AGV robot vs Belt Conveyor in warehouses, sporting plants, factories
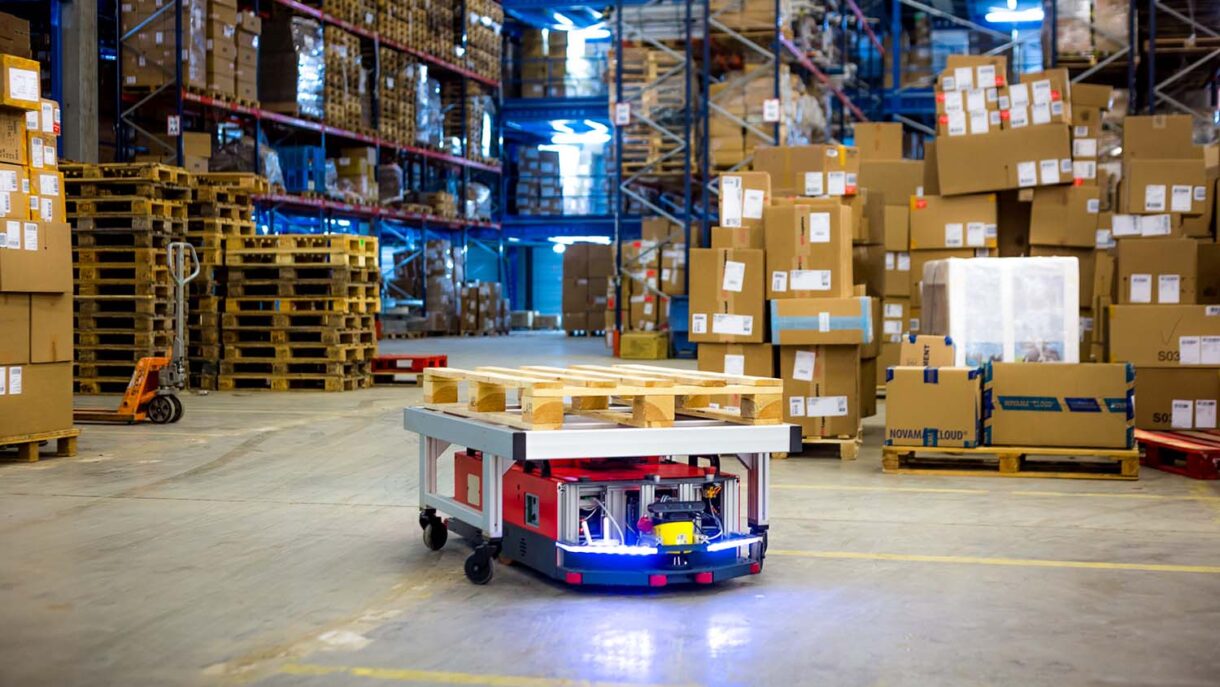
Automated Guided Vehicle (AGV) robots are often combined with conveyor belts and monorail systems. In some cases, they can be treated as complementary solutions. The choice between the two means of transport is dependent on whether speed or flexibility of transport management is a top priority.
When considering choosing a specific solution, you should be aware of the advantages and limitations of the three intralogistics systems mentioned above.
AGV robots: incomparable flexibility
The biggest advantage of AGV robots, especially Autonomous Mobile Robots (AMRs) such as VERSABOT 500 and VERSABOT 1000, is their multifaceted flexibility. It primarily concerns their quick and easy adjustment to existing working conditions. The implementation of AMRs is possible without the need for extensive changes in the architecture, equipment, or amenities of a given facility. Thanks to its ability to map the surroundings, the machine can navigate without the need for markers or landmarks. The only interference is the installation of a charging station, as well as the preparation of load collection and delivery points.
The flexibility of AMRs also applies to route changes and reconfigurations to perform new tasks. The change in collection and delivery points of goods takes place very quickly, and the costs of robot changeover are minimal. Thanks to this, logistics can stay flexible in the face of ever-changing manufacturing conditions.
In the event of robot breakdown, the logistics process does not stop – tasks assigned to the malfunctioning machine are given to another one, which can be done ‘on the fly’. All repair and maintenance services of an AMR fleet are possible without affecting the overall execution of logistics processes. Robot traffic can therefore be sustained very efficiently – processes are completed in a continuous cycle, practically without downtime.
Ensuring work safety is also a tremendously important feature of AMR implementation. Autonomous robots can work with people, but also with other modes of transport, such as forklifts or industrial tractors. Their design does not necessitate ‘human exclusion zones’ in warehouses and factory halls.
Belt conveyors and monorail systems: unbeatable efficiency
Belt conveyors, much like monorail systems, cannot be called a flexible solution. Assembling a conveyor system is a large, expensive, and time-consuming investment. It requires a precise design, setting up transfer stations, and testing of the entire system. However, high implementation costs are compensated for by the speed of operation. Intralogistics based on belt conveyors and monorail systems are characterised by very high efficiency.
A definite weak point of conveyors and monorail lines is that a malfunction of just one element halts the entire line. Repair and maintenance service people have to be extremely efficient in their work, in order to maintain the continuity of logistics processes. Even the smallest changes require huge financial expenses, primarily due to very costly downtimes and stoppages in transport and, consequently, in production.
One of the most important aspects of conveyor system operation is the problem of ensuring safety. Fully automated belt conveyors require physical access control, as well as monitoring the operation of the entire system in case of disturbances and potential threats to the people working in the vicinity.
AMR or a belt conveyor?
If the main goal is to ensure speed and efficiency of transport on fixed routes, the belt conveyors and monorail systems are decidedly a better solution. An additional argument in their favour is the high probability that once assembled, the conveyor system will not require any modifications or reconfigurations for long enough that a depreciation of the investment will be possible.
AMRs are a perfect fit wherever belt conveyors cannot be assembled due to technical or financial reasons, or if they are unjustified due to the need for frequent modifications of logistics processes. AMRs are slower than belt conveyors but ensure regular and reliable deliveries, for example, small parts between work centres or between warehouses and production facilities.
Summary
All the properties of intralogistics systems based on AMRs result in a relatively fast return on investment. The high adaptability of AMRs to the current needs of a production facility is an important aspect of building a competitive advantage. Low costs of retooling and changeover allow easy line assembly and cost-effective production of even small batches of particular products. This is incredibly important because, according to current forecasts, it is this ability to react quickly to changes in demand, and to adapt production to changes in customer expectations, will be an essential aspect in staying on the market in the face of a global and increasingly automated industrial manufacturing.