5G in the industry – are cables a thing of the past?
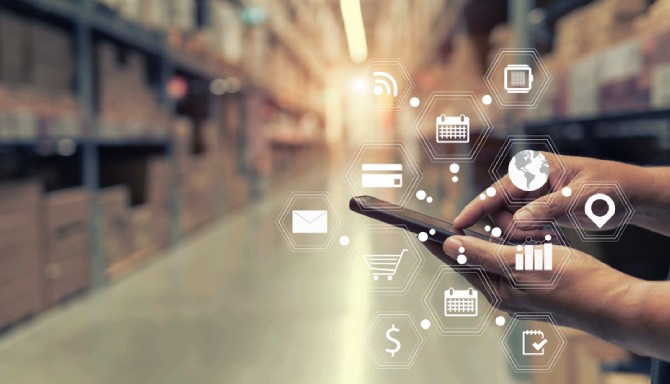
According to optimists, 5G will replace industrial cabling. Intelligent machines that make up the Industrial Internet of Things (IIoT) will wirelessly connect with each other, with production management systems, and with cloud analytics. Broadband transfer (several hundred percent more efficient than currently used technologies) will make smart factories and warehouses truly smart and fully autonomous.
Opponents of 5G are in the minority, and their arguments boil down to two issues: whether modern radio transmission will have a detrimental effect on our health (there’s currently no evidence to back up that claim), and the security of transmitted data. The latter may prove to be crucial, but there’s no doubt that it won’t hinder the development of new technology. Giants of the IT industry, led by Siemens, have already announced billion-dollar investments into research on the use of 5G for industrial purposes.
Each factory will have a virtual twin
The transmission capabilities of 5G come with great hopes for the dynamic development of digital twin technology. It involves creating virtual models of factories, warehouses, power plants, refineries, mines, power grids, road or rail networks, metro lines, airports, and hospitals in the cloud (one that can offer adequate computing power, of course). In principle, any industrial and production plant, communication or transmission network, public institution or private company can have a “virtual twin”.
A digital twin is a faithful representation of a real object, organisation, machine, system or even a single process. In ideal conditions, the creation of which will be possible thanks to 5G, the twins maintain a constant connection, and the data flow between them takes place in real time. Every change in the real world is simultaneously, and without any delays, mapped in virtual reality. This creates some very interesting possibilities:
- Ongoing monitoring and remote management – knowing the current state of machines and processes allows you to fully control them – you can instantly respond to any irregularities, make necessary corrections, or automatically send alerts and reports to the relevant services and individuals. Management is possible from anywhere, from any device with Internet access.
- Predictive maintenance – machine models based on process data (temperature, vibration, mechanical wear, efficiency, energy consumption, intensity of use, operating mode, etc.) collected throughout their lifetimes (a virtual model can be based on any number of similar or identical devices), allow you to implement a predictive maintenance strategy that aims to predict failures before they occur, and thus completely eliminate unplanned downtime.
- Modelling and testing of processes – every planned innovation can be tested on a virtual model, which minimises costs and the financial risk associated with making changes in the real world.
As you may have noticed, all these possibilities are based on data that’s continuously generated by machines. Currently, only a small percentage of this huge information stream is being used. One of the obstacles is low network bandwidth, which is going to be solved by 5G technology.
Production becomes a service
5G enthusiasts are convinced that by exchanging huge amounts of data in real time, it will be possible to redefine the concept of a factory. In the future, it won’t be a place that supplies ready-made goods, but a potential based on technologies, machines, processes, and raw materials. Factories will not offer products, but the service of making them.
Currently, the closest thing to this sales model are car configurators used by automotive manufacturers. In the near future, instead of choosing from a range of ready-made options (e.g. paint colour or upholstery material), you will be able to design your own car body or the entire car from scratch, i.e. create your own brand. Not only that – thanks to the development of augmented reality (AR) and virtual reality (VR), you’ll be able to test and improve your car before any part of it is manufactured. Needless to say, the development of VR and AR will greatly accelerate with the advent of 5G.
Robotisation with 5G strength
Far-reaching production flexibility, while still maintaining its profitability, will ultimately require complete automation. Only smart machines will be able to ensure excellent internal transport efficiency, and cheaply and quickly produce goods that meet the highest quality standards. People will only perform supervisory and maintenance duties. But even those will be subject to automation in the long run (most likely based on the use of Artificial Intelligence). The development of these areas of industrial manufacturing may rapidly increase, thanks to broadband data transmission.
However, it will be a few years before we can experience this bright future, and in some parts of the world it might even be a few decades. Especially since the use of wireless connectivity to control production equipment raises many fears and doubts. At present, it seems unlikely there’s a need to use wireless connectivity in production hubs. However, if in the future we want to quickly adapt production lines (treating machines and devices as “building blocks” of sorts), mobility and wireless connectivity maye be a necessity.
All of that is still in the future. However, thanks to a large extent to 5G, we will soon see an “invasion” of autonomous machines, primarily in industry and logistics. The takeover of intralogistics by Autonomous Mobile Robots (AMRs) seems almost as obvious as the fact that the future of long-distance transport is autonomous electrical trucks. In both cases, remote fleet management will be much easier using broadband data transmission.