Are AMRs eco-friendly?
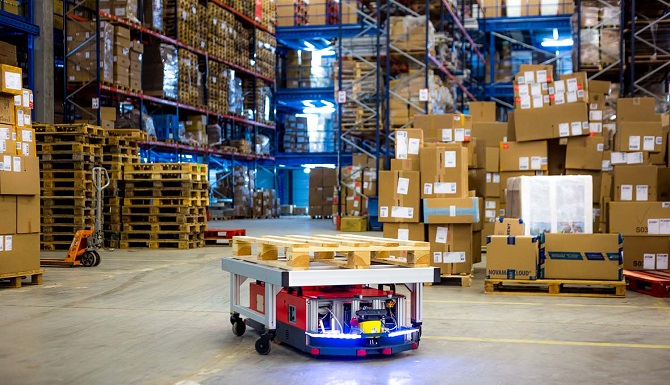
AMR-class autonomous robots perform similar tasks to those of intralogistic trains or electric forklifts. At the same time, their design is not as complicated – they’re smaller in size, and don’t require many of the mechanisms and elements normally associated with a human operator. This results in a much smaller impact on the natural environment and a reduction of the carbon footprint left behind. The most important advantage of AMRs, however, is the optimisation of energy of use that’s simply unattainable for other intralogistic vehicles.
The electric tide of history
The number of electric vehicles has been rapidly increasing over the last decade. Electric passenger cars becoming more commonplace, and work is well underway on electric lorries and trucks. They are seen as alternatives to diesel-powered trucks. The goal is to reduce emissions and the carbon footprint. Not many people are aware that this isn’t a new idea but that, in fact, it’s a return to an old one.
Before the internal combustion engine was perfected, electric cars were the reason for many breakthroughs in the automotive industry. The most commonly known example is finally beating the 100 km/h speed limitation. A Belgian driver called Camille Jenatzy achieved this on 29 April 1899. La Jamais Contente, an electric car resembling a rocket on wheels, which he constructed himself, reached a speed of 105.88 km/h. The car was powered using lead-acid batteries.
The development of electric drives for machines used in internal transport was less turbulent. The first vehicles with a lifting platform – prototypes of current transport trolleys and forklifts – were made in the 19th century. Vehicles that resemble machines used today have been around for about 100 years. When it comes to cars, the internal combustion engine side-lined electric engines for the last 100 years. However, both types of engines were developed in intralogistics. What’s more, electric drives have completely dominated transport in confined spaces. For obvious reasons, they were also a necessity for AMRs.
What’s the carbon footprint of an AMR?
AMRs are only ever equipped with an electric drive. Although it’s widely considered to be eco-friendly, it also somewhat controversial. Critics point to the significant carbon footprint of fully electric machines. The issue is the total CO2 emissions, i.e., the sum of emissions, starting from the manufacturing of the vehicle and then during its use. It’s true that electric engines don’t produce exhaust fumes, but traction batteries are a problem.
The manufacture of modern lithium-ion batteries – maintenance-free, durable, quick to charge, smaller and lighter than their lead-acid counterparts – is especially detrimental to the natural environment. They’re eco-friendly to use, but their manufacture requires the use of lithium and cobalt. These two elements can be found in very few places around the world, which means significant destruction of the environment during mining, and increased CO2 emissions during transport of the raw materials from the mining to the manufacturing sites. The difficult and expensive disposal of used batteries is another issue. This doesn’t change the fact that this type of battery is being used more often and will become even more commonplace in the future. This is why optimising energy consumption is a key issue that determines how effective carbon footprint reduction actually is. As a manufacturer of high-quality autonomous mobile robots, we care about the energy efficiency of every robot we design and manufacture.
AMRs are masters at optimising energy consumption
To illustrate why an AMR makes optimal use of its batteries and energy, it’s best to do so in comparison to a forklift. The first difference is obvious – size and weight. An AMR is lightweight and, as a result, uses up much less energy on driving without a load than a forklift. The second, and even more important difference, is the limitation of activities that don’t lead to any work being done. In fact, it’s not a limitation or a restriction, but the exclusion of any unnecessary activities and energy expenditures on unproductive tasks. An AMR only does things that will result in the intended effect. The robot doesn’t slow down or speed up unless there’s a need for it. It maintains an optimal speed and always selects an optimal route. It doesn’t go down the wrong aisle in a warehouse. It doesn’t make mistakes when assessing distances, which naturally limits the number of unnecessary manoeuvres when driving. A robot is fully predictable. It doesn’t have any social needs, so it won’t stop to have a chat or think through a problem.
It’s not an exaggeration to say that among all machines currently used in intralogistics, AMRs are the most effective at converting energy into work. As a result, they are currently the most environmentally friendly machines used in internal transport.