Versabots automate manufacturing at the IKEA network Partner – Padma
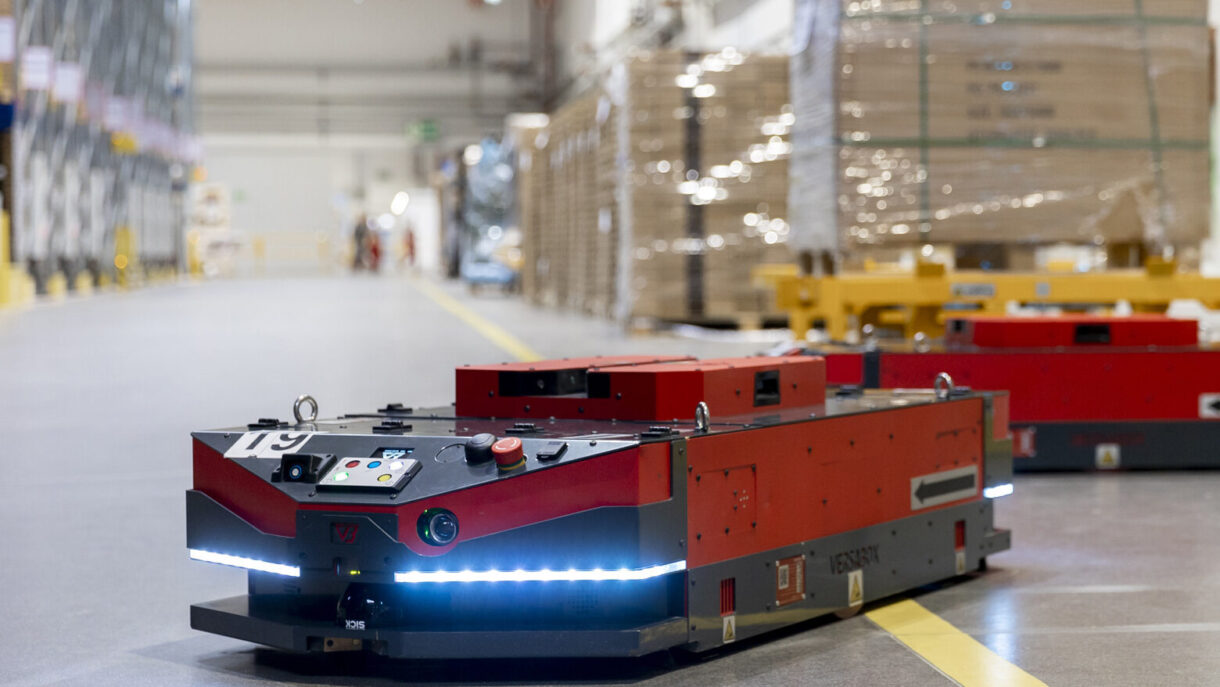
Entrusting internal transport at the Padma furniture factory in Suwałki to Versabot autonomous robots is a step towards the implementation of a futuristic vision of automation in a company for which innovation is one of its competitive edges on the global market.
The effects are already visible: increased productivity and manufacturing efficiency, decreased workload for the staff, greater reliability and transparency of intralogistics processes, and an increased level of safety – and all this with a return on investment of 25%.
Thanks to all this, Padma – a leader in the furniture and home decor industry, and a long-term subcontractor for IKEA – is able to develop faster and meet the requirements of its international partners a lot easier.
The customer: Padma is one of the largest furniture and home decor manufacturers in Poland and has been a partner in the global IKEA network since 2008. Innovation, development, and automation are key components of the organisational culture of the factory, which employs around 1500 people.
The most important goals of introducing VersaBox autonomous mobile robots were to increase the flexibility and the efficiency of the manufacturing process, while at the same providing an appealing return on investment.
“For me, Padma is an example of a tremendous success of a Polish company operating in the global supply chain. VersaBox, which has provided the technology to digitally transform the transport system in the factory, is becoming a part of this success and that makes us immensely proud. The experience gained will allow us to further improve our product. The implementation of VersaBots in Padma confirms that our solution works in a globally competitive environments that our client operates in.”
Jacek Królik, President of the Management Board, VersaBox
The challenge
Optimisation of internal transport between the components warehouse and the production line, including:
- resource management,
- order fulfilment,
- digital data collection,
- reduction of intralogistics costs.
“Due to an increase in production scale, we are constantly modernising our machine park. The implementation of robots is a kind of automation of manufacturing for us, thanks to which we can delegate our employees to other processes, enable them to further develop and gain qualifications.”
Monika Grochowska, Production Manager, Padma
The solution
- 2 autonomous mobile robots, Versabot VB500, equipped with several types of trolleys adapted to payload transportation,
- the Autonomy@Work intralogistics platform,
- VersaBox maintenance team and monitoring installed in the robots.
“Our system is not just the robot – it’s also the comprehensive Autonomy@Work platform, which is simple and intuitive to use. The platform lets the customer make changes and optimise the intralogistics process. The system consists of a Process Manager responsible for process management, the True Autonomy navigation system that can handle dynamic environments perfectly, and a Fleet Manager responsible for robot operation management.”
Mateusz Nowakowski, Robotic Expert, VersaBox
The process
The implementation of Versabots in Padma was a multi-stage process that required the involvement of both the customer and VersaBox specialists. The key elements included:
- adaptation of trolleys to varied payloads that need to be transported,
- adjustment of digital solutions to fit the customer’s existing IT systems,
- ensuring transport safety in a harsh factory environment.
“We designed the transport process at the beginning of our cooperation with the customer. We use our proprietary software for this purpose. The digital version of the factory layout is uploaded into our software, and we design the entire intralogistics process using digital twins of our robots, controlled by exactly the same algorithms used to operate real robots. We forecast how many robots will be needed, where to place the loading points, what the process is going to look like, and how efficient it will be using a given fleet, or its maximum efficiency.”
Szymon Kubicki, Sales Director for Poland, VersaBox
The effects
Autonomous internal transport operated by two VersaBox robots has been in operation at the Padma factory since September 2021. Since then, Versabots have:
- transported goods with a total weight of over 1,100 tonnes,
- covered a total distance of over 2 thousand kilometres.
“Six months after implementation we can confirm that the system fully meets our expectations.”
Marcin Augustajtys, Production Engineering Coordinator, Padma
“Despite many initial concerns related to our cooperation and the safety of working with robots, our employees are gradually warming up to them, and the company itself gets perceived as modern and innovative. That is why we are currently expanding the scope of Versabots’ operation and launching new service lines.”
Monika Grochowska, Production Manager, Padma
Why VersaBox?
According to the customer, the most important advantages of the AMR robot system offered by VersaBox are:
- quality,
- efficiency,
- flexibility,
- safety.
“The decision to go with VersaBox was determined by the durability and high quality of the proposed solutions, their modularity, flexible approach, perfect navigation capabilities, as well as the virtual simulation, which helped in estimating our aims.”
Marcin Augustajtys, Production Engineering Coordinator, Padma
“Our customers receive a unique combination of durable and proven hardware solutions with an advanced navigation and process management system.
We pay special attention to safety and quality of workmanship, starting from the design stage and through to the manufacturing stage, which is why our robots undergo very thorough tests. Providing comprehensive and efficient process and technical maintenance for our clients is part of our extensive customer service. We support our customers directly through the maintenance team and indirectly through the advanced monitoring system installed in our robots.”
Rafał Chojecki, Head of Production, VersaBox
“We chose the VersaBox solution because of its flexibility. In IT, the ease of integration with various solutions and systems is particularly important to us.”
Jan Giedrojć, Head of IT, Padma
“We were positively surprised by the safety measures, which included adjusting the robot’s speed depending on the amount of free space around it. When an employee appears the path of a robot there’s no need to consider the driver’s reaction time, as in the case of a traditional forklift – the system will safely stop all on its own.”
Patryk Walendzewicz, Health and Safety Specialist, Padma