Intralogistics 4.0. Glossary of terms – part II
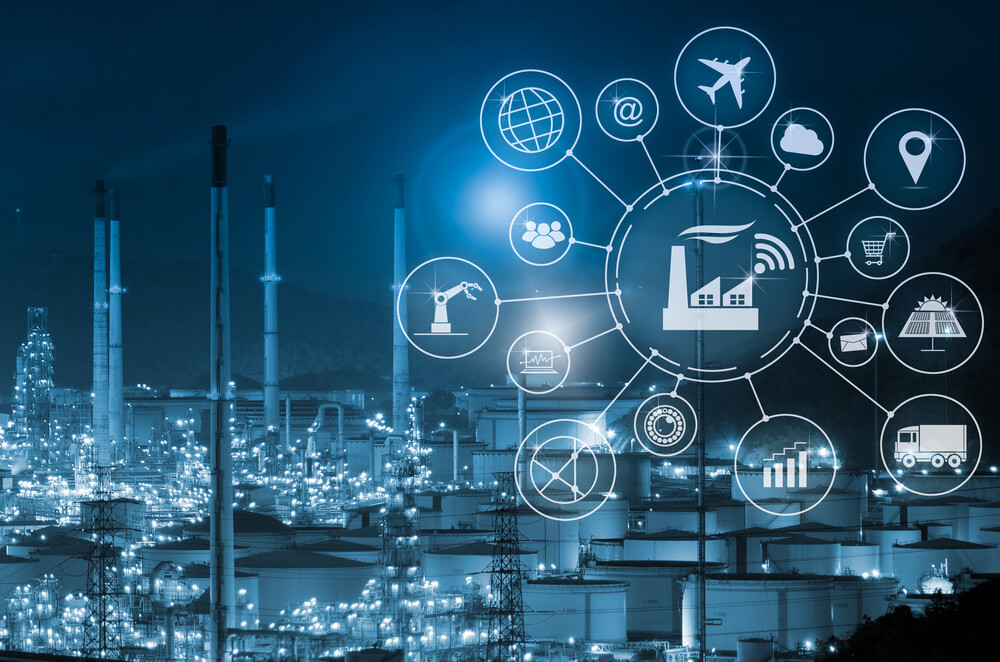
The next edition of the intralogistics dictionary is an overview of terms that appear regularly in articles on the VersaBox blog. All of them are directly linked to the possibility of using Autonomous Mobile Robots (AMRs) in carrying out internal transport tasks. This time we focus on explaining terminology associated with lean management.
Lean management
A set of rules for the organisation of industrial manufacture, the prototypes of which were production management models developed by the Toyota Motor Company in the mid-20th century. In general, lean management is the formally and scientifically described principles of the Toyota Production System (TPS). After World War II, the Japanese were looking for solutions that would allow for genuine improvement in manufacturing quality and reduction of losses. After several decades, a management model was created in which unnecessary overproduction was minimised and creation of stockpiles was reduced, as well as waiting times, load-less journeys (unnecessary transport), and any redundant traffic. The key TPS concepts are just-in-time (i.e., precisely on time) and kaizen (continuous improvement, which is not only a way to improve quality, but also a philosophical basis for the entire manufacturing process). TPS was recognised in the USA and Europe after the publication of The Machine That Changed the World in 1991. The authors described the Toyota quality system and used the term lean management for the first time.
Milk run
This term is translated into Polish as “milkman’s course” or “milkman’s loop”. It describes a model of component delivery from the warehouse to the assembly line (or manufacturing cells) and finished products from manufacturing cells to the warehouse (or the customer). The main objective is a smooth flow of deliveries, ensuring a flow of transported goods in such a way as to avoid the formation of excess stock. In practice, milk run means creating a system of cyclical deliveries in which a single transport set (e.g., an intralogistic train or an AMR) visits a set of subsequent stops of a transport loop. One of the milk run models includes the delivery of ordered components to specific points and then the collection of empty reusable containers. Delivering empty containers and collecting full ones is another possibility. The delivery routes are fixed, and the runs are done according to strict schedules. The delivery of components and the collection of finished products are small-scale, and closely matched to current needs.
Manufacturing cell
This term is used to refer collectively to a set of machines, components, and workstations set up next to each other. A manufacturing cell can be organised based on technology or around an object. In the former, a specific type of operation is performed in the cell (e.g., welding, machining, painting). In an object-based cell, on the other hand, specific products or families of products are manufactured. Object-based manufacturing cells allow for a significant reduction of finished goods transport in production facilities. Quality control is also improved, as any defects are spotted immediately after they arise and not after the component has already moved along the assembly line. Manufacturing cells are one of the main models of manufacturing organisation, in addition to the assembly line and straight-line production models.
5W (5 Whys)
The 5 Whys method is one of the elements of kaizen (quality improvement system), one of the pillars of lean management. The method was developed by Taiichi Ohno, the main creator behind the Toyota Production System (TPS, lean management). The story goes that he got the idea from conversations with his young daughter – the child kept asking seemingly naive questions that started with “why…”. Ohno realised that having to explain something to someone who doesn’t understand it allows you to find the real source of the problem.Getting to the root of the problem shouldn’t take more than five questions. If the questions keep multiplying and the issue still hasn’t been identified, it means the questions weren’t properly formulated. 5W can be a very effective method of optimising intralogistics processes, including, for example, minimising queues to load collection and delivery points.
Kanban
A term in lean management. Originally, it was a system of clearly labelled paper product cards, which were placed on a special board. Nowadays, the boards are digital. They are widely used not only in the manufacturing industry, logistics and intralogistics, but also in many other areas of the economy. Each process of creating value, e.g., manufacturing a specific product (it can be a physical product, but it could also be a conceptual one) or transporting a load, can be broken down into three stages: to do, doing, and done. The beginning and end of each stage of the process is recorded by placing a card on the board or by moving it to an appropriate place (status changes). This means it’s possible to have a constant insight into what is going on and you can quickly detect:
- shortages (of materials, components of finished products)
- formation of delays (product being held up somewhere, stoppages)
- accumulation of unnecessary stock
- queue formation
It also allows you to quickly locate places where machines and/or staff are idle or, on the contrary, the performed tasks are redundant and unproductive. In the case of intralogistics processes, kanban allows you to clearly define which load, in what quantity, where to and where from it needs to be transported.
Intralogistic train
The train consists of an industrial tugger and “carriages”, i.e., various types of transport trolleys and carts. The tugger is operated by a staff member. Internal logistics (intralogistics, material handling) that uses the milk run method requires the use of intralogistic trains. AMRs, which carry out transport tasks autonomously, are an alternative to tugger trains. They provide even greater flexibility in scaling delivery sizes, responding to changes in quantity demand, and the type of loads transported. Instead of creating a transport depot, you can dynamically allocate individual AMRs to carry out specific manufacturing processes.