DIGITAL RUN AT RATE
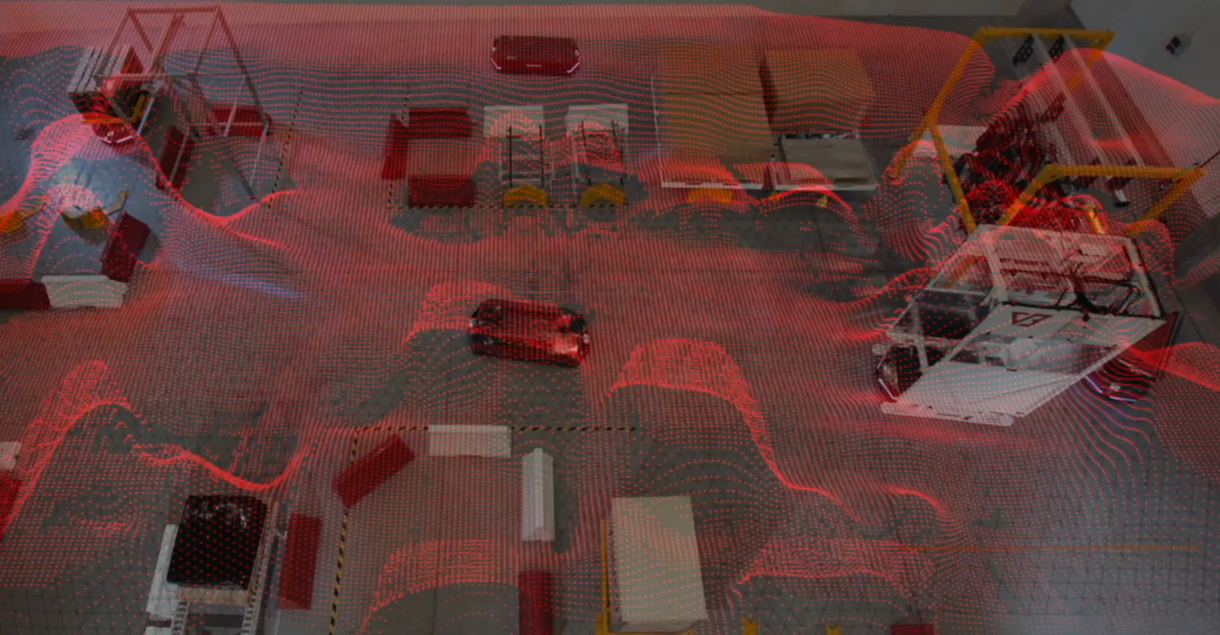
Run at rate (run@rate, run&rate) most often means a trial series of products before the proper mass production process starts. However, it can just as well apply to any process that results in a certain “product”. Run at rate procedures are also suitable for trial runs of intralogistics systems based on AMRs. In this case, the whole process can be carried out without physically interfering with the internal transport system already in place, and even before the space where it’s to be implemented is built. These are the possibilities offered by the VERSABOX VIRTUAL FACTORY™ tool.
What is run at rate?
In a financial context, run at rate means developing forecasts for the future based on current turnover data. For example – a company listed on the stock exchange generated a net profit of 2.5 million in the first quarter, so shareholders can expect 10 million to be distributed within the entire year. Under manufacturing conditions this is a kind of test – a release of a sample batch of products in order to verify the theoretical assumptions regarding the production volume in a given time frame, while maintaining the required quality standards. In the case of intralogistics, run at rate aims to check the “efficiency” of a finished internal transport system.
There is no one-size-fits-all set of run at rate procedures. They must be adapted to specific kinds of manufacturing or process. However, the goal is always the same: to obtain confirmation that a given process will achieve the desired quantity and quality of the finished product. Many run at rate models also check the ability to exceed the required values (e.g., number of finished products, or the volume of transported loads). As an example, the surplus value can be set at 120%. This allows you to protect yourself against periodical increases in demand. This is especially true in the case of seasonal goods manufacturers.
Run at rate procedures in intralogistics
The traditional way of carrying out run at rate procedures requires all components of the intralogistics system to be assembled in a physical, three-dimensional space. Otherwise, it’s impossible to obtain valuable (verifiable) results. This means that you must have a complete set of AMRs, install charging stations and parking spaces, and load collection and delivery systems. It’s also necessary to adapt transport routes (installation of markers, horizontal marking of traffic routes), and often relocate manufacturing equipment or storage racks. Training should also be provided for operators of other transport machines, as well as staff who will be working alongside the robots. Only a fully organised system can be reliably tested.
The traditional way of preparing a trial run of an intralogistics system is time-consuming and expensive – even assuming that most forecasts and predictions are confirmed in practice. Costs increase exponentially whenever errors occur. Additionally, each modification, such as introducing a new robot or changing a route, means all procedures have to be carried out from the beginning. You can avoid tedious system setup and expensive tests if you use the tools offered by VersaBox. These tools allow you to obtain reliable run at rate results even before the deployment of AMRs into a production hall or warehouse.
Modelling and optimisation of intralogistics processes
We know that one AMR is able to transport a certain number of payloads in a given time frame, e.g., tonnes or units during one shift. It seems logical that if we want to transport twice as many loads in the same amount of time, we should use two robots. This kind of scaling works, but only up until a certain point. It might turn out that increasing the fleet from 5 to 10 robots will not double the number of transported loads. Why does that happen? Finding an answer during the implementation process can be extremely difficult and expensive. Using the VERSABOX VIRTUAL FACTORY™ tool is much more convenient, cheaper, and most importantly more effective.
The tool developed by VersaBox is used to design, simulate, and optimise intralogistics processes. You can use it to carry out any number of run at rate processes aimed at AMR implementation. All you need to do is provide the software with the right amount of data. You need the hall layout with defined transport routes, end point locations, and charging stations. This is enough to design a new system and introduce updates to existing processes. The virtual model created using the VERSABOX VIRTUAL FACTORY™ allows you to test any intralogistics processes. You can easily examine the consequences of introducing new robots, changing transport routes, relocating load collection and delivery points, or the charging station.
It’s worth noting that it’s possible to accelerate the processes taking place in the virtual model. This means forecasts and predictions that are not only effective, but quick as well. By observing the virtual model, you can get answers to your questions, and diagnose and solve problems that you wouldn’t have been able to detect in time using traditional tools.