AGV, AIV, AMR, SGV, LGV – what are these?
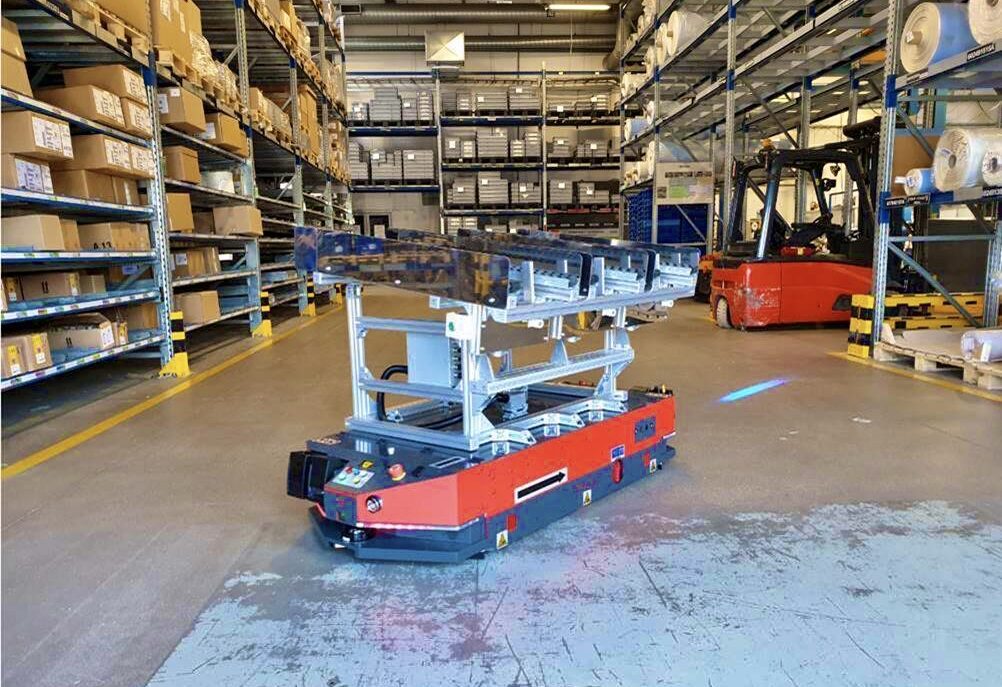
Automated Guided Vehicle (AGV) is the most common name for various types of automatic trolleys used for internal transport. It is often used alongside or even interchangeably with the name Automated Mobile Robot (AMR). There are also terms like Autonomous Intelligent Vehicle (AIV), Self-Guided Vehicle (SGV), and even Laser-Guided Vehicle (LGV). How to tell these machines apart? What design and functional differences are hidden in these terms and abbreviations?
An overabundance of names is often a result of a strong desire among manufacturers to distinguish their robots from the competition. However, regardless of the terms used, a rudimentary distinction can be made based on the level of autonomy of the machine.
Automated vs autonomous
The automation of internal transport is currently associated primarily with the concept of Industry 4.0, i.e. the fourth industrial revolution. However, it is worth remembering that the first AGV trolley was introduced as early as the mid-twentieth century. The machine was deployed at the U.S. Barrett Electronics facility in Northbrook, Illinois. This historic robot was a kind of tug, adapted to pull trolleys and trucks without their own engines. It had very limited autonomy – it moved thanks to inductive guidance, that is, along a live wire embedded into the plant floor.
The key to the development of AGV robots was a navigation system capable of working inside warehouses and production facilities. The replacement of live wires embedded in the floor with adhesive tapes stuck to the surface of it was another milestone. Guides like these, made from ferromagnetic or light reflective material, did not require as much interference into the architecture of the work environment as inductive guidance, which greatly contributed to the popularisation of AGV robots. Machine vision and laser-based navigation were the next big breakthroughs. This is where the name Laser-Guided Vehicle (LGV) comes from. Using this technology, the robot scans the surroundings and possible routes during its first journey and creates a digital map of the area. Once implemented, the map is a reference guide for the robot. It compares the current state of the environment with the digital counterpart, which enables it to distinguish between permanent obstacles (storage shelves, pillars, walls, etc.) and temporary obstructions (e.g. an abandoned loaded pallet, etc.). Thanks to the use of laser scanners, AGV robots could be ‘unleashed’ – physical guidance systems became superfluous.
AGV robots, if equipped with the appropriate software, can independently make decisions about the best route to take, but also assess whether a given obstacle is temporary (e.g. a forklift operated by a person) and passage will be possible shortly, or whether it is better to choose a new route to the collection and delivery point. If the AGV truly possesses such capabilities, then it fully deserves to be called an AMR. An example of Autonomous Mobile Robots, transport trolleys with actual autonomy, are the VERSABOT 500 and VERSABOT 1000.
Unit load vehicles, tugs and forklifts
Apart from a division based on intelligence and autonomy, AMRs also represent several different functional classes. As mentioned above, the first AGV trolley was a tug, representing the category of towing vehicles. These types of trolleys or trucks are designed to move loads on mobile platforms. An interesting class of AGV robots are the so-called fork vehicles, i.e. autonomous forklifts, that enable horizontal transport, but also collection and delivery of loads to the higher shelves of storage racks.
The aforementioned VERSABOT 500 and VERSABOT 1000 belong to the currently most popular class of AGVs in the industry – unit load vehicles. They are very easy to spot – low platforms equipped with a load collection mechanism. The items to be transported are either on a pallet or a specially adapted cart on wheels – the robot moves under the cart, attaches to it from below, and begins the delivery.
AMRs are the future
To sum up this analysis, it can be assumed that Automated Guided Vehicle (AGV) is the broadest category that encompasses all automated trolleys (mobile robots) used for internal transport in warehouses and production facilities. Autonomous Mobile Robots (AMRs), also called Autonomous Intelligent Vehicles (AIVs) or Self-Guided Vehicles (SGVs), are the most important subcategory of AGVs. Mobile robots that use inductive or reflective guidance systems are still present in warehouses and factories. However, at present the market is dominated by robots that navigate using digital maps of the premises.
The choice of a specific AMR model should be based on an analysis of implementation possibilities in a given work environment. When it comes to the design of the machines themselves, their navigation systems or lift capacity, there are very few differences between what the AMR manufacturers have to offer. The key issue is the efficient management of the robot fleet. The actual advantages of using AMRs depend on the system’s capabilities, including its optimisation potential.