What is a smart factory?
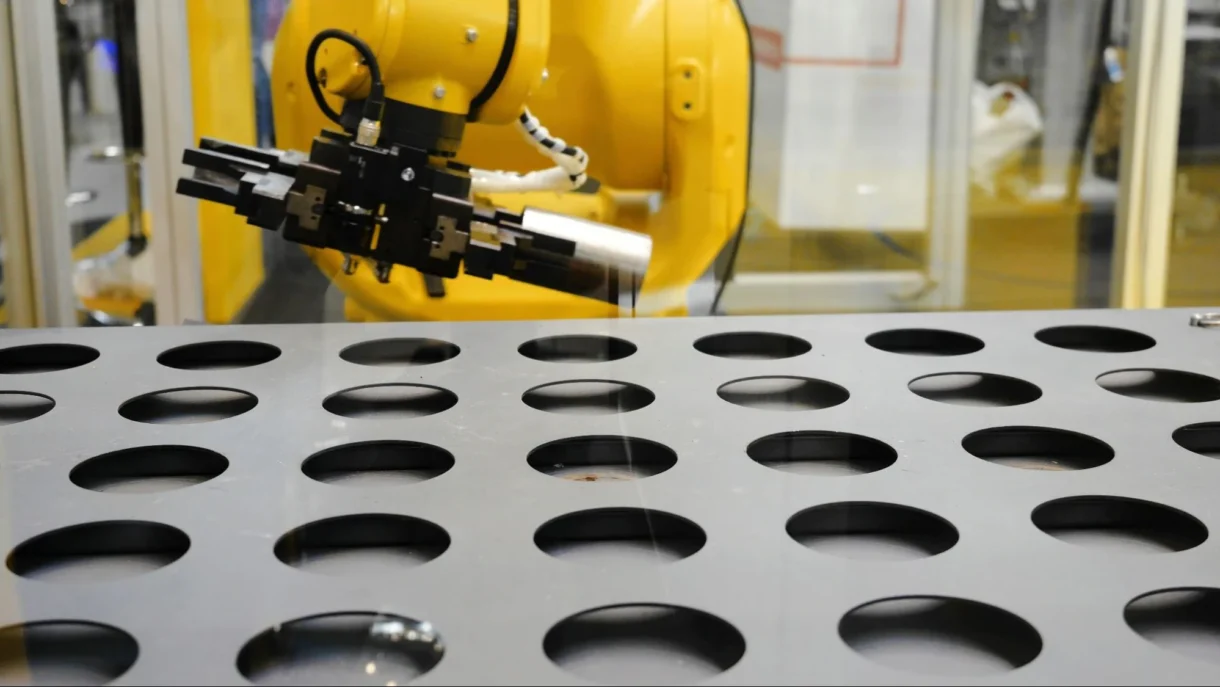
[vc_row][vc_column][vc_column_text]Smart factories are an essential part of the so-called fourth industrial revolution (or Industry 4.0). In short, this concept is based on a high level of automation in manufacturing processes, supply chain management, and intralogistics. Let’s take a closer look at smart factories, the technologies they utilize, the benefits they bring, and ways to transform ordinary factories into smart production plants.
What are smart factories exactly?
A smart factory can be defined as a cyber-physical system of interconnected machinery, devices, and production systems that utilizes the newest technologies to continuously collect and share data. This data is then used as a base to optimize each manufacturing process and supply chain in the factory.
Smart factories require minimal human intervention, especially if they are fully automated – human workers have purely a supervisory role or can be delegated to more ambitious tasks.
How does a smart factory work?
Contrary to traditional factories, all the assets in smart manufacturing work as one thanks to a digital ecosystem that connects them. This unified system includes, among others, people, machines, artificial intelligence, and Big Data. With the right tools, a smart factory will not only curate and analyse data, but also use these data sets to create forecasts of trends and events. Thanks to that, automated processes and smart manufacturing workflows can continuously self-correct – a smart environment can self-optimize and evolve into a safer, more productive, and more resilient system.
So, after the implementation of smart solutions, there won’t be any ‘solitary islands’ and each part of the factory will be able to communicate with others, thanks to real-time data collection. This allows for much easier coordination and smooth workflows in every possible scenario.
Basic smart factory structure
There are three main procedures that take place in every smart factory:
- Data acquisition – through the use of industrial Internet of Things (IoT) and artificial intelligence, smart factories can collect and compile massive amounts of data. The data can come from manufacturing processes, supply chains, intralogistics, and any external source that’s relevant to the factory’s work. The external sources can be anything from regulations, through market trends and consumer expectations, to news about technologies that can help in achieving maximum performances.
- Data analysis – the factory’s database is continuously analysed through machine learning, intelligent business systems, and other modern data management solutions. Data sets created by this process can be easily compared and allow for constant self-optimization, based on various supply chain forecasts and possible future scenarios.
- Intelligent manufacturing/factory automation – the gathered and analysed data becomes the base of workflows and instructions sent to every device and machine in the system. This allows for e.g. quick identification of potential hold-ups in the production process, predictive maintenance of machines, and adjustments to production quantities based on emerging demand. Thanks to Big Data analytics, the entire production process can be easily optimized with the most suitable smart factory solutions.
Main smart factory technologies
Various technologies can be utilized to make a factory ‘smart’. Practically all of them are a vital part of the aforementioned fourth industrial revolution. Here are some of the most frequently implemented ones:
- Sensors – these are used for collecting varied types of data about the manufacturing process. Sensors can be placed on various machines/devices and be linked to a shared network.
- Cloud Computing – this can be explained as off-site storing and processing data. With this technology, it can be done cheaper than creating and maintaining on-site data centres. Moreover, cloud solutions allow flexible and real-time access to the data analysis results, allowing for faster decision-making.
- Big Data Analytics – processing large amounts of data can provide insights and lead to a thorough analysis of each production process. This allows you to spot error patterns, test an iterative production process from different angles, and create highly accurate predictive quality assurance. Plus, the data can be shared between your other factories, thus providing solutions for common problems and smart manufacturing practices.
- Digital Twins – as the name suggests, this technology provides you with a simulation of a physical object or a single process. A digital twin is not only an extraordinary tool for quality control and planning, but also a low-cost way to test new machines and solutions before buy/implementation. All you need is the technical data and the simulation will run the proper tests for you.
- Augmented/Virtual Reality – the first one is a digital technology that overlays digital information across reality. Such information is viewable through smartphones or other similar devices. Virtual reality provides an immersive virtual world, viewed through special glasses. Both can be a great boon for smart factory operators, e.g. helping in production tasks, products organisation, and equipment maintenance/repairs.
Benefits of smart factories
Introducing smart solutions into your factory will bring many benefits and give it a competitive advantage over traditional industries. The main areas positively impacted by smart technological transformation include:
Product quality and customer experience
With the introduction of the shared data network provided by cloud connectivity, a smart factory allows for full end-to-end visibility. This means that all the instructions will be clear at every step of the manufacturing process and the final product will be an accurate reflection of the initial objectives. Moreover, constant data collection and analysis allow for agile adjustments to the production process, making it optimal for a given product.
Smart systems also allow for real-time reactions to customer experience – you can easily adjust your processes based on current market trends, reviews, and competition’s activities. This will lead to more satisfied customers, fewer recalls/returns, and a more customer-friendly business model.
Productivity and efficiency
Smart factory is no longer a reactive business – smart technologies allow for a much more proactive approach to manufacturing processes. All the shortcomings can be identified and dealt with much quicker, often before the product leaves the factory. The real-time data analysis and automated processes lead to higher productivity, while the ever-going optimization ups the efficiency of each process.
Safety and sustainability
Introducing modern industrial robotics into your factory can make your factory a much safer workplace. First, robots can take over the handling of hazardous materials. Second, autonomous trolleys are much safer than traditional forklifts (no overloading, risky manoeuvres, or collisions with obstacles). Third, there’s no risk of robot arms hitting human workers thanks to the network of RFID sensors.
A smart factory is also much more environmentally friendly – digital transformation reduces the facility’s carbon footprint, e.g. by replacing gas-powered transporters with robots or switching off the light in fully automated production halls. Such practices are appreciated by an increasingly large group of consumers, who are willing to spend more on products that are manufactured in an eco-friendly way. So by going ‘smart’, you can make your business more sustainable and reach wider markets.
How to make a factory ‘smart’?
At first glance, switching to a ‘smart’ business model might seem as a huge and expensive endeavour, but in reality, effective and fast changes can be made without excessive interference in the manufacturing chain.
First, pick out the most important parts of your manufacturing chain and thoroughly analyse them. Data from this analysis will show you what should be improved first.
To avoid biassed opinions, make sure that this analysis is done by a diverse team, composed of specialists from various areas of the business. The changes will be the more effective, the more workforce is involved in the improvements. Be ready to provide employees with necessary training, as they will need updated skill sets as their work tasks change with the new solutions.
IT systems specialists, management, and engineers should work hand in hand to find areas for improvement and draw plans for reducing costs, increasing sales, saving time, and optimising processes.
Smart factory – summary
A smart factory is a vital part of the so-called Industry 4.0 – by implementing new technologies into your factory, you will not only future-proof it, but also increase its productivity in a relatively short time. You don’t have to ‘smart up’ your business all at once – smart solutions can be implemented sequentially, starting from the most vital parts of the manufacturing process. Many businesses get satisfying results from just partial digitization, but full digitization gives you far more flexible and agile production facilities.[/vc_column_text][/vc_column][/vc_row]