Automation in manufacturing: What you need to know?
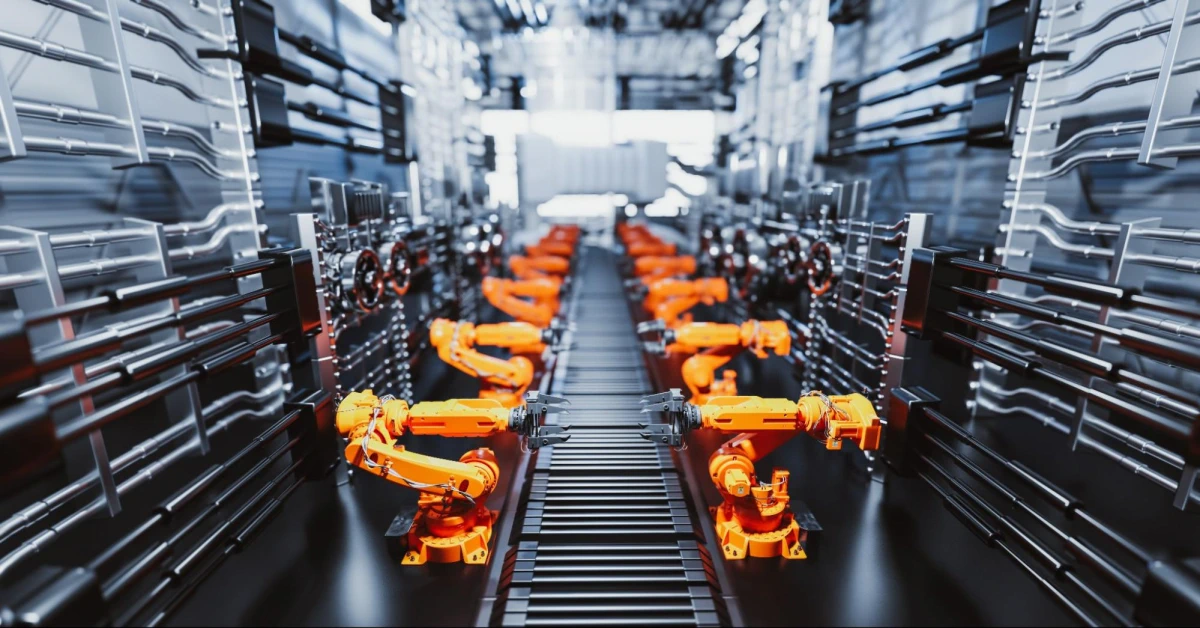
Recent years have brought us significant advancements in automation technologies, especially those with industrial applications. One of the most impacted sectors is by far the manufacturing industry. Today’s manufacturing automation tools can revolutionize a company and up its competitive capabilities. Let us take a closer look at automation in manufacturing and the benefits it can bring.
What is manufacturing automation?
This term can be summed up as the use of various technologies that allow the automation of production processes. This includes both software and equipment used in manufacturing.
Contrary to the first impression, industrial automation isn’t a novelty concept – first attempts, although simple, at automating manufacturing processes were made throughout almost all history. Even industrial robots aren’t as modern as you might think – the first diver-less electrical trolley was built in the 1950s by George Devol.
Types of automated manufacturing
Each manufacturing process, even under the same production line, is ever so slightly different. This means that we need various types of automating processes to cover all the different aspects of production. With this in mind, manufacturing automation can be divided into 3 main type groups:
Fixed automation
Also known as hard automation. Fixed automation can be summed up as a system in which manufacturing automation is used within individual machines or for a single product. Hard automation is generally used in large-volume production.
Fixed automation combines many production operations and sequences, which makes it a gargantuan task to switch production styles when the machine is set in place. Thus, launching a new product production requires high initial investment.
Some of the most common uses of hard automation include: assembly lines, chemical manufacturing processes, and conveyor systems.
Programmable automation
This type of automated manufacturing is based on a production system. This software is used for governing the whole manufacturing process, by serving as a set of rules by which the production line operates.
Contrary to the aforementioned type, programmable automation has some capacity to change – it can use varying sequences and be configured for different products. Moreover, you don’t have to get new machines when introducing other products – all you have to do is switch to a new program. Programmable automation works best as a batch production tool.
The most common applications of programmable automation include: NC (numerically controlled) machine tools, logic controllers, industrial robots (such as AGVs – Automated Guided Vehicles).
Flexible automation
Flexible automation might be considered as a successor to programmable automation – as its name suggests, it gives more freedom in configuring control systems. Besides each machine having its own controlling system (be it simple software or an HMI – Human Machine Interface), flexible automation has a central hub system, which controls all the material-handling and production systems.
This not only allows for fast adjustments to the product, but also enables running simultaneous production processes of different products. This works great for both on-demand production and batch production.
Flexible automation is used most prominently in: robotics (e.g. AMRs – Autonomous Mobile Robots), fully automated assembly lines, material handling systems.
Why should you incorporate manufacturing automation?
Using manufacturing automation in your production lines will bring you various benefits. Here are some of the most universal ones:
- Increased productivity – thanks to process automation, all the repetitive tasks will always be performed with the same effectiveness. Automated processes in manufacturing can therefore far exceed human capabilities in productivity. Moreover, a fully automated manufacturing business can run 24/7, which boosts productivity even more. Plus, technologies such as machine learning, AI, and Internet of Things (IoT) will help you optimize your supply chain further.
- Lower operating costs – despite the high initial cost of automation tools, implementing them can bring you significant added value – the difference is visible in the labour costs alone. Depending on the type of machine and nature of the task, a single robot can do the work of three or even five people. You can save even more with fully automated devices and production lines – there won’t be any need for lighting in the production hall, as robots can work in the dark. Considering the rising electricity prices, switching off the lights can save you thousands of dollars each month.
- Better product quality – advanced machines available today can be far more precise than human workers – automated systems perform manufacturing tasks with great accuracy, no matter the time of day. This leads to far more uniform results and significantly lower defect rate.
- Higher workplace safety – automation solutions allow you to remove human personnel from hazardous work conditions and dangerous environments. Moreover, there’s a group of robots (so-called cobots from collaborative robots) that can safely perform tasks in the same workspace as humans. Such machines are equipped with a system of sensors that detect movement in their proximity, so there’s no risk of the robot arm hitting a passer-by or a human working next to it.
Automation in manufacturing—summary
Manufacturing business processes can greatly benefit from automation – the technological advances available to manufacturing plants are a part of the next industrial revolution. Even a partially automated system can bring a significant boost to the entire business. Moreover, automated equipment performance is more consistent and can work to its fullest potential without human intervention. Digital transformation can therefore help your company achieve new heights and be more competitive on the market.