DOES EVERY FACTORY NEED A DIGITAL TWIN?
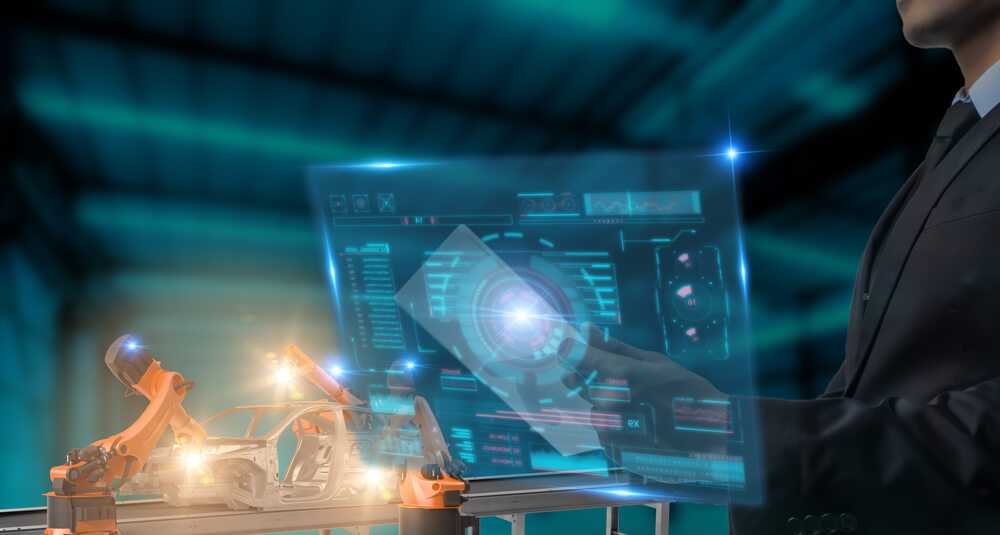
Not yet. However, it will have to have one soon in order to effectively optimise costs, predict malfunctions and breakdowns before they occur, prepare products in small batches, and react quickly to the changing demands and preferences of customers. Factories will have to create a digital twin to survive in a global economy.
Digitalisation may apply to the entire factory or just selected processes. One of the key processes is internal transport, which offers great potential for optimisation with relatively low entry costs. On the condition that you use AMRs and the AUTONOMY@WORK platform, of course. How virtual twins work, and what opportunities they create, is best illustrated by a famous historical event in the 20th century.
How was the filter on Apollo 13 fixed?
The Apollo 13 mission was a series of unfortunate events. This meant that the astronauts missed their chance to land on the Moon. To make matters even worse, they could have died as a result of a simple malfunction of the carbon dioxide filter. Specialists in the Mission Control Center had data on all the materials, tools and devices present on the shuttle. They collected an identical set back on Earth and asked themselves a question: how to repair a carbon dioxide scrubber using only the equipment available to the astronauts? On 15 April 1970, the filters started working again.
You could say that NASA scientists used a model that we now know under the name digital twins. They had the layout of the shuttle. They also had information about the location of key objects and the processes taking place within it. They could manage the situation based on data (data driven). They took data from the environment, entered it into a model, analysed the problem, and found a solution that proved to be successful.
What do digital twins do in factories?
The virtual twin of a factory is a representation of the production hall, its equipment, and machines in the form of a digital model. If necessary, virtual models of human staff can also be created. All of these creations must interact with each other, which means the model should also recreate the relationships between objects.
The more data we enter into the model, the more complete it will be, and the closer to the actual physical object. All of this will make the model more accurate when tested. A constant influx of new data is also incredibly important. For this to work, you need to install various sensors that collect data about the state of machines and processes. Based on measurements of temperatures, vibration levels, and current carrying capacities it’s possible to very precisely monitor the condition of machines and predict upcoming malfunctions with high probability.
The ideal digital twin is a model powered by real-time data. This allows for an effective analysis of existing problems, testing of solutions using the model, and sending information (specific instructions) back to the real factory. Analysing huge amounts of process data (Big Data) is possible thanks to the use of artificial intelligence. All of the above transports us into the realities of Industry 4.0, or a fully automated factory of the future.
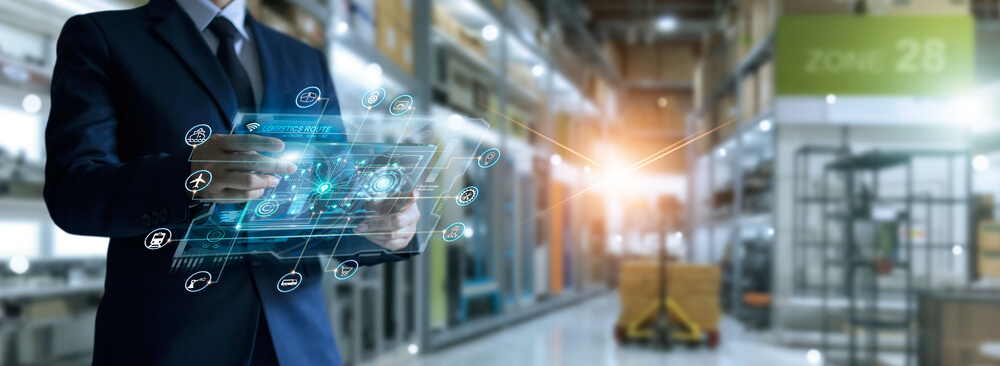
Modelling intralogistics – first step towards factory 4.0
The development of complete virtual twins of factories is slowly becoming a reality. Modelling internal transport could and should be a gentle entry point into this new reality. Using the AUTONOMY@WORK platform, you can create an intralogistics system based on AMRs.
The system developed by VersaBox offers all the functionalities necessary to design a system, for its implementation, and the management of a robot fleet. It also includes the VERSABOX VIRTUAL FACTORY™ tool, which is used to model and optimise intralogistic processes. In practice, this means it can be used to create a virtual twin of an internal transport system. It works according to the descriptions above – it analyses data from an actual production facility in order to test solutions to real problems on a virtual model.
VersaBots create new quality in intralogistics
It might seem that introducing AMRs into factories is just a simple change in contractors – from people to VersaBots. However, the introduction of AMRs and the fleet management system is a significant change that goes beyond a simple reproduction of already existing intralogistics processes.
Robots come with predictability – they don’t make mistakes, don’t get tired or sick, and don’t get overly emotional. They can work non-stop with short breaks for charging their traction batteries. These just some of the changes they bring to a factory. However, they’re more than enough to recognise that we’re dealing with a paradigm shift in how we think about the design and the efficiency of intralogistics processes. If we carefully recreate them in a digital model, fleet management and optimisation of transport processes will be more effective than ever before.
AUTONOMY@WORK and VersaBots, along with the necessary additional equipment (traction battery charging stations, load collection and delivery systems), are a complete software and hardware solution. Thanks to it, it’s possible to create from scratch or modernise an existing internal transport system to the level of Industry 4.0. In other words, you can take a step towards a major change from which there is no turning back. And already you can achieve real savings, increase efficiency, and reduce losses. In the near future, you can ensure your competitive advantage and, as a result, survive in the global market.