Automotive industry personalisation using AMRs
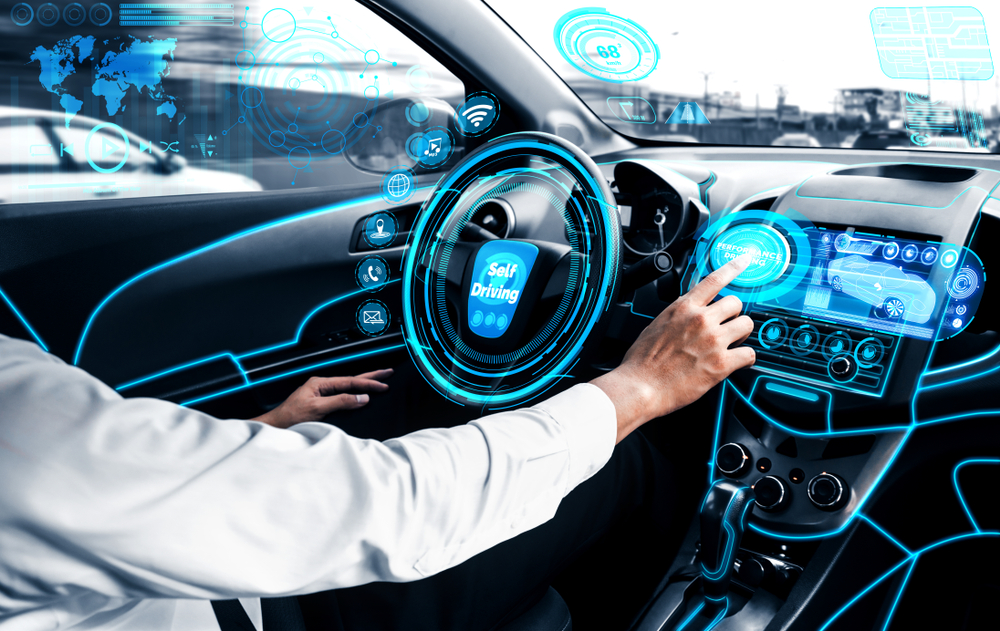
Configurators are part of every car manufacturer’s website. Even though they contain dozens of options, choosing your favourites can hardly be described as personalisation. In fact, we are only able to choose one of the ready-made options prepared by the manufacturer. True personalisation would exist if it were possible, for example, to submit a graphic design to be reproduced on the car bonnet. But such an option does not exist. Personalisation is possible but applies to luxury brands and is available only to very wealthy customers. For now. But things may change, and soon.
The COVID-19 pandemic has affected the automotive industry the same way violently slamming the brakes at speeds over 100 km/h does – no one knows what is going to happen next. Reports have just emerged that 100,000 people in the German automotive industry will lose their jobs. That is a huge upheaval. This crisis may last several years. However, even the pandemic cannot change the fact that the automotive industry is moving towards personalisation. Even today, car personalisation is partially possible thanks to the use of autonomous mobile robots. This trend is growing due to the dynamic progress of automation and robotisation of manufacturing.
From Ford Model T…
Over a century ago, Henry Ford launched the first assembly line in history. His goal was to reduce the price of the car as much as possible. He simplified the design, so that the car could be assembled on a moving production line. As a result, production pace increased greatly, which allowed him to set the unit price as a previously unattainable level.
The essence of Ford’s genius marketing can be summarised with his famous quote: “Any customer can have a car painted any colour that he wants, so long as it is black.” All Ford Model T’s were black. With time, cars in other colours appeared, but a non-black option came with additional high costs. This production model, where the customer chooses options that were pre-selected by the manufacturer, persisted for the next hundred years. Personalisation was simply not profitable.
Individualised cars with unique accessories and equipment, manufactured in limited series, cost a fortune to this day. Robert Lewandowski’s latest car is a perfect example – a Porsche 911 Speedster, with only 1,948 copies made, about PLN 1.3 million each. In comparison, hundreds of thousands mass-produced family cars are sold every year. Only thanks to mass production and standardisation can you offer a price that is achievable to an average Joe. Can this be changed, and can customisation be combined with affordability?
… to Industry 4.0
According to analysts, Industry 4.0 will bring about a change in the production model established by Ford. After over a century we will be back at the starting point – the car will be once again built as an individualised order. And not even as a limited series, but a single copy. Instead of using cumbersome configurators, we will be able to design our car from scratch. Moreover, this will not be an option only for the chosen ones, but the basis of manufacturing itself. Those who can afford it will hire professional designers. As a result, mass production will be a thing of the past – the product will be created after the order is received. Instead of looking for customers to sell ready-made and configured cars to, car dealers will try to tempt us with the promise of creative possibilities and their price. All of this will be possible thanks to the precise, efficient, and almost free work of robots.
AMRs allow product personalisation
Ford invented the assembly line. The linear nature of manufacturing processes means they do not tolerate modifications well. Even a simple change of car body colour, when done during manufacture, turns out to be a serious issue. The problem can be solved if you replace the assembly line with manufacturing cells. The car being made will move between these cells according to the specification order. The physical movement of the car between the manufacturing cells recreates the structure of a configuration tree. The time that elapses from the moment configuration is finished to when the production starts is an incredibly important factor. Needless to say, the goal is to shorten this time interval as much as possible. The scale of possibilities on offer thanks to robotisation can be seen in BMW factories. Currently, the customer can change the customisation of their car up to six days before the start of production.
The question of how to ensure flexible deliveries to manufacturing cells, with frequent component changes, still remains. The possibility of putting together such a “variable” assembly line based on belt conveyors is practically impossible. And yet the essence of customisation is the ability to react and quickly adapt to incoming orders. The problem can be easily solved by AMRs such as VERSABOT 500 and VERSABOT 1000.
By using AMRs instead of conveyors, logistic trains, or forklifts, you can achieve full flexibility of delivery of components to manufacturing cells. Changing the flow of the product being made will not require the physical repositioning of machines and conveyors. All that is needed are corrections in the robot fleet management system.
Additional benefits of using AMRs
Getting rid of human labour allows you to exclude the element of randomness. Robots maintain delivery time schedules without any delays, which means the entire manufacturing process becomes fully and easily controllable. In addition, robot labour is cheap and can go on for as long as necessary.
It is worth emphasising that the implementation of AMRs does not require any investments in infrastructure. All you need are charging and parking stations, the purchase of appropriate trolleys, and adaptation of collection and delivery zones. The introduction of autonomous transport trolleys into the production hall organises the entire manufacturing process. The present of autonomous robots allows you to monitor and effectively optimise all manufacturing processes. All of this results in the creation of a rapid response system to changing market demands. The manufacturer can fulfil personalised orders. Efficiency and quality of products increase. In the end, they get a chance at gaining a real competitive advantage. The change is huge, but it is easily accessible – and it becomes noticeable even after implementing a small fleet of AMRs.