AMRs operate as a team, or how simulation supports intralogistics processes
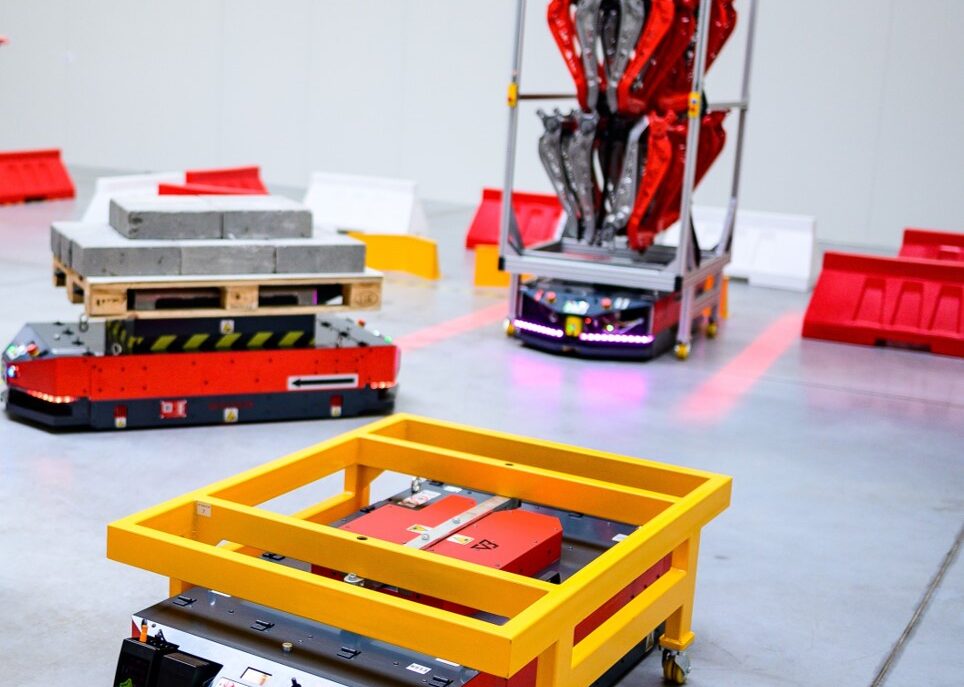
AMRs in manufacturing plants, acting like a good tema or swarm of busy insects, sounds like something out of a science fiction movie. Machines exchange information with each other, negotiate the right of way, and designate detours based on current data analysis.
Making completely autonomous decisions is within the scope of AMR capabilities. And it can be very useful. However, most warehouses and storage spaces are not so complicated that such an advanced independence is necessary. “Ready-made” solutions have greater practical value.
If route A is blocked, select route B
An AMR can make autonomous decisions based on an ongoing data analysis – data that it exchanges with other robots. But it can also choose from predefined routes – if route A is blocked, it selects route B and makes its way to the destination. And if route B is also impassable, does it then select route C? It could do that, but most often there’s no such possibility or need.
In reality, point-to-point transport can happen via any route, or one or two pre-selected ones. When the main route is blocked, the robot always re-analyses the data coming from the other robots and plans an alternative route based on it.
Choosing the optimal route is choosing the shortest travel time, not the shortest distance travelled. This is because that in given working conditions it may turn out that the longer route can be covered faster. It may take longer to drive the shorter route, because it’s more congested and requires moving at a much slower speed.
If robots are a team, the system is their boss
If a robot cannot collect data and decide on its own, e.g. how to avoid an obstacle, it communicates with the system, which decides what action to take. For example, when driving up to an obstacle, which requires potentially driving into oncoming traffic, the robot receives information from the system whether there’s another robot (vehicle) coming from the other direction or not. Instead of collecting data from other robots and negotiating the right of way, it immediately acts – drives around the obstacle or gives way.
“We initially used a many-to-many communication model. The robots shared data with each other without the mediation or supervision of a decision-making centre,” says Paweł Oziębło, Business Development Manager at VersaBox. “However, for larger fleets, a star topology ensures a much greater predictability and efficiency of robots – all robots communicate with a central system that then distributes information to individual machines. It doesn’t mean, however, that the entire system stops when connectivity is lost. On the contrary, the robots continue performing their tasks. Versabots are autonomous machines not only in name.”
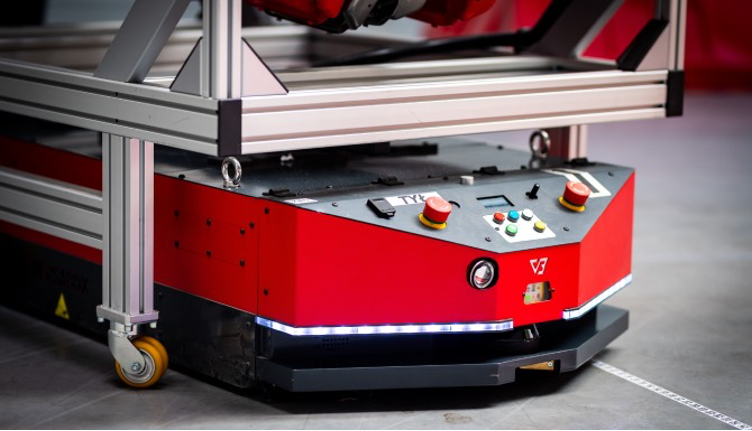
The basic rule of setting up a task queue is the “first come, first served” principle. It determines the right of way at intersections, the order at payload collection and delivery points, and a robot’s place in the queue to the charging station. You can also define priorities by setting which of the robots, depending on their current status always (e.g. with or without goods) have priority.
Get rid of queues before they even begin
Using the tools developed by VersaBox allows you to avoid unnecessary queues and congestion. This is because the intralogistics system is first created as a virtual model. All solutions are tested on such a prototype before physical implementation begins. It’s possible to check many variants and alternatives. Using the simulation, it’s possible not only to design and test, but also to optimise the internal transport system before introducing the robots into a manufacturing plant or warehouse.
All of the things mentioned above can be achieved using the VersaBox Virtual Factory tool. It enables the modelling of intralogistics processes, their testing, and managing any changes. It’s incredibly important that all operations can be performed by the endpoint customer’s staff. Using the system doesn’t require any specialised training or programming skills.
Thanks to the use of the VersaBox Virtual Factory and the virtual model, you can simulate and work out basically any situation that could happen in real life. Referring to analogies from the world of human work, the VERSABOT fleet is a team of autonomous, digital collaborators, managed by a central system. The units perform their tasks autonomously, while the central system ensures a collision-free operation of all intralogistics processes. Thanks to this, managing a fleet becomes fully predictable.