How does VersaBox do it? Comprehensive AMR implementation
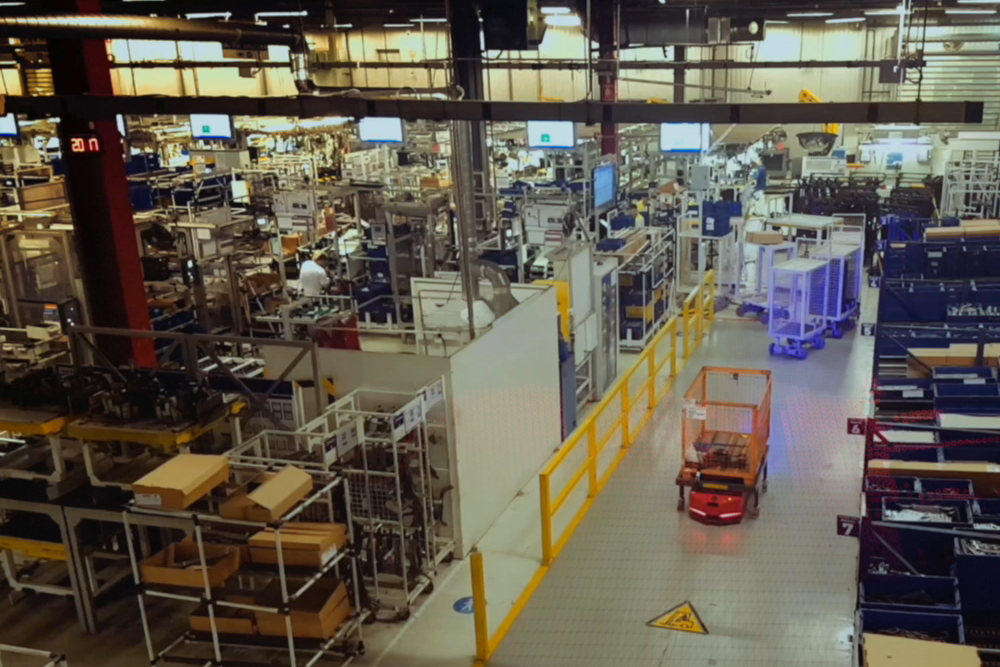
VersaBox has created a system that allows customers to easily switch from traditional intralogistics to using AMRs. The solution is flexible and extensive. Versabots can be introduced into existing manufacturing plants and warehouses, without the need to change their layout. VersaBox as an AMR manufacturer provides hardware, software, consulting and maintenance services. The system is fully scalable – from one robot to an entire fleet, consisting of several or dozens of units.
“From the beginning of VersaBox’s existence, we have strived to create a comprehensive intralogistics solution,” says Paweł Oziębło, Business Development Manager at VersaBox. “All successive projects were testing grounds for our robots, but also for our organisational structure and implementation methodology. We currently have an extensive and complete system that allows for very short deployment times, and at the same time it’s easy to scale and open to further development,” concludes Oziębło.
5 steps of intralogistics robotisation with VersaBox
The standard model of cooperation consists of 5 steps:
- Meeting with the customer – when the sales staff make appointments to meet with customers, the clients usually already know the capabilities and functionalities of VERSABOT robots, because they had participated in a presentation pitch, a webinar or watched videos – this means that the staff can quickly move on to discussing the offer details;
- Preliminary project – if the meeting with the sales staff ended with a cooperation agreement, a preliminary project is created – a general simulation and visualisation of how the robots would operate in the manufacturing plant or warehouse layout;
- Offer presentation – a detailed project and simulation are created, taking into account all available data on the working environment in which the AMRs are to be deployed – the customer receives a detailed offer, which contains precise data on the expected effects of the implementation, i.e. how many and what kind of loads the robots are able to transport within a specified time;
- Implementation – the physical introduction of robots into a facility is a verification of the simulation prepared earlier – it’s a clash between the theoretical project stage with the realities of the working environment, a time for final adjustments and “fine-tuning” of the intralogistics system;
- Operation and maintenance – under normal operating conditions the customer can carry out a lot of the maintenance on their own, after undergoing appropriate training – the only thing they don’t have access to are the safety systems, classified data, or any solutions under patent protection. Of course, even after prior training, the customer is provided constant support and can count on our help any time.
If there is ever a need to make minor adjustments in the way the robots operate, this can be done by the user themselves. In case of major system upgrades, e.g. related to a change in the warehouse layout, the support of VersaBox specialists is usually necessary.
What’s the service life of an AMR?
AMRs, like any other machine, require ad hoc cleaning, and periodic maintenance and repairs. In the case of Versabots, repairs are limited to replacing damaged modules. As a result, downtime is kept to an absolute minimum. However, the simple and easy replacement of all structural elements affects the service life of a machine.
“Our robots are machines with a very low failure rate,” says Paweł Oziębło. “Technical problems are usually not caused by operational breakdowns but are due to physical damage to the robot, e.g. being hit by a forklift. If you choose a model with replaceable batteries, then the robot can operate almost continuously and for as long as you need it to, not counting inspection and maintenance breaks.”
Versabots make use of a lot of ready-made, easily available components. This means that maintenance is even simpler and cheaper.
Unpredictable human factor
Clearly defined and repeatedly proven procedures allowed for a reduction of the AMR implementation time down to two weeks.
“We try our best to recognise the customer’s expectations, the details of the tasks to be performed by the robots, and the conditions in a particular facility. The more detailed the analysis, the fewer surprises appear during the implementation stage,” emphasises Paweł Oziębło. “Of course, that’s the ideal flow. In reality, there are sometimes many surprises. These are usually the result of robots interacting with people. It’s practically impossible to predict human behaviour at the pre-deployment analysis stage. This is why the initial period of operation is so important – we monitor the robots, make adjustments, and train staff who will be working in a shared space with the robots.”
Human-robot collaboration a key to success
For the system to run smoothly and with maximum efficiency, people need to get used to the presence of robots. They must also learn to understand their capabilities and how they operate. A good example is the way robots “see”. A robot scans its surroundings approximately 10 cm above the surface of the floor. If it comes across a forklift with its forks raised a dozen centimetres, a collision may happen. A robot can be equipped with appropriate sensors and 3D cameras, but this significantly increases the cost of purchasing one. Besides, practical experience shows that a lot of collisions are due to forklift operators forcing the right of way.
Robots need predictability and repeatability to operate, e.g. ensuring that transport routes aren’t blocked with pallets abandoned in the middle of aisles. The process of “break-in” of an intralogistics system involves the gradual tidying up and organising of the working environment. The better the organisational culture at the beginning, the faster the whole system achieves optimal operating parameters.