Epidemiological safety and robotisation
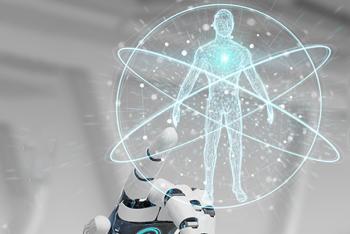
The COVID-19 pandemic has caused significant changes in industry and trade, which have sparked a new interest in automation and robotisation. This epidemiological threat has created two opposing trends. The first is fully in line with forecasts – concerned about the impending crisis, companies reduced their spending on the robotisation of manufacturing processes. The second trend was a surprise to many analysts – the warehousing industry is undergoing intense robotisation to cope with the sharp increase in turnover during lockdown.
“The pandemic became the push needed to make the decision to implement intralogistics robots for many of our customers in the food and warehousing industries. The Lubella factory, where we deployed our robots during lockdown, is the perfect example. Tons of people began to cook their own meals due to the closure of restaurants and cafes. The robots turned out to be indispensable in handling the rapid increase in demand for cereal products,” says Mateusz Wiśniowski, CTO Robotics Expert in VersaBox, an Autonomous Mobile Robot (AMR) manufacturing company.
Food sector not the only beneficiary of lockdown
The list of enterprises that broke sales records during the pandemic includes companies from the new technologies industry, pharmaceutical manufacturers (disinfectants, masks, visors), video game companies, and manufacturers of sports equipment for home use.
The construction industry and home furnishings manufacturers are also doing exceedingly well. Due to the fact that people were not able or were afraid to leave the house, the e-commerce industry and delivery companies also experienced record-breaking turnovers. The need to handle huge numbers of orders immediately translated into an incredibly dynamic growth of the warehousing industry.
Warehouses boom during pandemic
The recently published Savills Report demonstrates that the warehousing industry proved to be completely immune to the economic turmoil caused by the pandemic. It not only maintained its growth rate in the first two quarters, but also outperformed the 2019 financial indicators. Gross demand for warehouse and industrial space increased by almost a quarter in the first half of 2020.
Great economic conditions go hand in hand with increased risk – the detection of even a single COVID-19 case would mean closing the warehouse for two weeks of mandatory quarantine. This led to many companies extending time intervals between shifts to prevent contact between employees. If a COVID-19 case gets detected, only one shift goes into quarantine. The problem of disease transmission and infections can be solved with AMRs handing intralogistics processes.
AMRs solve staff shortages in times of pandemic
“Before the pandemic, AMRs were seen as a tempting alternative to forklift, pallet truck, and logistic train operators. The pandemic has made automated guided vehicles the only way for many manufacturing companies and warehouses to maintain a continuous workflow or handle the increased number of orders,” says Mateusz Wiśniowski.
From an epidemiological point of view, a robot is completely safe when compared to a human. If the machine is truly autonomous, as is the case with VERSABOT robots, it precludes the possibility of transmitting pathogenic microorganisms. The reason is simple – an AMR performs all tasks without any human contact. The robot carries out all operations and decisions related to the transport of a given payload from point A to point B entirely on its own, and without the need for human presence or help. It collects the payload, chooses a route, and transports the payload to the designated location within a warehouse or production facility. Then, it places the load at the delivery point, also on its own. The only time when machine and human cross paths and come into direct contact is during maintenance or repair.
This is obvious but worth emphasising: robots do not get sick. They can work literally non-stop, as they do not get tired and labour laws do not apply to them. If you use robots, you do not have to fear of absenteeism due to sickness, holidays, or random events. The problem of staff shortages, associated with a lack of people willing to take up specific jobs, disappears. The tedious process of searching for, recruiting, and training handling equipment operators can be replaced with a quick and reliable implementation of AMRs.
The possibility of repeated disinfection is also very important. Clean zones and so-called clean rooms, i.e. rooms with a very high cleanliness standard, are a necessary requirement in the food, pharmaceutical, and cosmetics industries. The movement of people between different cleanliness zones requires the use of specialised protective clothing and complex disinfection systems. Autonomous mobile robots solve this problem. AMRs can be disinfected quickly and cheaply using ultraviolet radiation, ozone, or chemical disinfectants. The procedure can be repeated any number of times, without the need to worry about harmful side effects.
Pandemic survival and investment into future
“Our customers from the automotive industry are currently very careful with their investments – they limit the scale of deployments or postpone projects until the new car sales market regains its momentum from before the pandemic. However, they are constantly investing into robotisation because, regardless of the situation on the market, car production requires progressive automation and autonomisation of processes,” says Mateusz Wiśniowski. “The forecasted development of the automotive industry will lead towards the production of more and more personalised cars, made in increasingly limited series. Achieving this kind of goal is impossible without autonomous robots.”
Many industries face similar challenges. Today, no one is able to determine precisely how quickly the economy will recover from the losses caused by the lockdown. However, it is an indisputable fact that robotisation is the only development path that provides the opportunity to build a strong market position. In the near future, it may become a requirement for survival in the realities of the global economy.