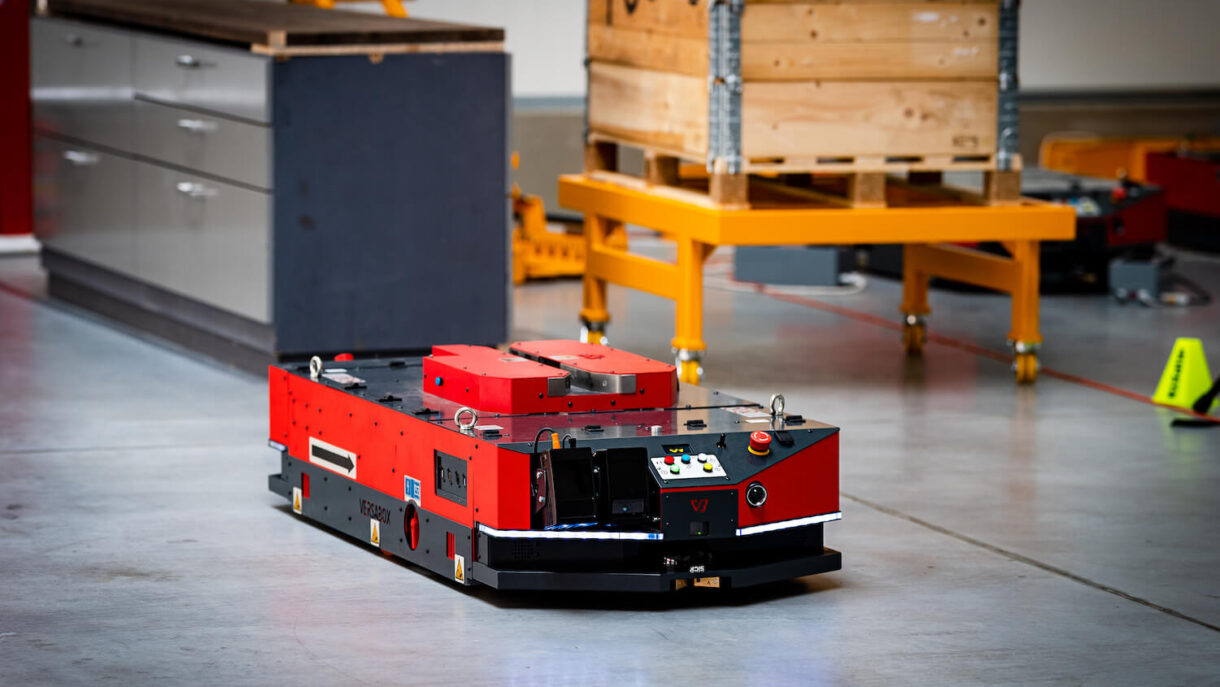
Autonomous transport trolleys, also known as Autonomous Mobile Robots (AMRs), are a modern alternative to traditional means of material handling. Their biggest advantage is the lack of an operator. This fact is reflected in the robot’s design, and directly translates into its efficiency and work safety. It’s to be expected that in the near future these robots will take over most of the transport tasks in warehouses and production halls, which are currently the domain of forklifts and logistic trains.
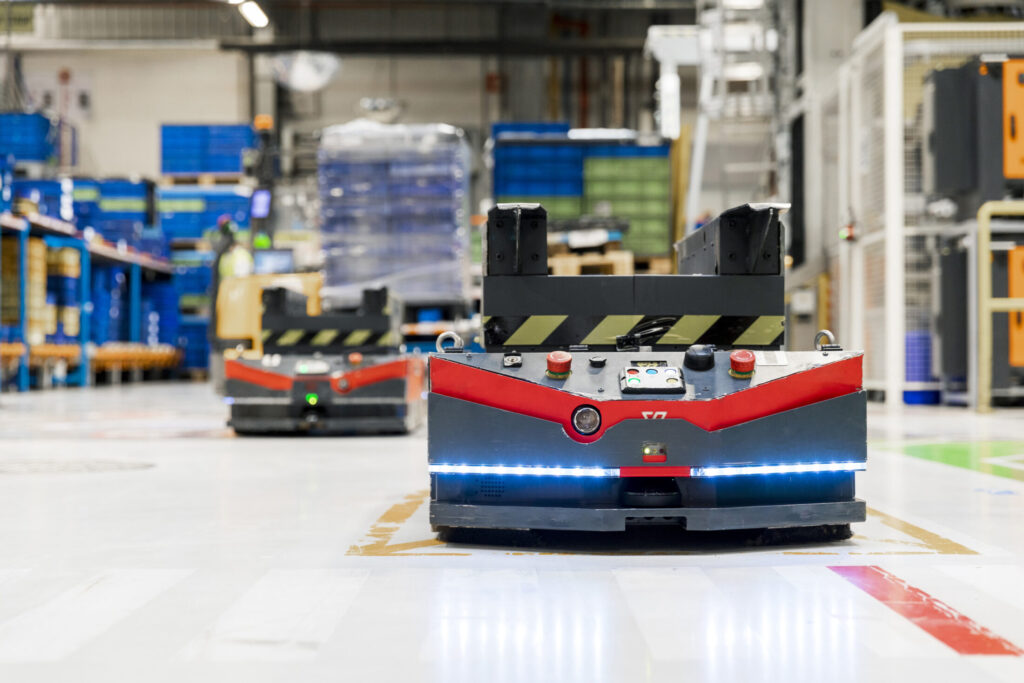
AGVs (Automated Guided Vehicles) haven been around since the mid-twentieth century. Over several decades, the trolley navigation system has evolved, taking the following forms:
- inductive navigation – the robot moves by detecting a magnetic field generated by a current flowing through a cable embedded in the floor – this solution is very troublesome in the case of already existing facilities because it means costly construction work, which would also be needed every time an AGV route needs to be changed;
- ferromagnetic or reflective navigation – ferromagnetic or reflective tape glued to the floor is used instead of an electric cable embedded in the floor – this solution is much cheaper and makes it easier to change transport routes;
- visual navigation – using machine vision and laser navigation, the robot scans the entire facility during its first pass and creates a virtual map that becomes a reference point for later navigation during transport tasks – this is the most flexible solution as it doesn’t require installing any markers in the working environment.
The development of robot control systems went hand in hand with improvements of navigation methods. Autonomous Mobile Robots (AMRs) are currently the most advanced version of autonomous transport trolleys. Their level of autonomy allows them to make independent decisions about choosing the optimal route between load collection and delivery points. Machines such as VERSABOT 500 and VERSABOT 1500 are able to distinguish between permanent obstacles (an abandoned pallet in an aisle) and temporary ones (a forklift, another robot, a person). This is the basis of their decision whether to choose another route or wait for the obstacle to be removed. These abilities mean that AMRs may well take over all horizontal transport in warehouses and production halls. All they need to operate is a hard and smooth floor.
Advantages of transport trolleys
The most important advantages of AMRs are related to their potential to optimise internal transport costs:
- maintenance-free operation – the lack of an operator means a drastic reduction of costs (one robot can work three shifts, which means it replaces three operators), guaranteed continuity of operations and predictable results (the robot always works in a fixed rhythm, doesn’t make mistakes, get tired or distracted);
- easy restructuring and scaling of the transport system – reprogramming of robot routes is very quick, which allows for flexible adaptation to current needs – you can start robotisation with a single AMR and expand your fleet gradually or exponentially;
- ability to work in every warehouse – you don’t have to build new warehouses “for AMRs”, and adaptations to existing facilities don’t require any deep interferences into their infrastructure;
- low failure rate – compared to forklifts and logistic trains, AMRs are machines with a simple, modular design – they have a low failure rate and repairs can be carried out quickly by simply replacing the entire damaged module;
- versatility of applications – AMRs come with tools and accessories that allow them to lift pallets and containers, tow warehouse dollies, transport frames on hangers, as well as cooperate with roller conveyors.
Is this a safe solution?
AMRs operate in a complex environment – they move along the same warehouse aisles as forklifts, logistic trains, and people. Therefore, the question of safety is completely natural. The answer is three safety levels. All AMR operations and activities include the fail-safe principle, which means the robot goes into a “safety mode” in case of any emergency. This also means that a critical system failure causes the drive to turn off and the robot to stop. This is an effective precaution against the fleet management system becoming “unleashed”, or continuing operations after damage to the laser scanner, for example.
Furthermore, each robot is equipped with active safety systems: motion sensors, cameras, bumpers, emergency stop pushbuttons, laser scanners, and machine vision systems. The machines are also equipped with passive safety systems, i.e., brightly coloured housing, body markings, and the ability to emit light and sound warning signals. These are needed not only by the people around the robot but by the robot itself – they’re mainly used to protect it against collisions with forklifts.
It can be said with absolute certainty that autonomous transport trolleys are the safest means of internal transport used in warehouses.
You might be interested in: How is it done at VersaBox? Comprehensive implementation of AMRs
Cobot, or new opportunities in your company
AMRs fully deserve to be called cobots, or collaborative robots. Thanks to their ability to work in a shared space with people, real operational autonomy, and low failure rate, they provide a number of company-wide benefits:
- mitigation of staffing shortages – AMRs are the solution to the problem of recruiting and retaining warehouse employees;
- minimisation of costly downtimes – low failure rates, easy repairs, and the ability to predict breakdowns makes traffic maintenance much easier, and losses due to downtimes are significantly reduced;
- increased efficiency – an autonomous warehouse robot can work three shifts a day, seven days a week, and the lack of absences allows you to create reliable work schedules and achieve efficiencies unattainable by people;
- improvement of work safety – if an AMR collides with another machine, in practice in means that the robot wasn’t able to escape the forklift – collisions with people are a purely theoretical possibility. They can only happen in case of a premeditated action (if an employee decides to jump onto a trolley, the machines cannot avoid it, but it will immediately stop).
Summary
VersaBox is an AGV and AMR company that offer a quick transition from traditional intralogistics to a warehouse transport system based on autonomous, intelligent machines. This change paves the way for real optimisation of warehouse operation costs – overall reduction of labour costs, significant increase in efficiency, improvement of safety and quality of work.