How an expensive robot reduces labour costs
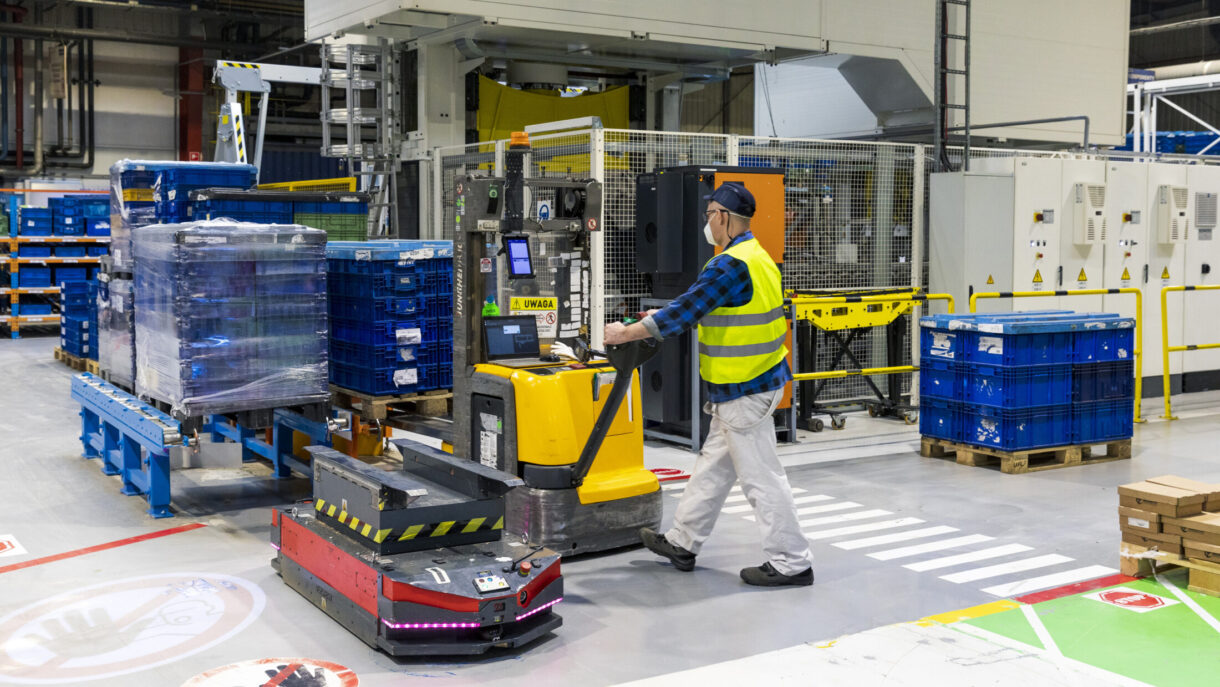
How an expensive robot reduces labour costs
Robots aren’t cheap. The purchase and implementation of an AGV-class robot means expenses that may seem disproportionately high in relation to the labour costs of an unskilled worker or even a forklift operator. However, if we tally up the overall labour costs, it’s easy to see that expensive robots (purchase and implementation) have very low labour costs. An investment in robotisation is depreciated within two years, and the first benefits are visible straight after implementation.
Contrary to ideas present in science fiction movies, robots won’t replace hairdressers, dentists, conductors or painters (even house painters) for years to come. Tasks that require interactions with the environment, the ability to negotiate decisions or an aesthetic sense are by no means beyond the reach of intelligent machines. However, the costs of their creation are disproportionate to the potential profits. The use of robots in the manufacturing industry and logistics, however, is an entirely different matter.
What do robots do better than humans?
The use of robots brings the greatest benefits whenever it’s necessary to perform repetitive, monotonous or highly physical tasks. Employees carrying out such tasks get understandably tired, and cannot maintain the pace and the precision required to complete those tasks. This results in an ever-increasing number of mistakes, which in practice mean loss of property, but also serious accidents that endanger human life and health. The remedies for these issues are steadily growing automation and robotisation, which are already a prerequisite for ensuring consistent and high-quality production in many manufacturing industries.
The following types of tasks benefit the most from the use of robots:
- tasks performed under adverse working conditions – in low and high temperatures, in highly polluted air or in the presence of toxic substances,
- repetitive tasks – any type of work “on the line” requiring many hours of performing the same task or sequences thereof,
- high precision tasks – for example installation of very small components,
- working in hard-to-reach places – the robot can operate at high altitudes, in narrow channels or low-ceiling rooms,
- high-strength work – robots can easily move heavy loads and repeat these tasks as many times as is required.
For the above tasks, robots are not only more efficient and more precise, but also provide almost 100% reproducibility of finished products or the quality of the work done. In the case of AGV (Autonomous Guided Vehicle) robots used for internal transport, it means that — apart from emergency situations — cargo will always arrive at the designated place at the designated time, parts will always be at the assembly station, and materials will always be at the production station.
Machines work for less
Robots offer a quality of work, which we don’t have to pay for, that’s unattainable for people. Labour costs of intelligent machines come down to charging and repair. Not only do robots not get a salary, but they also don’t need holidays or sick leave. They also don’t suffer from burnout and don’t require incentive systems. From the employer’s point of view, it’s also crucial that robots don’t change and abandon their jobs. These issues seem obvious but are often overlooked when purchase and implementation costs of robots are compared to human labour costs.
The advantages of using robots are best demonstrated by the behaviour of international corporations. Until recently, it was obvious that the best way to reduce labour costs is to move production to a country where worker protection laws are weak or non-existent, and unemployment forces people to take incredibly low paid jobs. Today, an alternative has been created: constructing a factory in a developing (read: poor) country or robotising production. And this is not an ostensible alternative, but increasingly the reality of the global economy.
How does a robot depreciate in warehouses and factories?
The biggest obstacles in robotisation are the costs of purchasing and implementing intelligent machines. The second hurdle is insufficient knowledge about the possibilities of robots and subsequent wariness regarding their implementation in manufacturing and logistics.
“We are aware of this and we regularly organise VersaBox Academy training dedicated to robotisation, Industry 4.0 and intelligent intralogistics,” says Mateusz Wiśniowski, VersaBox CTO. “We also offer free demonstrations of our AGV robots, especially the flagship VERSABOT 500 model. They allow for a personal assessment of the robots’ business potential.”
VersaBox’s experience so far clearly shows that investing in robotisation is cost-effective. The average depreciation period for VERSABOT 500 is between six months and two years. How quickly the robot starts to generate meaningful profits depends on the type of manufacturing done and the tasks performed. It’s worth noting that you don’t have to wait years to see the first results: the robot offers an immediate increase in quality of work, efficiency and safety.