ABM GREIFFENBERGER
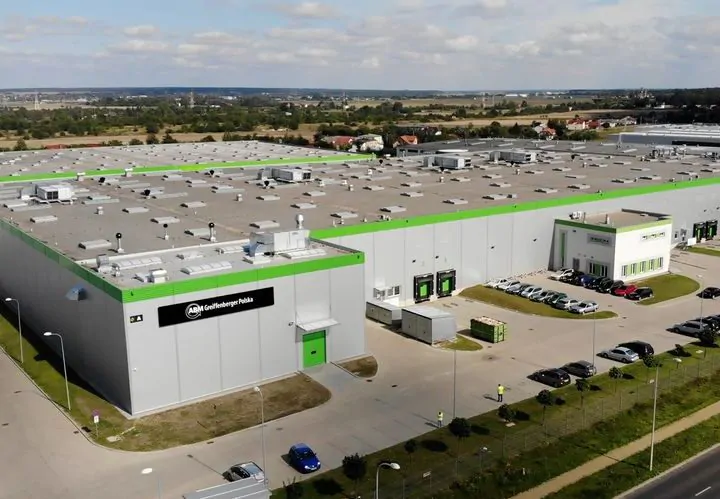
ABM Greiffenberger Antriebstechnik is the world’s leading supplier of advanced drive solutions for machinery, plant and mobile equipment. Founded in 1927 and headquartered in Marktredwitz, Bavaria, the company is part of the Senata Group since October 2016.
The company specializes in the development and production of high-quality electric motors and gearboxes for various industries. It offers drive solutions consisting of motors, gearboxes, brakes and frequency converters tailored to individual requirements. ABM pursues a zero-error strategy through continuous process improvement, using stress testing, a consistent CAQ system, laser measurements and state-of-the-art testing technologies.
Investment goals
Eliminating the need to handle transport activities by manufacturing line operators
Autonomous devices have to be cooperate seamlessly with AGVs
Challenges
In the context of the zero-error strategy, the area of quality control is an important part of the production process for drive solutions at ABM Greiffenberger. The intralogistics system must deliver assembled motors and gearboxes from the assembly stations to the appropriate inspection and testing stations, from where they must be transported to the warehouse or workshop.
The automation of the transport of finished components between stages of the production process must ensure the uninterrupted work of operators, and eliminate tasks that distract them from performing key tasks for the production process.
An important challenge is to ensure the smooth and precise cooperation of mobile robots with the previously deployed AGV equipment designed and manufactured by ABM.
The autonomous transport system using the VB500, sensors and visual signaling allows operators to fully focus on manufacturing and quality tasks.
VB500 equipped with an automatic connector cooperates with the existing AGV system by transferring and collecting the load on a transport trolley adapted to the connector.
Up to 1,400 missions per month
Nearly 100 km per month
VERSABOX showed flexibility by offering a device rental model, which allowed us to verify the solution on the shop floor before making the investment. Today, when we see the benefits of implementing the solutions offered by the company, we decided to purchase the solution ourselves. An important element here was the flexibility of the solution itself, which efficiently cooperates with AGV devices of our own production in our processes.
PAWEŁ SAWICKI
Manager of Support & Development Dept.