Can my factory be automated?
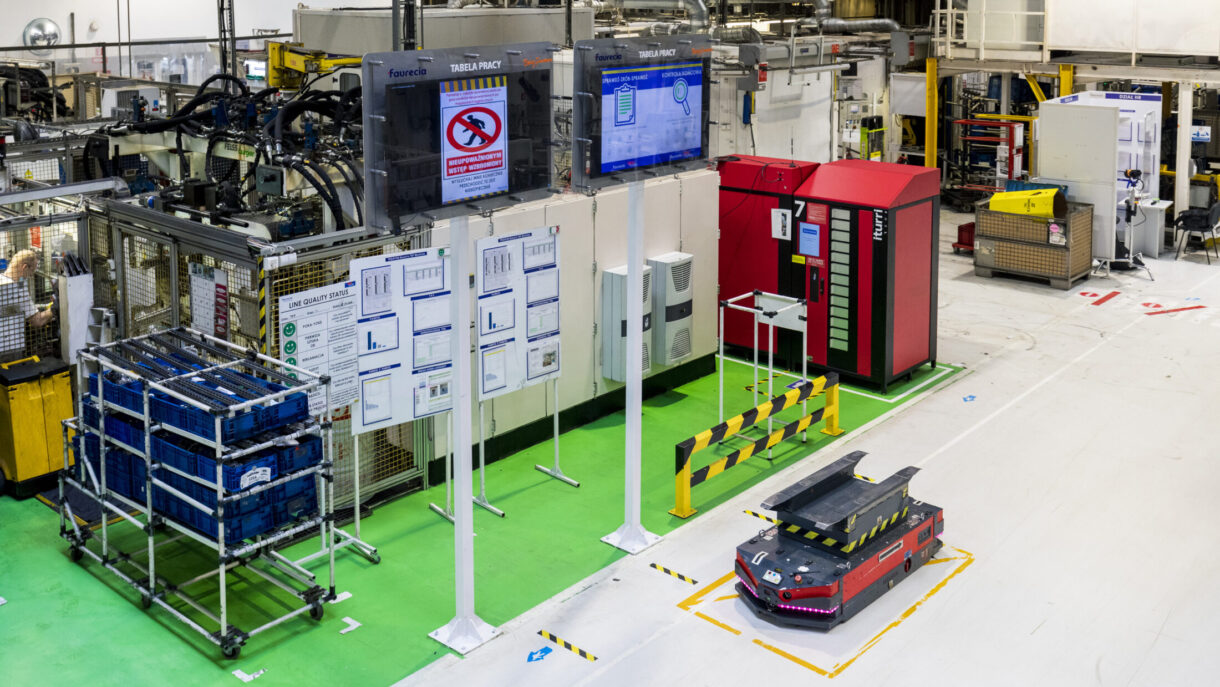
The automation of industrial processes, and in particular the automation of intralogistics, is one of global economy’s hot topics. Everyone knows that processes need to be automated – but not everyone knows how to start. If you are asking yourself whether your plant can be automated, you will find the answer to your question below. We debunk common myths about the automation of intralogistics, and we show the potential of optimising internal transport with the use of Autonomous Mobile Robots (AMRs). If you are asking about the possibility of automation, you are most likely interested in not just the technical aspect, but primarily in the cost of such an operation. It is obvious that with an appropriately large investment, robots can be implemented into any production hall, warehouse, sorting plant or transhipment terminal. However, in the case of automated production or transport lines, their use involves a serious interference into the structures of existing facilities. If you choose AMRs, this will not need to happen.
Autonomous robots in every plant
The first generation of self-driving Automated Guided Vehicles (AGVs) required landmarks and reference points to find their way around a factory floor. Guides along the surface of the floor, usually in the form of an adhesive tape, or expensive inductive guidance systems embedded into the floor were necessary. The self-driving AMRs currently dominating the market, such as Versabot 500 and Versabot 1000, are fully independent. The only thing they need to efficiently perform their assigned tasks is a level, hard floor. They will take care of the rest themselves. When preparing an implementation, the location of charging stations and parking spaces for the robots should be carefully planned.
How is a virtual map made?
The robot scans its surroundings and creates a virtual map during its first run. The map will be its reference point. It contains static elements, while the obstacles will be detected by the robot as it moves through the environment. The robot independently decides how to overcome these obstacles. A storage rack is a static and permanent element, while an abandoned pallet obstructing the path is a temporary hurdle. Robots can easily identify them and take appropriate action. Conclusion: there is no need to adapt the facility to the AMR. It is the robot that adapts to function in an already existing work environment. What is more, the AMR reacts dynamically to all changes. It constantly keeps its virtual map up to date and never loses its bearings. The fear of needing expensive adjustments to the infrastructure of an existing facility is the most important myth connected to the automation of internal logistics – but it is not the only one.
Warehouse and production hall automation: 5 myths blocking development
We have compiled five of the most popular, stereotypical, misleading, or downright false beliefs about the automation and robotisation of industrial processes. We were primarily interested in the automation of logistics processes in warehouses and production facilities that utilise self-driven trucks and trolleys. However, it would not be a big mistake to extend the list below to other types of industrial robots.
Myth #1: Robots are expensive, it is cheaper to hire people
How is it really? Are robots really a more expensive solution? You do not have believe any promises – you just have to count the full annual costs of employing one warehouse worker, wages included. Then, compared that with the cost of implementing one AMR and you will see what the truth is. A robot can work much more efficiently than a human when it comes to many logistics tasks. Furthermore, a self-driving truck can easily withstand continuous operation, for three shifts. This means that when comparing the costs of human labour they should be multiplied by three.
Myth #2: It is difficult to ensure safe working condition for both robots and humans
The subject of the safe use of AMRs in warehouses and production facilities was discussed in detail in the article “Don’t fear the robot“. Here, we will limit ourselves to just state that AMRs are much safer than forklifts or conveyor belt transport.
Myth #3: Our manufacturing process excludes the use of robots
There is no manufacturing or logistics process that cannot be at least partially automated. The best results can be achieved by automating tasks that are associated with performing repetitive, monotonous motions, and the need to maintain high precision and attention to detail.
Myth #4: There is not enough space for robots to operate
AMRs can easily cope with avoiding obstacles, but also manoeuvring in narrow alleys where doing the same using forklifts is a big problem. AMRs can work in any space big enough to fit the load it is transporting.
Myth #5: Robots are difficult to program
Some industrial robots, including large machines responsible for precise assembly, require the work of a programmer. AMRs are much easier to program. A set of commands such as “drive to point A”, “wait 20 seconds”, “if … then … ” is used to define their assignments. Assigning tasks requires logistical knowledge and knowledge of ongoing manufacturing processes rather than programming skills. Conclusion This is not an exhaustive list, but these are definitely the most popular myths about robots and automation. It is worth debunking them because they effectively hinder the development of many companies. Knowing the real facts, we can easily see that basing intralogistics on autonomous robots is an easy way to optimise internal transport and gain a competitive advantage. This is how it is today. And soon it might be a necessary requirement to keep up with the competition.