Customers about VERSABOTs
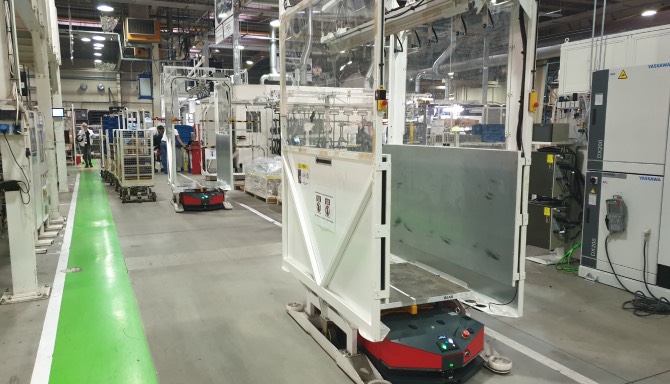
AGVs will bring simplification to all
The concept of production automation, intended to expedite manual labour, has recently gained momentum. How do we fare compared to others? Martin Slabý, a specialist in Manufacturing Engineering FAURECIA, presents the AGV project – Automated Guided Vehicles.
The AGV project was launched at our plant at the beginning of last year under the direction of our former colleagues, Daniel Pešla and Jakub Dostál. The aim is to automate the flow of products between welding machines, paint shops and assembly lines. The main benefit is the replacement of hard physical labour with machines, and an increase in efficiency.
AGV technology was selected from two main types of navigation solutions. The first type uses navigation based on a magnetic tape, the second one navigates using optical sensors which scan the environment. We chose the second solution for our factory due to a high intensity of traffic in the plant, which could rapidly damage the magnetic tape. The second reason was the ability to overcome dynamic obstacles. After selecting the right technology and the supplier, we began the testing phase, divided into 4 different areas (trials), which included a safety inspection carried out by an independent entity. After we successfully completed the testing phase, our supplier provided us with the first AGV device, which initially operated under the strict supervision of a project manager who recorded all the flaws and defects that had to be rectified by the manufacturer.
AGV technology is relatively new to us, and of course it has its whims that need to be understood to ensure its proper and effective functioning in our plant. Obtaining the desired functionality required an adjustment of many issues, layout optimisation, welding equipment and paint shop loop adaptation, logistics adjustments, removal of floor cracks, etc. Many modifications are still ahead of us. The currently operating AGV transports the welded UKL and VW120 Up MSP project frames to the paint shop. In the future, AGVs will also carry empty “hangers” from paint shops and assembly lines. The execution of these plans requires the implementation of another project – Fleet Management – which will be an indispensable component of their proper functioning. Until now, the project has experienced delays. The largest was caused by waiting for investment approval, which required the preparation of appropriate documentation, the calculation of demand and return on investment, the choice of financing method, the development of a project plan, etc. The first part of the investment, involving the implementation of 3 AGVs and the adjustment of the internal infrastructure, has already been approved and we can take further steps to successfully implement this project.
The first AGV has only operated 6 machines so far, and we have now been able to expand the scope of its work to 6 more. Within this expansion, we have also migrated all communication between production lines and AGVs to the internal WiFi network. The next step will be the implementation of a second AGV, which will transport the welded frames and slide rails of the VW379/326 project to the paint shop.
At the same time, software updates will also be implemented to eliminate errors and to speed up AGV docking. A prerequisite for a successful AGV implementation is the collaboration of all departments throughout the factory. For this reason, I would like to thank my colleagues from ME, logistics, traffic maintenance, IT, HSE, FES, control and UAP departments for their support in this project. I would also like to thank all machine operators for their patience and kindness during the AGV implementation and operation process.
HOW MANY WILL THERE BE?
For now, we plan to operate 6 AGVs for the transport of welded frames between the welding shop and the paint shop, and for the transport of empty hangers from the assembly line to the welding shop and from the paint shop to the assembly line.
CAN I BE HIT BY “IT”?
No, you won’t be hit. The AGV is equipped with mechanisms that recognise obstacles and, if necessary, stop the AGV.
HOW FAST DO THEY DRIVE?
Their speed is based on safety requirements. When going in a straight line, with no obstacles in its path, the AGV moves at a speed of 0.8 m/s. When avoiding obstacles, turning and parking, the speed is limited to 0.3 m/s.
(Martin Slabý, ME FAURECIA)