Top 3 processes to be automated using AMRs
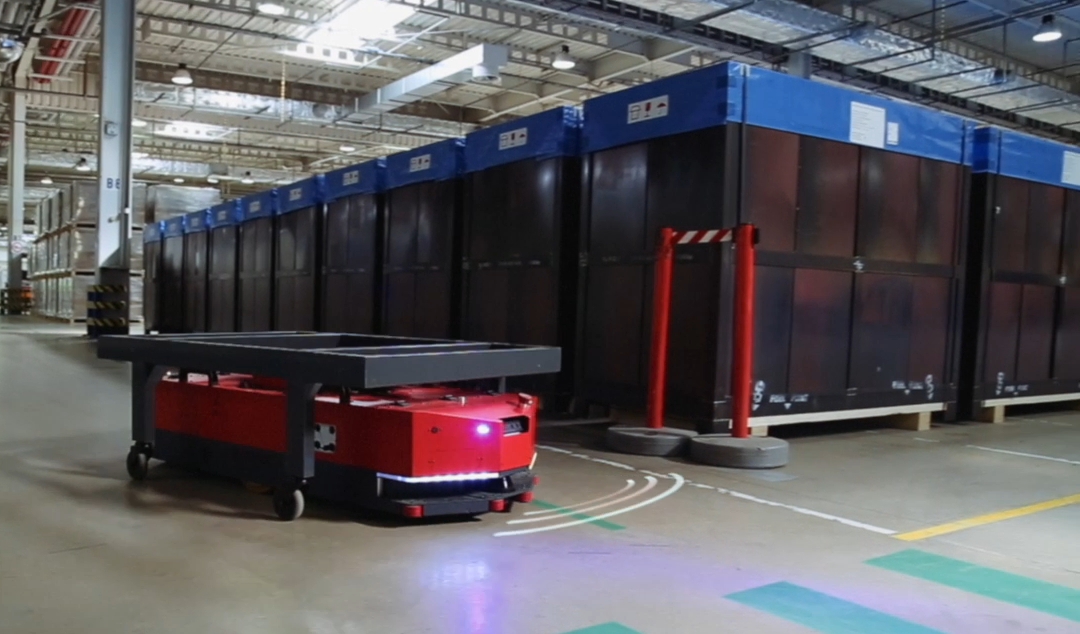
Autonomous Mobile Robots (AMRs) most commonly perform the same kind of task – collect a payload at point A, transport, and deliver it at point B. This simple sequence of events essential for many manufacturing and warehousing processes. In this article, we will discuss processes whose automation using AMRs has the greatest impact on improving the ROI.
“Our robots cannot go out into a snow-covered car park. It also does not make sense to use them to transport payloads over a distance of several metres. However, they are unrivalled whenever dealing with a smooth and level floor, and the need to ensure a steady flow of payloads of various weights and sizes,” says Mateusz Wiśniowski, CTO Robotics Expert at VersaBox, which produce AMRs.
3 areas of industrial intralogistics automation
Automated guided vehicles are slowly replacing forklifts and hand pallet trucks in manufacturing facilities. The reason is that forklifts pose a big risk to people and other handling equipment. Limited visibility, large weight of the forklift, or rushing to get tasks done quickly result in many collisions and serious accidents. Unlike forklifts, AMRs perform exceedingly well in environments where both people and other machines operate. Their safety systems make them fully collision-free (they do not instigate the collisions). Their small size allows AMRs to operate in tight and narrow spaces where it would be impossible to use other means of transport.
The most important intralogistics processes, which could be automated using AMRs, concern three areas:
- Transport of materials from the warehouse to the manufacturing hall. This is an area with the greatest optimisation potential. AMR-based deliveries are fully maintenance-free. As a result, they become smooth, predictable, reliable, and measurable. Depending on needs, the robot can deliver one type of material to manufacturing cells or offer a diverse assortment of materials and supply multiple cells during a single pass.
- Transport between manufacturing cells. The need to produce many variants of the same product makes modern industrial processes increasingly non-linear. The journey of the product being made between manufacturing cells depends on the finished product you want to achieve. The path of car with a petrol engine is different to that of a car with a diesel engine or a hybrid drive. Quite often new equipment or a new type of drive appears after a production series is launched, and a new manufacturing cell must be created quickly. Modifications can also be caused by the variability of market demand for specific models, equipment, or accessories.Fast and relatively cheap conversion of a production line is possible only if AMRs are responsible for the transport of the product being made and its components. In the case of conveyor belts, the same kind of conversion would be incomparably more time-consuming and expensive. Thanks to their small size, AMRs can reach far deeper into manufacturing cells. The same cannot be said for large and heavy forklifts. On the other hand, logistic trains are very hard to manoeuvre – they cannot reverse and are unable to turn on the spot. The only thing left is manual transport, which is burdened with many limitations. These are the result of labour legislation and difficulties in recruiting people.
- Transport between the manufacturing hall and the finished goods warehouse. The task is similar to transporting materials from the warehouse to the manufacturing hall. An AMR, or a group of AMRs, can perform transport tasks using a milk-run system – it can collect goods from multiple manufacturing cells and deliver them to the finished goods warehouse. It is possible to track the reference numbers and current location of each pallet being transported. It is up to the Warehouse Management System (WMS), however, to direct pallets to the proper warehouse, to the picking zone, or to be shipped.
3 types of internal transport most susceptible automation
Automated guided vehicles have less competition with each passing day when it comes to horizontal transport. They effortlessly take over the tasks of other material handling equipment. Here are three processes, which are ideal for automation with AMRs:
- transport of pallets taken from a feeder – VERSABOT robots are perfect for this task thanks to their small size. The robot’s width is smaller than the width of a standard roller feeder, which means the implementation of VERSABOTs does not require costly expansions of stations,
- transport on trolleys – the payload is not placed directly on the robot, but on a trolley for which the AMR is the driving unit. One robot can handle a large number of trolleys, which is a very economical solution in the case of a wide variety of payloads and frequent changes in the assortment of transported goods, but also in the case of small batch sizes – the robot can deliver a full trolley and collect an empty one, thus reducing the number of empty runs.
- transport of components suspended on frames – a special module for transporting hangers, which the robot collects automatically from standard suspended rails made from steel: this can be used to transport heave steel components, but the robots could also “get hired” in the clothing industry and transport clothes on the hangers.
Excellent ROI and low investment risk
In the case of AMRs, you do not have to immediately implement an entire fleet of robots. You can start with a single robot. Moreover, the implementation does not require any changes in the architecture of the facility. As a result, the investment risk is significantly lower when compared to other logistic solutions. The likelihood of disruptions in manufacturing processes is also lower. All this makes testing the capabilities of an AMR completely safe in the context of the company’s finances and maintaining production continuity.
The situation with ROI, i.e. the return on investment, is no less attractive. If a factory or a warehouse operates in a three-shift system, then one AMR replaces at least three employees. This includes the costs of leasing or purchasing a forklift, and expenses for its maintenance and repair. Under these conditions, the return on investment on an AMR-based transport system ranges from just 18 to 24 months.