From mushrooms, through laser scanners, to TRUE AUTONOMY. Robotics safety on the example of AMR
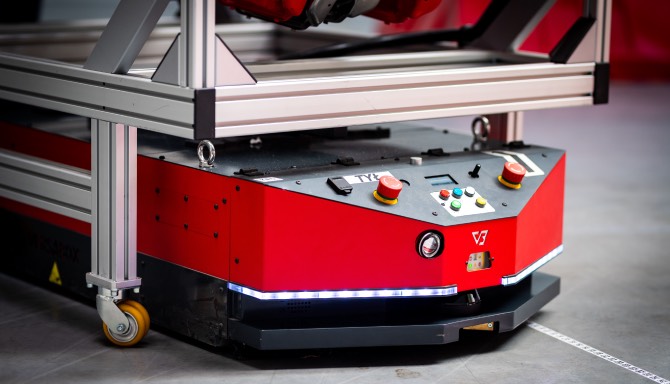
People are becoming less and less afraid of Autonomous Mobile Robots (AMRs), and are far more willing to believe that these machines are designed with human safety in mind and do not pose any serious risks. Another extremely important issue is the safety of the loads that are transported by the autonomous trolleys. The key to excellent results in both areas is the use of a technologically advanced robot and the creation of a system that allows efficient management of automatic transport.
The main challenge for AMRs is to fit into an incredibly dynamic, complex, and ever-changing environment of production facilities and warehouses. The constant movement of people, forklifts, overhead cranes, and logistic trains create a very dense network of mutual interactions – the AMR must fit smoothly and unobtrusively into it. The machine’s design and safety systems should enable it to efficiently perform assigned tasks, without posing a threat to people, other vehicles, plant equipment and transported loads. However, the most efficient, ergonomic and universal stroller is just half the battle – the other is the system that enables the planning and the execution of intralogistics tasks.
What makes the AMR safe?
We have learned to trust robots, even though we do not always know why they are safe. Meanwhile, robots are machines whose safety systems are developed based on detailed regulations and standards agreed upon by international experts. The latest set of guidelines will be included in the ISO 3691-4:2020 “Industrial trucks — Safety requirements and verification — Part 4: Driverless industrial trucks and their systems”, which is set to be published in August 2020.
AUTONOMY@WORK – The safety systems of AMRs such as VERSABOT 500 and VERSABOT 1000 can be divided into several categories:
- Active safety systems – that is, all safety measures which activate in response to changes in the work environment: motion sensors, cameras, bumpers, emergency stop mushroom push-button, laser scanners (which provide terrain mapping and spatial positioning), and machine vision, which enables the robot to control the changes in its surroundings.
- Passive safety systems – all robots have different colours and are marked appropriately, emit light and sound warning signals, can emit emergency signals – all this to make sure that the appearance of a robot will be noticed by people performing manual labour or operating machines such as forklifts.
- Fail-safe mode – that is, in the event of a robot sustaining damage, it goes into ‘safe mode’ – for example, if during a delivery the laser scanner or the machine vision systems malfunction, the robot automatically halts because stopping is a much safer option that continuing the task without an efficient navigation system and the ability to detect obstacles.
These systems and mechanisms protect the environment in which the robot works. The design of the AMR itself, however, is the factor that ensures the safety of the goods being transported. VersaBox is a manufacturer of AMRs that have a modular design, which means that a universal transport platform can be equipped with different types of attachments: a lift, a wheeled trolley, a frame hanger, or a roller system for load collection from a roller conveyor. They ensure stability and safe transport of virtually any loads – based on these solutions, robots can be highly personalised and perfectly adapted to specific customer requirements. The design and adaptation of load collection and delivery infrastructure also heavily impact the safety of the robot’s performance. Simple yet precise loading and unloading solutions ensure the risk of damage to goods in transport is minimised.
In order to fully exploit the robot’s potential, it is necessary to create suitable software – a system that will allow to design processes, control their execution, and implement them efficiently.
Autonomy@Work, or the power of software
The true value of the solutions offered by VersaBox is not only due to their innovative nature, but also their comprehensiveness. Along with VERSABOT robots, customers receive the AUTONOMY@WORK intralogistics platform. Thanks to this software, it is possible to fully integrate the robot fleet with the production environment in three key aspects:
- Hardware integration – the aforementioned modular design of VERSABOTS allows for a quick and flexible adaptation to all types of transport tasks.
- Software integration – the AUTONOMY@WORK platform offers a universal API and thus allows for a seamless integration with an already installed MES software.
- Human integration – various types of mobile terminals provide convenient integration of robot work with processes carried out by humans.
AUTONOMY@WORK enables easy and flexible design of logistics processes, monitoring of their execution, exchange of information between robots that make up the fleet, and connecting with the already existing workplace infrastructure. AUTONOMY@WORK possesses the tools that allow you to ‘teach’ the robots appropriate behaviours that are dependent on the area of the facility they are located currently in. Different manoeuvring procedures are used at aisle junctions, at intersections with pedestrians, and during manoeuvres in narrow aisles. VersaBox robots can not only identify obstacles but categorise them in order to implement the best strategy to avoid them. The robots react differently to the sudden appearance of a human and to an oncoming logistic train. Thanks to the intelligent and truly autonomous behaviours described above, it is possible to simultaneously increase the safety and the efficiency of logistics tasks.
Summary
AUTONOMY@WORK allows for optimal design of intralogistics processes, flexible and dynamic robot fleet management, and its seamless integration into the existing infrastructure or processes already operating at the production facility. The true ‘intelligence’ of the system solutions offered by VersaBox is that they are not in opposition to the manufacturing processes already in place but support them – by using the potential provided by robots they offer real business value.