AMR: THE NEW NORMAL
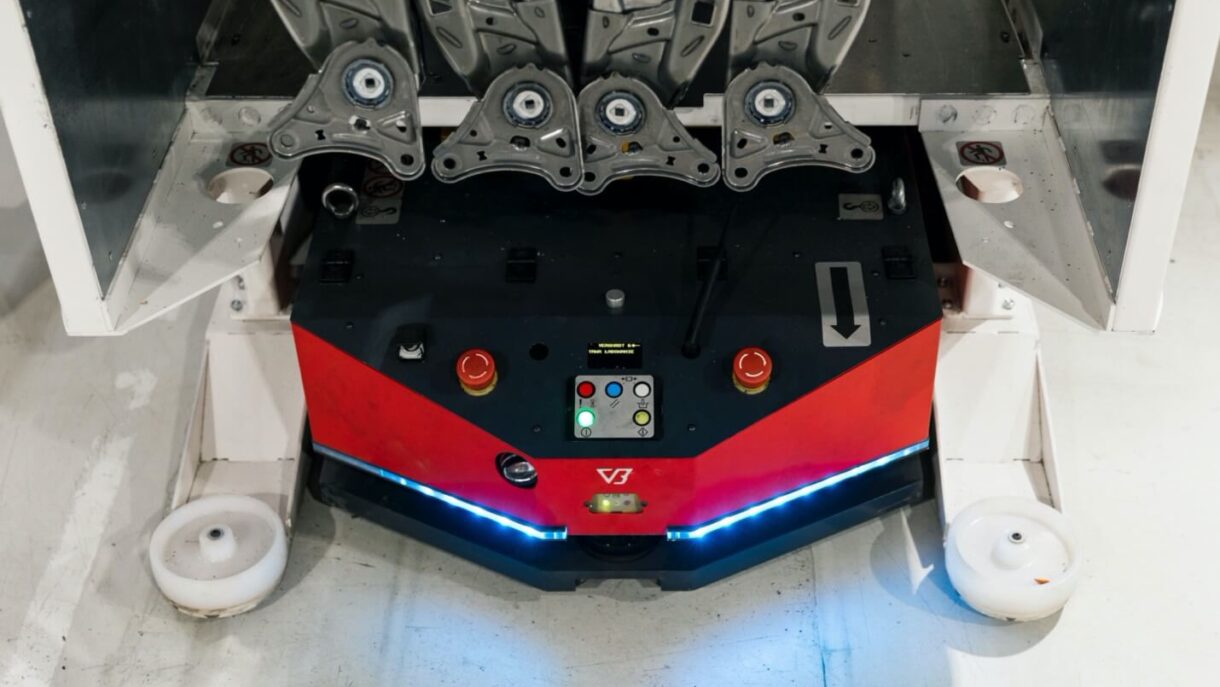
“New normal” is a term to describe the state of slowly returning to normalcy, which took place after the global economic crisis in 2008-2012. These days the term may also refer to the use of autonomous robots, which – although programmed by people – perform tasks previously intended only for humans. Read on to find out why the “new normal” is the future of intralogistics.
Autonomous mobile robots – application and operation
When talking about autonomous mobile robots, we can distinguish several types of machines that differ significantly in appearance and purpose. There are also fundamental differences between automatic and autonomous robots.
AMRs and AGVs – main differences
AMR stands for Autonomous Mobile Robot and is used to describe modern, independent, and smart mobile robots. AGV stands for Automated Guided Vehicle, which means automatic but not independent robots – they navigate using a network of fixed routes and have a limited ability to adapt to new conditions.
AMRs use a system of sensors for navigation, which allow them to adjust their operation and transport route based on an ongoing analysis of the overall situation. AGVs need physical markers for navigation, such as magnetic tapes, induction loops, or lines painted in colour on the floor. To summarise – AMRs are distinguished by flexibility and the ability to react to various situations they encounter in their environment.
Autonomous mobile robot with a hook
TThis is a smart, self-propelled AMR equipped with a special tow hook. Using a 3D camera, the AMR detects the trolley waiting for it in the designated place, then attached the trolley to its tow hook, and delivers it to its destination. An AGV, however, can only move around a previously mapped area, avoiding obstacles and people.
Autonomous mobile robot for pallet transport
The vehicle drives under the pallet, lifts it, and transports it to a specified location. The transporting robot navigates along its route on an ongoing basis and uses scanners to locate the proper stand, docks, and then lowers the load. The robot is in constant communication with the fleet manager, which provides it with up-to-date information on stand availability and its assigned transport tasks. Software running on a central server manages robot transport orders. If a robot is waiting for a load or a free drop-oof point, the fleet manager parks it in a special rest spot or docking station.
Autonomous mobile robot cooperating with a roller conveyor
Robots can cooperate with other machines. A lot has changed in the intralogistics industry over the recent years. Until recently, transport was done using roller conveyors, which were large and bulky, and took up a lot of space. A roller conveyor also has the disadvantage of being relatively difficult to modify on an ongoing basis. Traditional roller conveyors are very popular but in the face of the latest technological solution – autonomous mobile robots – they turn out to be inflexible and unable to adapt to the needs of modern warehouse processes.
VersaBox mobile robots, equipped with a special accessory in the form of a roller conveyor, come to the rescue. VersaBox robots can easily replace a network of roller conveyors in a factory. The robot cooperates with the roller conveyor, can dock next to it, and communicating with the conveyor’s controller enables it to pick up loads from it. An AMR drives up, fits in precisely using a special marker, and signals the conveyor to start its rollers (along with those on the robot).
Application benefits
Autonomous mobile robots have the ability to adapt to the current situation in a warehouse or manufacturing hall. An AMR maintains a constant pace and efficiency, and in the case of a breakdown another robot takes over its tasks. An unmistakable benefit of autonomous vehicles is also the fact that they can operate in a shared space with people as well as other robots.
An alternative to traditional systems
A traditional belt conveyor is a large, costly, and time-consuming investment. Failure of a single element leads to a complete standstill on the entire transport line. Even if AMR units are slower than traditional belt conveyors, their advantage is that they guarantee certainty, continuity, and regularity of deliveries, which translates into higher overall efficiency of transport processes.
Effects of robotics on health and safety at work
Both AMRs and fully automated belt conveyors are modern solutions that aren’t without flaws or limitations – both require physical access protection, analysis of ongoing threats to people working in the vicinity, as well as constant monitoring of the entire system to ensure it runs smoothly.
Roller conveyors are as safe as AMRs, but in the case of a belt conveyor you have to ensure transport safety along the entire route. A sufficiently large are of the warehouse has to be fenced off, which is often problematic, costly, makes it difficult to modify the warehouse at a later date and creates additional logistical problems. Keep this in mind when planning your operations.
Summary
There are fundamental differences between the design and the purpose of AGVs and AMRs. Traditional conveyor systems are inflexible. This means that the system works perfectly provided that all its individual components are also working flawlessly. If an AGV comes across an obstacle, it will stop, expecting a human to solve the problem. Thus, it slows down the entire transport process. An AMR is equipped with sensor and navigation systems that enable it to analyse the situation on an ongoing basis. If it comes across an obstacle, it will attempt to bypass it, in compliance with safety rules. Autonomous mobile robots are the future. The technology is constantly evolving, and many companies have already seen its potential and invested in modern warehouse automation processes. VersaBox is not only an AMR manufacturer, but also helps to provide smart solutions using the latest technologies that allow you to optimise operations and intralogistics processes in factories and warehouses. Join us and start creating the future of the intralogistics industry today.