Data-driven intralogistics
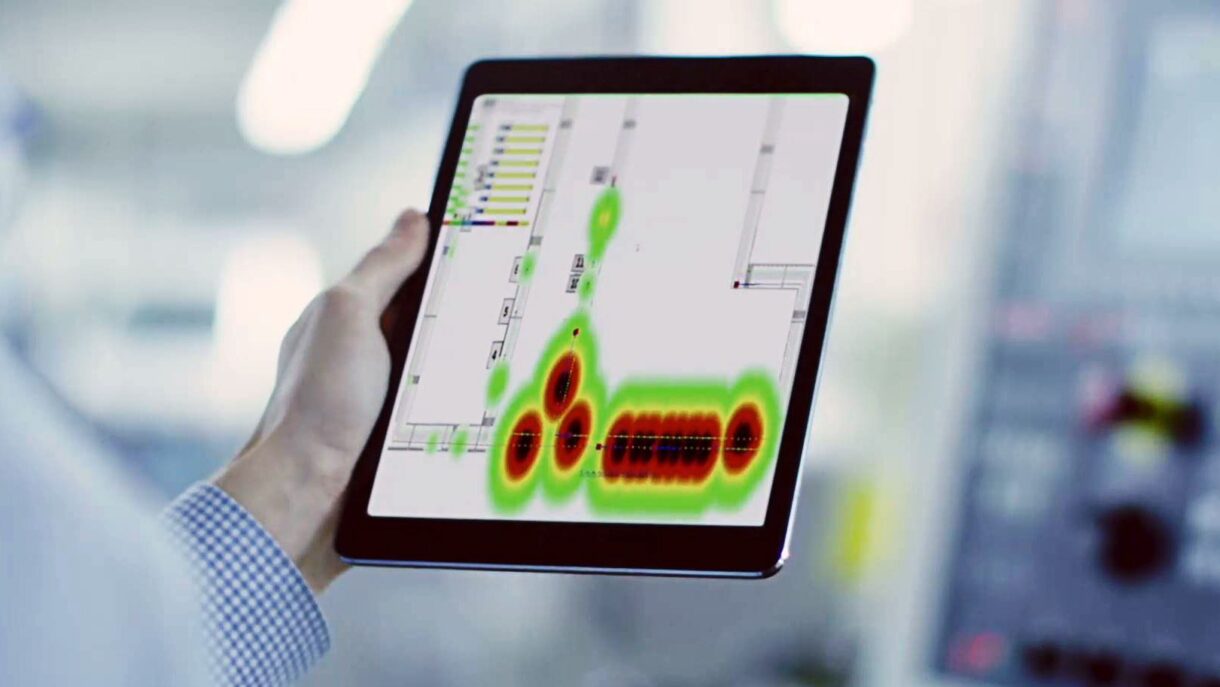
Data-driven business is one of the current, hot economy trends, especially in the industry. The idea is to base your business process management on data analysis. The aim is data monetisation, which in practice means optimising production costs (savings) and improving sales (profit maximisation). The Autonomy@Work transport system offered by VersaBox allows you to manage a fleet of Autonomous Mobile Robot (AMR) VERSABOTs using a data-driven approach. VersaBox Virtual Factory is an important component of the system – a tool for modelling intralogistics systems. The robots and the software comprise a comprehensive intralogistics solution with enormous optimisation potential.
Every industrial facility, every production line, and every machine produces huge amounts of data. Only a small portion of it is used in production management processes. The data-driven approach aims to collect and process data into something that will become a basis for making business decisions.
What can you learn from Autonomy@Work?
By using AMRs or running a simulation, we gain access to precise data on intralogistics processes and, as a result, manufacturing processes. You can monitor the implementation time of individual stages of the flow of materials and products on an ongoing basis:
- Minimum, maximum, and average delivery and collection times – knowing how much times elapses from placing an order to its completion, you can place orders for the delivery of necessary components in advance and order the collection of finished products.
- Production line cycle times – you receive information on real cycle time length and, as a result, can deliver the necessary components and pick up the finished goods on an ongoing basis without the need to create a stockpile. You can also study the efficiency of each production line by analysing the transport volume to/from the production line per shift/employee.
- Necessary buffer size – buffers are essential for maintaining efficient deliveries and production flows – determining an optimal buffer size significantly improves and shortens the implementation of the entire manufacturing chain.
The parameters described above are difficult to measure and standardise in traditional intralogistics systems. By using AMRs, not only do you gain quick access to data, but also full process predictability. Autonomous machines guarantee high task repeatability, which allows to eliminate time discrepancies. A given process is almost always executed in an identical length of time. This gives you real control over supply chains. The use of data allows you to optimise the entire internal transport system in a factory or a warehouse.
Virtual models replace spreadsheets
Spreadsheets are still the most commonly used tool for intralogistics management and internal transport design. The traditional model of intralogistics system design is based on knowledge and experience, as well as the intuition of people who create transport systems. The emotional aspect is also important here, for example pushing your own ideas and solutions when you are convinced they are correct. The decision process is based on a subjective, and not always rational, assessment of the situation. The result is a high risk of errors and, as a consequence, misguided business decisions, e.g. related to the purchase of machines or means of internal transport. A spreadsheet cannot help you predict or solve problems created by autonomous robots interacting with each other, with other means of transport, or with people. For example, it is very difficult to estimate where robot traffic jams might occur and how big they will be. And it is entirely impossible to analyse the impact of robot congestion on traffic in other parts of the facility.
The data-driven intralogistics approach aims to base the decision-making process on data, i.e. objective information about the real conditions in the production hall. The collected data is used to create a virtual model of the plant, including the machines and the people in it. It is a perfect environment for testing all planned changes before they are implemented in the real world.
The ultimate goal of making a model like that is to create a so-called virtual twin (a digital twin), i.e. to recreate the production facility in the virtual world. The model gets constantly perfected thanks to the constant input of process data. At some point it becomes an almost perfect mirror of all the processes taking place in the real world. This kind of environment is ideal for conducting all kinds of tests. You do not have to wait long to get results. Time ceases to be an obstacle in the virtual world because processes can be accelerated at will. In a matter of hours, the model provides data that would have taken months to obtain in the real world. The more data entered into the model, the more reliable the results. In practice, this means that the longer the virtual twin exists, the more valuable the information it can provide about its real-world mirror.
To convert traditional intralogistics management to a data-driven approach, you need Autonomous Mobile Robots (AMRs), and an appropriate system for process modelling and fleet management.
VersaBox Virtual Factory
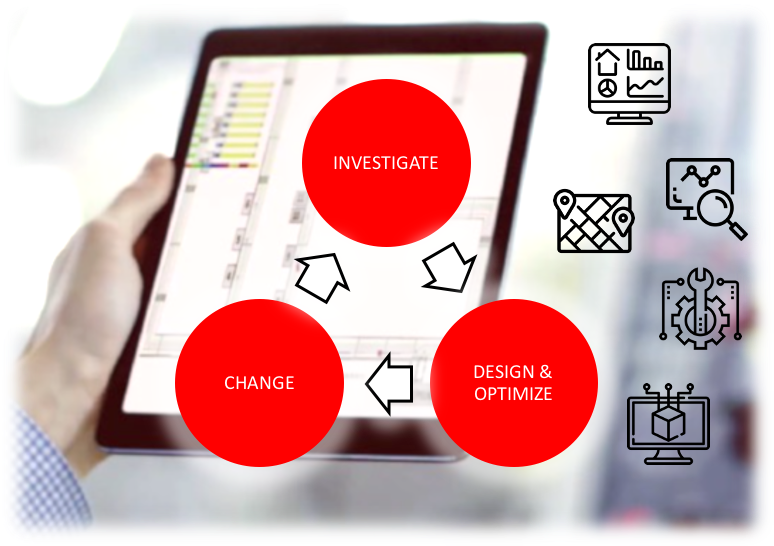
VersaBox offers a comprehensive intralogistics solution, which comprises of VERSABOT AMRs and the Autonomy@Work platform. The system can be applied to all stages of the organisation and management of internal transport:
- Pre-implementation analysis – VVF allows you to model and test the internal transport system before any tasks are even carried out in the real world. As a result reduce the investment risk, and reduce the cost and the implementation time.
- Monitoring and optimisation during operation – the platform created by VersaBox enables real-time monitoring of the AMR fleet and immediate implementation of corrections.
- Modification testing before implementation – planned modifications and expansions of the internal transport system can be tested on the virtual model, which avoids costly errors and unnecessary investments.
The system’s capabilities can be expanded by introducing electronic tags. These would allow to include data on the movement of all objects – AMRs, forklifts, logistic trains, people – into the virtual model of a production facility or a warehouse. This means that you would not have to use an estimated average speed of these objects for your calculations but could use actual data to make them more accurate. The result? Accuracy of process modelling that is simply unattainable in other ways. The self-learning algorithm will be able to analyse thousands of real situations. Based on them, it will be able to model the results of every implemented change. It will suggest the best optimisation solutions.
The first practical uses of the VVF system proved that modelling changes and their optimisation on a virtual model results in up to 30% reduction in implementation costs.
A virtual model of a production facility or a warehouse is installed the cloud (cloud computing). The customer can provide data and request appropriate tests or conduct the entire process on their own. Everything depends on the range of serviced purchased.
Real predictive maintenance
VersaBox Virtual Factory allows you to model the operation of AMRs and other elements of the intralogistics system over long periods of time. This means that it becomes possible, for example, to calculate the exact hours of operation a machine will work in a given time period. In turn, real-time monitoring will allow to detect any discrepancies between the model and the actual operation. There is also nothing to prevent robots from providing data on their technical condition themselves. Data from temperature or vibration sensors could be processed into reports for maintenance services.
The aforementioned data make an excellent basis for creating precise robot maintenance plans. These would be based on the actual condition of the machines and not on a predetermined schedule, as is the case with typical preventative maintenance. By conducting real-time monitoring, you can take preventative measures well in advance and avoid failures from happening. The same data can be used to accurately budget maintenance expenses. As a result, this new way of intralogistics management also allows you to switch maintenance to a data-driven approach.