What is automated guided vehicle – AGV?
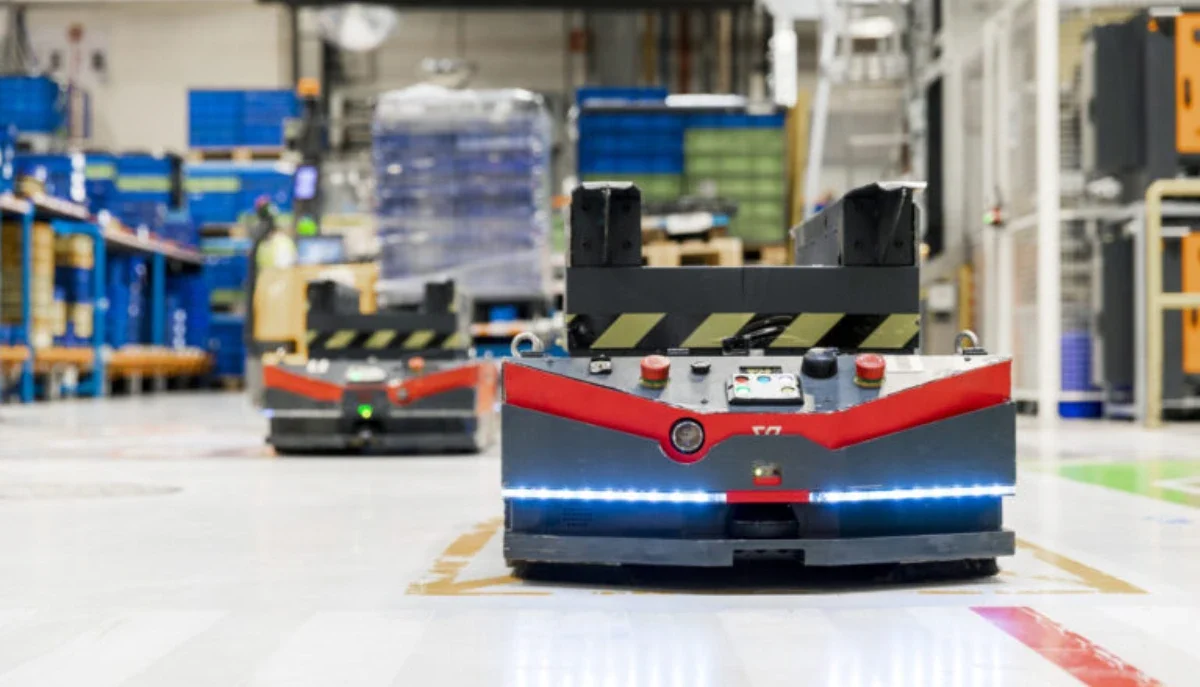
Efficient intralogistics is a cornerstone of any manufacturing plant or warehouse. However, high-speed roller conveyors or conveyor belts cannot be installed everywhere – among other things, AGV-type mobile robots are helpful in such situations. What exactly are they, what are their uses, and why should you use them? The answers to these questions can be found below.
AGV mobile robots – what exactly are they?
AGVs (from Automated Guided Vehicles) or Automatically Guided Vehicles are various types of transportation machines that can move independently and operate without an operator. They can range in size from small, nimble carts transporting light materials between production nests, to considerably large machines that can easily carry up to several tens of tons. Various types of automated guided vehicles used in a single facility can be connected into AGV systems, which can greatly enhance any manufacturing process. All you need is the right software, peripherals (e.g. charging stations), and occasionally some infrastructure tweaks (depending on the types of AVG used). Some people also refer to AVGs as Automatic Guided Vehicles, but that’s not the correct expansion of that abbreviation.
The simplest self-propelled transport trucks can only move along a designated route – older models required special wires to be placed in the floor to generate a magnetic field. Nowadays, however, they use much less invasive ferromagnetic or reflective tapes applied directly to the floor surface.
Newer and more advanced models are equipped with cameras that allow them to read special markers placed on the walls and avoid obstacles that may have appeared on their route. An AGV system can be implemented in virtually all manufacturing facilities – just a few of these machines can significantly accelerate production processes by making production lines more efficient.
Types of automated guided vehicle
An automated guided vehicle system can be comprised of many types of AGVs, many of which were made to perform a specific task. Here are some of the most popular options (in random order):
- Automated Pallet Jack – specifically made for moving pallets around. These load carriers can pick up cargo from the floor or from elevated platforms (e.g. production lines) of up to 1,5 m height.
- Unit Load AGV – widely considered to be the best alternative to traditional conveyor systems, these fast carts can transport raw materials and various goods across the facility.
- AGV Tow Tractor – the best option for towing multiple trolleys at once. However, it’s not very practical in smaller spaces.
- Very Narrow Aisle AGV – a great option for warehouse automation. These machines can deposit pallets on racks up to 12 m high, while requiring only 1,7 m of aisle space to move freely.
- Automated Guided Cart/Under Ride – fast and agile, this smallest type of AGV solutions is ideal for intralogistics in e-commerce. They can easily tow carts, trolleys, and handle most totes transporting materials used in internet sales.
- Automated Reach Truck – this is the thing you should get for a production environment requiring stacking raw materials/ready products on high racks in wide aisle warehouses.
- UV Robot – a relatively fresh product that can significantly speed up disinfection in various facilities. It’s an essential asset for the pharmaceutical industry and food processing plants.
- Automated Forklift – these robots can transport inventory of the highest load, just like their human-operated counterparts. They can easily deal with virtually any warehousing and distribution applications in almost every manufacturing and distribution facilities.
Autonomous Mobile Robots
A separate category of automated guided vehicles is AMR or Autonomous Mobile Robots, which are a real breakthrough in material handling technology. What makes them different from typical AGV robots? Thanks to a system of cameras and laser sensors, they are able to scan their surroundings and autonomously choose the optimal route to take when executing a specific sequence of commands. What is significant – these systems do not need the installation of any infrastructure (such as tapes on the floor or a system of mirrors) so their installation is cheaper, faster and more flexible. You can learn more about them in our dedicated post. Our flagship products VERSABOT 500 and VERSABOT 1500 fall into this category. AMR robots have another common feature: they are devices that cooperate with their environment (operators and other handling equipment). What sets them apart from ordinary robots (both transport and production robots)? Unlike the latter, they can work in the immediate vicinity of people without being separated by special barriers. And this is thanks to a safety system and the installation of special sensors that continuously monitor their immediate surroundings. Such technological advancements make the robot stop when something comes within its range and avoid stationary objects, eliminating the risk of collision.
Applications of AMR robots
AMR trucks can be used in virtually any intralogistics process – their main task is to transport products and materials within the production plant, warehouse, between loading and unloading stations. Depending on the process and specific transportation tasks, a particular type of AMR robot will be used:
- Single-load robots – the most common version of AMR trucks carrying single loads of different shapes and sizes on them, such as drums, racks, pallets, or containers of non-standard shapes. They can be loaded using roller conveyors, chain conveyors or other loading stations and carry up to tons of cargo. Overhead loading provides ample maneuverability for the truck, allowing them to navigate even narrow and complicated paths. They work very well in distribution centers, warehouses and production halls, and as an extension of conveyor belts into harder-to-reach places.
- Transportation – small-sized mobile robots that can work as towing devices for a single cart. The advantage of such a solution is that the carts can be automatically retrieved and put away so that they can continue to be retrieved by the production station operator for ergonomic use.
- Autonomous forklifts – popular especially in distribution centers and warehouses, versatile vehicles that can handle a variety of loads from pallets or standard containers. They are very agile and can maneuver efficiently even in very confined spaces.
Why use automated mobile robots?
Automatically controlled vehicles bring many benefits, the most important of which are:
- The ability to integrate with a warehouse management system – a warehouse information system (otherwise known as WMS from Warehouse Management System) enables efficient management of all logistics processes taking place in the warehouse. Robots are fully compatible with such systems and can further improve warehouse operations and even introduce full automation.
- Efficient flow of materials and goods – all transported cargoes always reach their destinations on time and in the right quantities, eliminating downtime.
- Increase the level of safety in the plant – thanks to the aforementioned sensors, AMR robots will not bump into any obstacle. With the right configuration, we will also get the assurance that they will not drive into unplanned areas.
- Reduction of costs associated with internal logistics – by increasing the efficiency of internal transport, the investment will pay for itself in just a few months. And you can save a lot on the work of robots, such as lighting, which they do not need at all.
- Maintaining the continuity of plant operations – so production can continue uninterrupted throughout the year, as long as we take care of the availability and flow of cargo.
AMR/AGV robots – summary
Regardless of their type, the use of AMR robots makes it possible to significantly improve the efficiency of intralogistics. Of particular note here, however, are the fully autonomous mobile robots, which continuously plot optimal travel routes for themselves, saving time and avoiding any obstacles. Even a single robot can clearly improve the flow of materials and finished products, and by having several of them, you can begin the process of automating plant operations. This innovative technology is the way to go if we aim at reducing human error and making any manufacturing facility ready for joining Industry 4.0.