What is an AMR Robot?
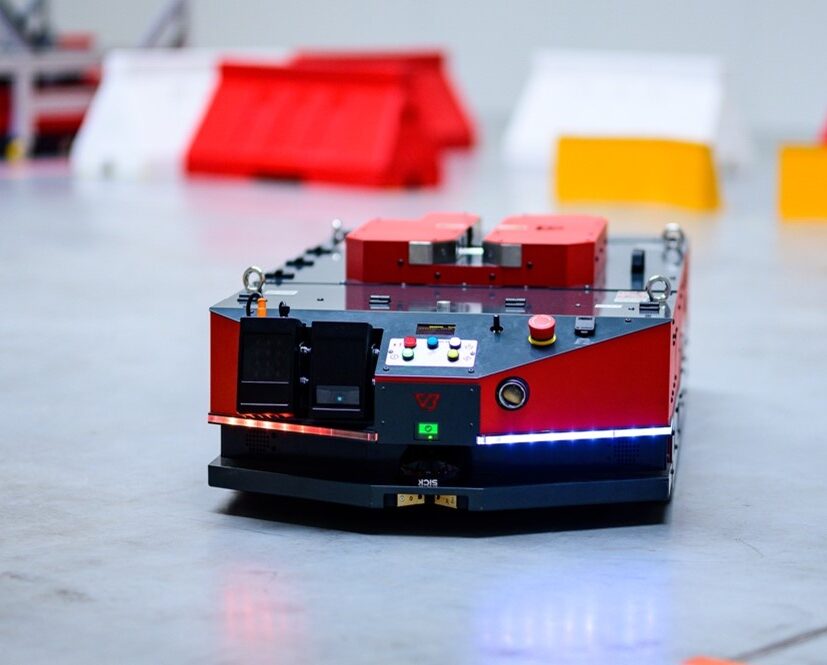
Robotics has come a very long way in the last few decades – it is no longer just large, stationary machines that not only were operated by specialised programmers, but also had to be separated from human workers/workstations. In this text, we will introduce you to their complete opposite – small and agile autonomous mobile robots. Collaborative robots of the AMR (Autonomous Mobile Robot) class.
A mobile robot – what is it actually?
Mobile robots are nothing more than machines that can change their position in space (e.g. by driving, flying or swimming) while performing pre-programmed tasks. So this category includes, i.e. self-driving trolleys, flying delivery drones and remotely operated underwater vehicles. A standard mobile robot does this within a predetermined path, and its range of movement is limited by power or control cables. AGV (Automated Guided Vehicles, not Autonomous Guided Vehicles as some call them) trolleys are a good example of standard type mobile robots. They can transport goods on their own or tow several trailers behind them (including further trolleys). These machines only travel on specially designated routes (often created by magnetic strips placed in the floor) and are unable to avoid obstacles that appear in their path. Once obstacles are detected, they will stop and wait until the passage is clear. Correcting the trajectory of their movement is a time-consuming and costly process. All types of AGVs require a specific control sequence and route to be programmed, and their path is monitored in real time using laser scanners usually located at the front of the unit. Autonomous robots are by far the most advanced solution, on which we will focus for the rest of this text.
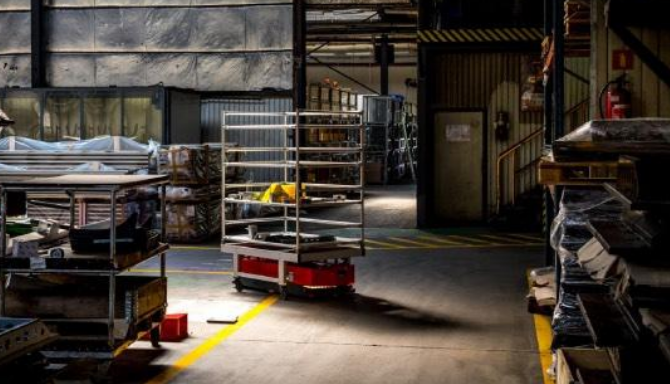
Autonomous mobile robots – what are they and how do they work?
Autonomous robots or AMRs (Autonomous Mobile Robots) are a modern type of mobile robots that can be navigated without any additional external infrastructure. AMRs do not require route planning – they will move efficiently and safely through a given space on their own. Thanks to a system of sensors (e.g. cameras, distance sensors, or other machine vision technology), they will avoid colliding with encountered people and obstacles, continuously selecting the most efficient route. Autonomous mobile robots in Industry 4.0 are also often referred to as:
- autonomous warehouse robots
- autonomous transport robots
The operator’s role here is limited only to a manually controlled tour of the site, thanks to which a map of the workspace is created. To be able to do this, all you have to do is run a dedicated mechanism on the robot and drive it precisely around, for example, the production hall. All you need to control it is a virtual joystick on your phone. During such a tour, the robot’s laser scanners will detect walls, equipment, machinery, and all other stationary elements of the interior. Once the entire workspace has been scanned, a map will be created, which the autonomous mobile robot will use to navigate through that space. Thanks to the advanced mapping technology, only a single tour is required.
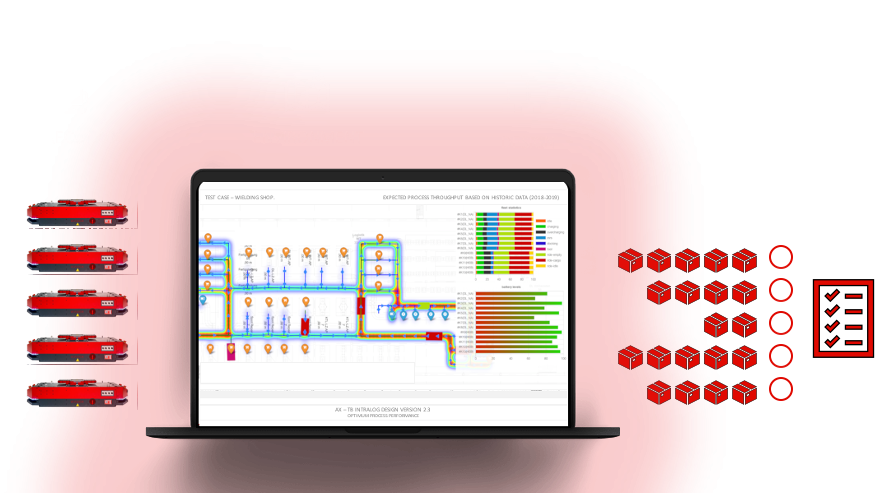
Such a map can be easily changed later on (e.g. after implementing new stationary machines) and further zones can be added to it (e.g. a speed limit on a particular section or an exclusion zone). It can also be used to introduce new objectives and dynamically change the guidelines for autonomous mobile robots. All this results in AMRs being ready to work in just a few hours after being delivered to the facility.
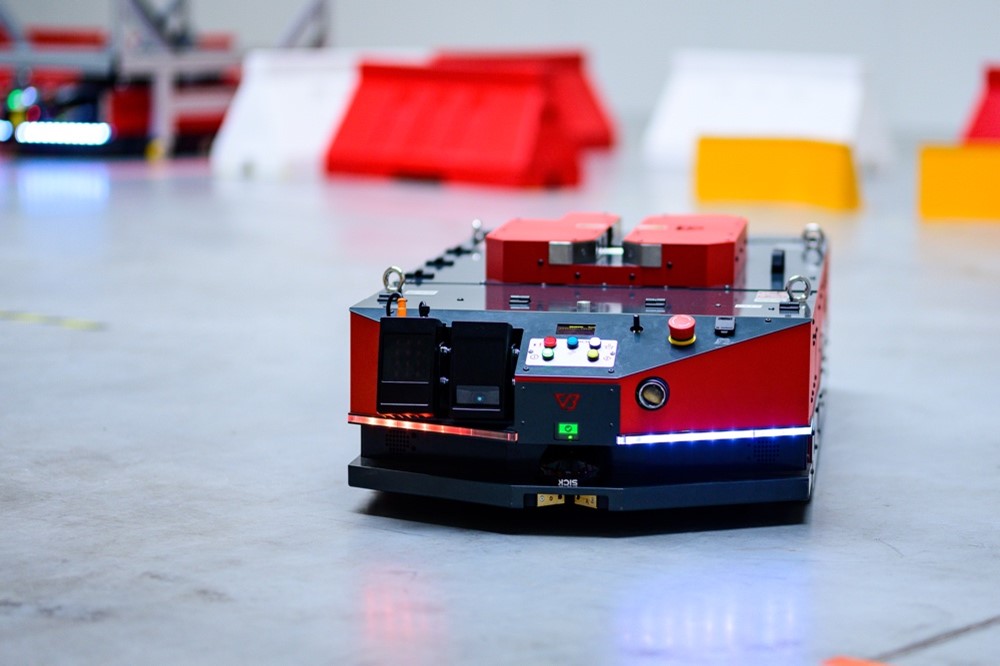
Applications for autonomous mobile robots
Autonomous mobile robots can be used on a large scale in virtually any industry – at least some production processes, especially those within intralogistics, can be automated. With the help of the right software, it is even possible to completely automate intralogistics in a factory. A wide variety of autonomous mobile robots are available on the market – both specialised robots, designed to perform a specific task, and more versatile ones that can be adapted to the changing needs of a company. It is to the latter group that our VERSABOTs belong – thanks to their modular design, they can be adapted on an ongoing basis to tasks within the production line, factory floor or warehouse. The mobile robots in question can be loaded automatically by industrial robotic arm, manually or automatically from a suitable docking station. What’s more, an autonomous robot can be adapted to transport the customer’s unusual cargo, thanks to passive or active attachments. Below are some of the most popular applications for these machines.
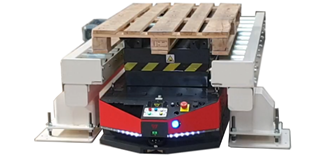
Pallet transport
One of the most common applications for AMR robots is the transport of pallets within warehouses and production halls. Autonomous mobile robot technology enables quick transport of pallets from point A to point B without worrying about path planning, special track or predefined route. All you need are a receiving/retrieval station which the mobile robot will be able to drive into, and appropriate equipment for the unit – in VERSABOTs’ case it would be the Lift module.
Once docked, the robot picks up the pallet and drives it to the location indicated on the map as the destination point. Of course, it lowers the pallet onto itself after leaving the station. The aforementioned laser scanners and cameras allow it to enter the station precisely and detect whether there are any products already at the drop-off point. If there are, it will wait until the station is free or go to another one (depending on the activated software components). Finally, it docks, leaves the pallet on the platform and goes to get another one.
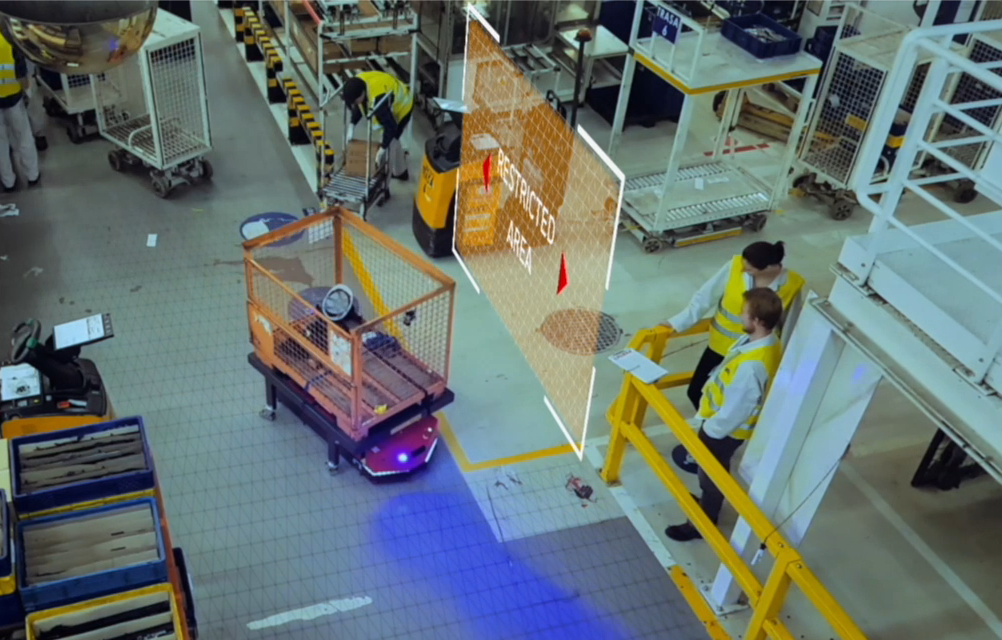
Trolley towing
VERSABOTs equipped with an automatic coupler module can be used to tow various types of mobile platforms and trolleys (e.g. pallet, cabana or gitterbox). Thanks to a standardized interface, we can tow different trolleys using the same unit. The VERSABOT (i.e. an autonomous mobile robot) drives underneath the trolley or mobile platform on which it is placed at the pick-up point (detected by cameras) and, after coupling, delivers the cargo to the specified location. Once there, it detaches the load and returns for another one.
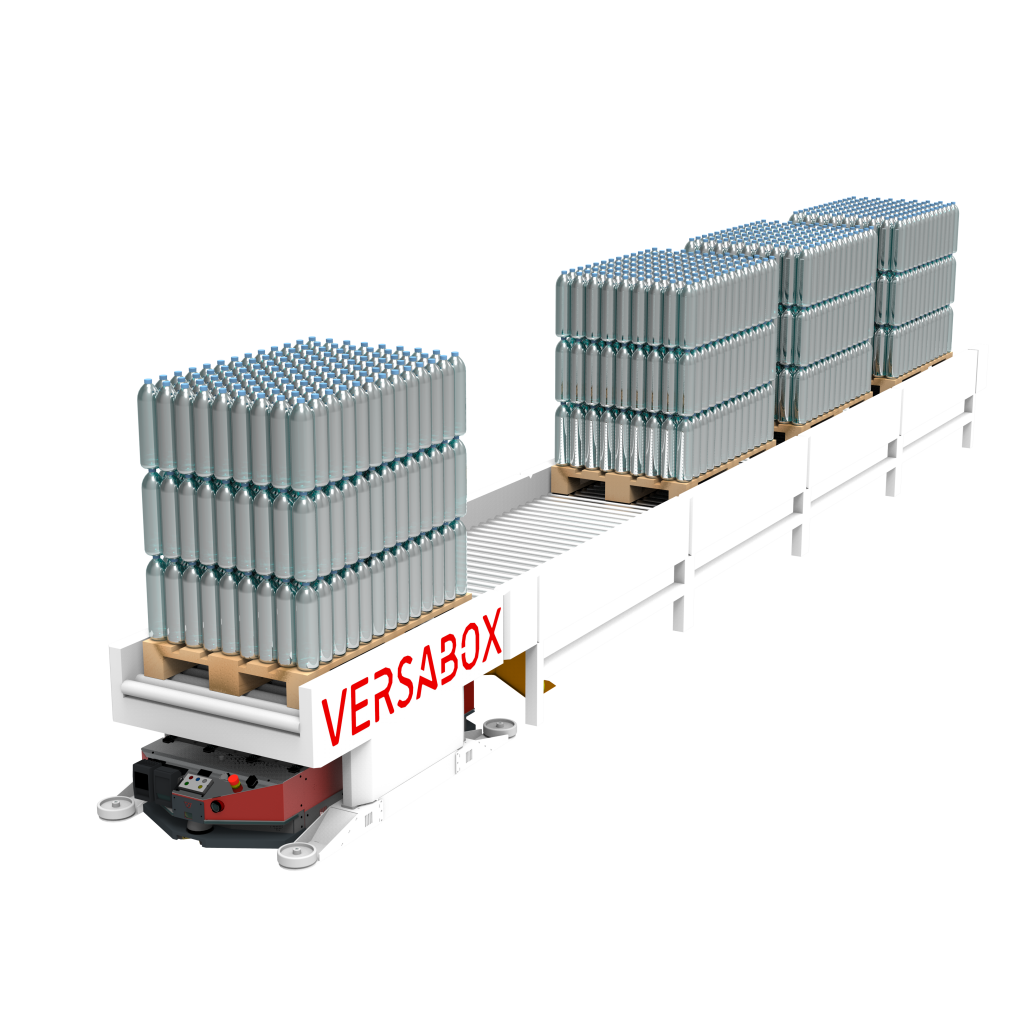
Support for roller conveyors
The permanent coupler module allows a VERSABOT to be connected to, among other things, a special trolley equipped with automated rollers. It is designed to carry heavy loads taken directly from the production line that uses roller conveyors and transfer them to similar conveyor belts in the warehouse. AMRs with this module can also tow other specialised trolleys, for example those for transporting hangers between production cells or for exchanging pallets between production lines.
Why should you adopt autonomous mobile robots?
Even a single autonomous mobile robot can bring significant benefits to your company. Here are some examples of what introducing autonomous mobile robot components can do for a factory:
- Intalogistics automation – mobile robotics ensures that the flow of resources and products is always smooth – everything is delivered on time and does not require constant supervision or human intervention.
- Possibility of constant operation of the facility – the only limitation of the automatic transport trolley is its battery capacity – it does not need breaks, sleep, or holidays. Thanks to process automation, factories can operate continuously virtually all year round. But back to the battery issue – most modern AMRs are equipped with a power source that allows for six to eight hours of continuous activity (i.e. roughly one work shift). Thanks to automatic charging stations, the robot will recharge itself when energy levels drop to a certain level or drive up for a quick charge during periods of downtime.
- Low costs – one of the most frequently repeated arguments against robots is their high cost. In reality, however, the purchase and the cost of implementing a robot in a facility is an expense that is comparable (and often even lower) to the cost of hiring an employee. Thanks to their high performance, most models pay for themselves in just a few months. We can significantly reduce or eliminate some costs altogether (e.g. production hall lighting – mobile robots can work unhindered in the dark).
- Higher safety – thanks to the technical solutions used, AMRs have a much higher level of safety than, for example, forklifts. They will not bump into any obstacles or racks in the warehouse, they will not exceed the weight of loads, nor will they hook on to passing people. An autonomous mobile robot (AMR) can even safely transport contagious laboratory specimens due to its advanced collision avoidance capabilities
Autonomous mobile robots (AMRs) – summary
Robotics technology, especially AMR, implementations open up a great deal of possibilities – just one robot allows a company, for example, to reduce the time it takes for products to reach the warehouse or to reach a production goal more efficiently. Mobile robots are undeniably the future of industry as a whole – they allow us to combine machine and human work in one area without fear of safety violations or serious injuries. Moreover, they can move around their environment independently, perform repetitive tasks easily, and use advanced technologies such as machine learning and artificial intelligence to plan an alternative route “on the fly” in case of an unexpected obstacle (autonomous navigation). Due to modular robot solutions, they can make use of various tools like mobile manipulators. Thanks to open, modular software development kits and cutting-edge computing solutions, they can be effortlessly fitted to the needs of a given company.