LUBELLA
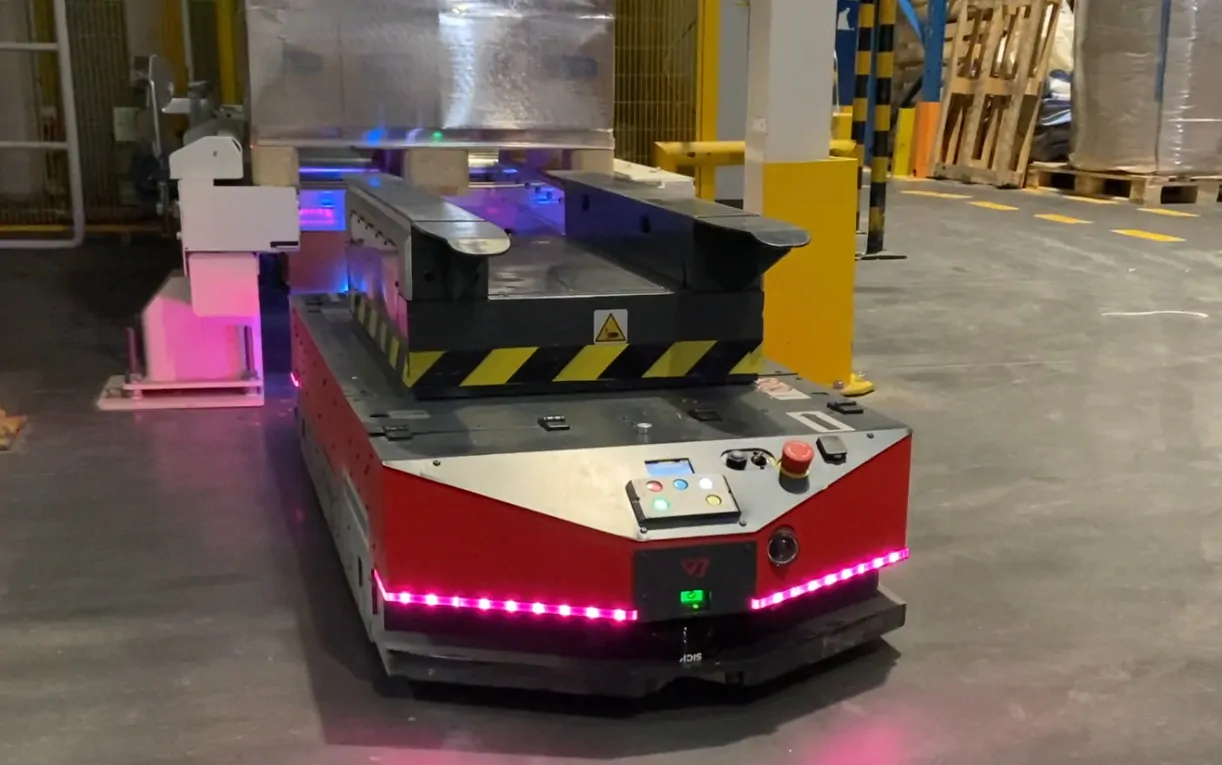
Lubella factory
Since 2003, Lubella has been operating as part of the Maspex Wadowice Group, one of the largest companies on the food market in Poland. Continuing the tradition of its great founders, it is constantly developing by implementing modern technologies and expanding its production facilities. The company has built a modern production and warehouse complex with the largest and most modern pasta production line in Poland. The investment not only increased the production capacity, but also, thanks to modern technology, made it possible to produce pasta of the highest quality.
Goals
The system should ensure efficiency ensuring uninterrupted service of the final stage of the production process (flow of products from the line to the warehouse).
Limiting the impact of the movement of devices and people on the implementation of transport tasks
Challenges
The MASPEX Group is aware that innovation in a well-selected area of the production process can have a noticeable impact on the entire value chain. Therefore, a good tactic for introducing innovation is to focus on specific improvement goals, in areas where it is easy to assess the results achieved. Such opportunities can be found even in such modern facilities as the Lubella pasta factory.
A modern production line at the LUBELLA plant uses roller conveyors as the basis for internal transport. But the process of receiving goods from 3 lines and transferring them to the warehouse intersects with a busy communication route, making conveyors impractical.
A route with heavy traffic impacts the smoothness and predictability of product pick-up, and at the same time creates the risk of accidents in the event of an accumulation of human-operated transport devices in this place.
Communication with the PLC system ensures adequate efficiency of the solution by synchronizing the receipt of products from the line by VERSABOT with the production cycle.
Thanks to the autonomy of the VERSABOTs, disruptions between the automated transport process and the movement in the factory were avoided, while the system delivers 24×7 availability. At the same time, robot safety mechanisms completely eliminate threats to people and other devices.
Up to 290 Missions per Day
Up to 145 Tonnes Per Day
Innovations are not a synonym of purely technical progress. In retail and manufacturing, process, logistic and cost innovations are also very important. The distribution chain does not have to be long or complex. Improving just one of its links can bring about huge changes in the efficiency of the entire process on the producer-retailer line, especially if the innovation concerns the area of logistics. (from an interview for the website www.wiadomoscihandlowe.pl)
KRZYSZTOF PAWIŃSKI
CEO, Grupa MASPEX
VERSABOX provided us with more than “just“ an efficient and reliable solution. The workshop for the management of MASPEX plants was also of great value, explaining the unique capabilities of autonomous robots and transport systems in an accessible and inspiring way. Knowledge transfer is an important component of the successful implementation of innovation.
PIOTR ROMAŃCZUK
Head of Factory Logistic