What is intralogistics?
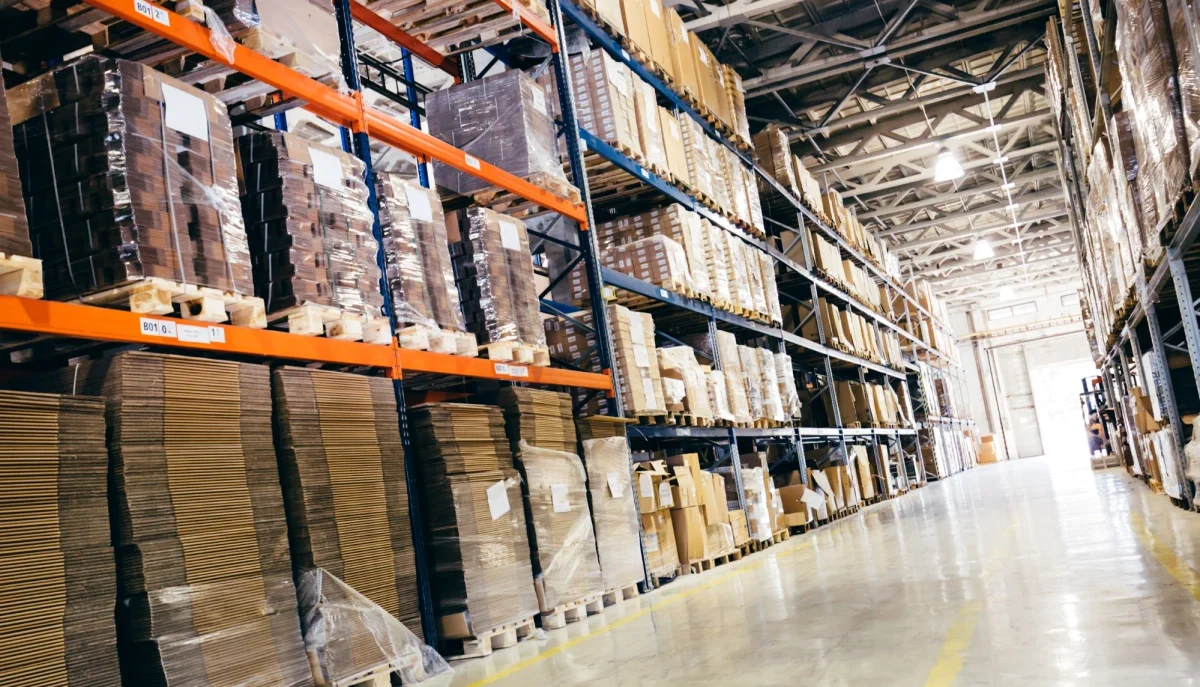
Although a relatively fresh term (it was first defined in 2004), intralogistics is one of the concepts encountered by many business owners even slightly associated with the flow of materials/products within a facility. Today, we will present a brief definition of intralogistics and its key elements, and take a bit closer look at the trends in its development.
Definition of intralogistics
Intralogistics or internal logistics is the branch of logistics that deals with the organization of the flow of information and materials within a given company. This term is therefore used to describe all the internal supply chain processes necessary for the smooth operation of the company, i.e. everything that happens from the arrival of raw materials to the release of the finished products.
What does intralogistics consist of?
Intralogistic processes can be divided into 3 distinct categories:
- Internal material flow – applies both to transport within a single site (e.g. a production hall) and to the flow of materials between different sites belonging to one company. For instance, on the production plant – warehouse route, between several warehouses or individual production plants in a single production chain.
- Management of information flow and inventories – every company should (and in fact must) ensure an efficient flow of information (e.g. every employee should be given easy access to the information necessary to perform their duties properly) as well as know exactly what its stock levels are and keep them up to date. In this way, it will always be clear where the available stock is located, how it is changing and when it needs replenishing. Special stock management software solutions make this task much easier – among other things, they make it possible to easily handle purchasing and invoicing processes and comprehensively track the flow of all goods in the supply chain.
- Management of warehouses – this applies to all logistical operations carried out in the warehouse, i.e. management of the location of products, preparation of orders, incoming goods and outgoing shipments, etc. The easiest way to optimize warehouse processes is to automate them – as an AMR/AGV robot manufacturer, we can equip you with all the tools you need to do this.
Intralogistics development trends
Thanks to the downright enormous advances in digitalization in recent years and the dynamic development of robotics/new technologies, companies can now optimize their logistics processes much more easily. This has allowed many new industry management concepts to develop – in the context of internal logistics processes, the most important of these is the so-called intralogistics 4.0. With its increasing prevalence, the following trends are developing:
Robotization of the warehouse space
With the introduction of AGVs (Automated Guided Vehicles) and autonomous mobile robots (AMRs for short) into warehouses, it is possible to automate the manipulation of loads, the flow of goods to dispatch zones and other repetitive warehouse activities that needlessly burden people (especially in pallet and heavy-duty warehouses). What’s more, both the overall production and logistical costs of running a warehouse can be significantly reduced.
Read here to find out how the implementation of our AMR robots takes place.
With the help of mobile robots, the need for forklifts can also be significantly reduced or even eliminated – work safety will certainly benefit from this. Besides, by basing the warehouse on the AMR robots, it is possible to monitor all the activities they perform in real time and dynamically adjust their guidelines if necessary.
It also saves a lot of time, especially for companies with fluctuating intensity of cargo flows or varying production volumes. Through automation, a smooth flow of resources and finished products can be ensured, thereby eliminating downtime and empty runs. It is not only large enterprises that can benefit from the implementation of robots, but also medium and small companies with their own warehouse or distribution center.
IT warehouse management systems
A WMS (standing for Warehouse Management Software/System) is another tool for streamlining the logistical processes taking place in warehouses. It allows the continuous traceability of goods (i.e. the ability to trace the history/location of a product from the moment it comes off the production line/enters the warehouse records to the end of the supply chain, i.e. reaching the customer). Thus you can better organize the tasks of receiving goods, complimenting and preparing orders and shipping (overall flow of goods/intralogistics solutions).
To fully utilize the capabilities of WMS platforms in planning and supervising intralogistics processes, it is necessary to implement a system of connected devices (based on the IoT technology – Internet of Things). This will enable the collection and transfer of information from the physical to the digital environment (which can be expanded to create a digital twin of the entire factory) and completely remote management of all connected devices. This is because the IoT system allows direct communication between the management and control software.
Implementing such a system saves staff time – collecting the data needed for order picking in an analogue manner would take incomparably longer. Its introduction will therefore allow for a much better allocation of human resources.
Synchronization of production and storage processes
In order for intralogistics 4.0 to become a reality in your company, close collaboration between the various activities affecting intralogistics management is essential. This is one of the basic principles of so-called lean management. The synchronization of production and storage processes plays a key role here.
One of the simplest ways to achieve it is to retrofit a WMS with a manufacturing module or use an AMR robot fleet management platform. They will greatly simplify the design process of the company’s material handling lines and allow full use of the AMR robots’ capabilities (and their functionality). Implementing it will give your business far more flexibility than any other currently available service.
Automation of the in-house material flow
Automation is worth taking out of the warehousing sites and at least partly enriching production processes with it. This will not only speed up all internal transport, but also make it much easier to plan and supervise. You don’t have to start at a high degree of automation – with the right technology, even a single autonomous machine can improve a lot, especially in e-commerce-oriented companies.
The introduction of mobile robots/autonomous machines is particularly recommended in hazardous areas – their navigation system allows them to easily avoid obstacles, and areas they should not enter can be easily marked in their guidelines. Thanks to their advanced sensor technology, they can provide continuous logistical flow even in the most busy facilities. Plus, you can add specific requirements to their programming.
Take internal logistics to the higher level with us
There’s no denying that optimization of logistics is crucial in future-proofing your company. The implementation of automation into production facilities has numerous benefits that are not to be ignored. In the digital age, it is robotics and autonomous systems that have the greatest potential for internal material handling. They are great both as an addition to automatic conveyor systems and a replacement for conveyor technology in production lines. With the right tools, even the most complex processes will run smoothly with minimal supervision. With solutions from VersaBox (such as AMRs, digital twin software, WMS etc.), you can not only improve the efficiency of product storage and packaging, but also fully automate the production and shipping of goods. Our robots and software will help your business become part of Industry 4.0, step confidently into the new era of the manufacturing industry and open brand new business opportunities.