Managing Autonomous Processes & Systems in Manufacturing
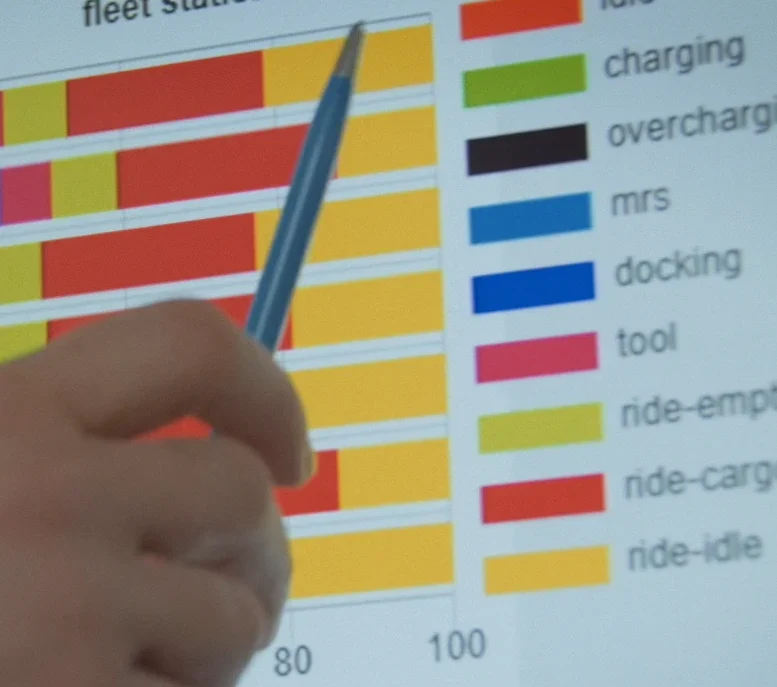
Autonomous systems in production and logistics
New areas of production automation
The industry today is short of manpower, and trends such as “re-shoring” (the return of production processes and industrial plants to developed countries) are making this phenomenon even more acute. Therefore, the automation of production processes is becoming a necessity also in areas where it has been neglected so far – e.g. in unloading and loading operations in warehouses, or internal transport in automated manufacturing. Automating processes in these areas is a sure way to cost savings.
Autonomous processes and systems
The factories can take advantage of smart machines that are able to independently plan the execution of the goals set for them. A perfect example are autonomous mobile robots (AMR – Autonomous Mobile Robots) and related autonomous internal transport systems (intralogistics). These machines can seriously speed up practically any manufacturing process and are one of the basic components of industrial automation. Implementing even a few of them can significantly lower manufacturing costs.
Production automation in its new version changes the way processes are carried out. The standard use of machines in manufacturing automation is also evolving – from the implementation of detailed and repeatable procedures to flexible execution of goal related missions. New robotics solutions allow flexible automation of manufacturing processes, improving the whole production system and lowering labor costs in many cases.
Industrial robots and people
Autonomous systems are one of the key factors influencing the roles performed by people in production plants. They replace humans in operational and simple management tasks. In the case of autonomous transport systems, these roles are taken over by mobile robots and fleet management systems supervising them. These systems, thanks to integration with production management and warehouse management systems, enable further optimization of production and freely programmable automation. In most cases, human labor on a production line can be fully replaced by programmable logic controllers. Fixed automation is especially beneficial for batch production and manufacturing tasks which could endanger human workers.
On the other hand, production automation allows managers to focus on meeting business needs efficiently and maintaining flexibility of operations. This is important because flexible operations and a reliable control system provide resilience towards changes in demand, and disruptions in supply chains. New technologies introduce new tools that are designed to provide new, better data, but as a rule, decisions are still made by humans.
Automation and robotization of processes also mean that there are new tasks where human participation is needed. The process of automating production lines and warehouses requires constant care to ensure that all components of autonomous systems work properly, cooperate with each other, and keep up with the development of needs.
The model of work efficiency for these roles is changing. Now human involvement embraces monitoring and analyzing data, planning or optimizing system configuration. Work efficiency results from knowledge and translates into efficient operation of production processes and effective response to unexpected events. Efficient performance of these roles requires access to modern business analytics tools, and proficiency in using them in a productive way.
Business analytics and robotization of production processes
Analytical systems in enterprises
Analytical systems in business have a long history and are one of the most mature areas of technology application. They are the norm in the industry. The level of sophistication differs between industries, however, decision support systems have always been built with the aim of providing decision makers and managers with data recording tools and their processing into reports supporting operational, tactical and even strategic decision making.
Reporting of operational indicators
Basic analytical tools are usually the functionality of systems supporting operations. They allow you to know the essential KPIs of the process – efficiency, orders, production in progress, stock levels, quality measurements, labor productivity, etc.
In operations managed by people, the reporting of indicators is used by the manager to correct the actions of employees operating the devices in order to achieve daily goals and smooth-out the production process.
Autonomous systems can use data generated by machines (robots, automated warehouses, sensors, etc.) to optimize the work of the smart factory on an ongoing basis so that operational goals are met. Data on operational indicators are available also to people but their management attention lies elsewhere. The key question that needs to be answered is whether the configuration of autonomous systems is optimal for the tasks and resources.
Optimizing goals, resources and managing the configuration of an autonomous system becomes a key element of operational management. Modern systems more and more often perform this type of optimization automatically, and in addition much more efficiently and faster than humans.
Interactive data analysis
Operational reporting is no longer enough when issues that go beyond routine patterns appear in the process. This may happen with significant changes in the logic or parameters of the process. An expected production efficiency may require changes not only in the system configuration (e.g. increasing the number of robots in the transport system) but also in its environment (e.g. increasing logistic buffers or adding more automated devices). This requires the analysis of more data, in a broader context.
The next step in the development of analytics was therefore the recording of historical data to track trends, and history-based leading indicators to implement adjustments to operational plans. At this stage, there was also a need for interactive multidimensional data analysis (On-Line Analytical Processing – OLAP) and the practice of building decision support systems with their complex data architectures. OLAP tools are intended for specialized analysts. An example may be a lean management analyst, responsible for designing a new, “better“ process or intra-logistics system by designing and evaluating a model based on process data, their patterns and correlations. Most modern process control systems automatically save all the required data.
Forecasting, simulation and decision automation
Predicting the future is becoming somewhat easier with modern tools and also increasingly important for business analytics. Two types of analytical systems are used for this purpose. Predictive systems are often based on machine learning. Their more and more frequent application is failure prediction, which allows for more effective planning of service activities and ensuring continuity of operations.
Simulation systems are based on dynamic models of the evaluated phenomena. It is a fundamental tool for predicting various scenarios of the behavior of systems and processes depending on their parameters and configuration.
The area of interactive analytics is also beginning to be automated. Firstly, thanks to the development of data mining tools that can generate rules based on data correlation analysis, and secondly, thanks to the development of machine learning methods and tools. However, this level of automation of analytical systems is still rare in manufacturing and logistics.
Analytics in the AUTONOMY@WORK system
Operational reporting
AUTONOMY@WORK allows you to monitor parameters related to the performance of an autonomous transport system in real time, and also provides data exchange with popular analytical tools.
Simulation
One of the key components supporting process design in the AUTONOMY@WORK ™ system is the VIRTUAL FACTORY ™ simulator. It enables operations managers and intralogistics specialists to model, assess and optimize the configuration of AMR-based intralogistics processes in the virtual (digital) factory space before its implementation in the real space.
People, data and autonomous production and transport processes
The trend of combining advanced analytical, simulation and production systems with process automation is becoming more and more clear. This combination of factors paves the way for truly autonomous processes and even entire factories that are capable not only of efficient implementation of routine activities, but also flexibly adapting to the changing environmental conditions and the expectations of the people in charge.
Lean management has always been one of the important reasons for introducing analytical systems and information management in the process. Today, Lean Management specialists are often at the forefront of the change related to the digitization of processes in industry and logistics. However, it is hard not to ask the question whether in autonomous factories there is still room for this management philosophy, strongly based on decentralization of decisions and first-hand experience from the shop floor (gemba).
Time for Lean 4.0?
Waste remains waste even when the related activities are performed by robots. Therefore, for example, the analytics available in AUTONOMY@WORK allows you to first track the utilization of devices in activities of different value (e.g. empty runs and waiting vs. loaded runs) and diagnose the possibilities of improving efficiency using simulation.
In an autonomous factory, managers of any level can have access to data illustrating the functioning of processes at any level of detail. And for the analysis of undesirable phenomena defined in Lean Management as “muda” they can use an advanced system for analysis and simulation. Arguably, with the advent of autonomous operations, a new version – Lean Management 4.0 – will emerge to support digital transformation in manufacturing and logistics. The conclusion is simple – don’t shy away from beneficial digital technologies and be ready for the next great industrial revolution.