SMOOTH & EFFICIENT – FAURECIA STORY
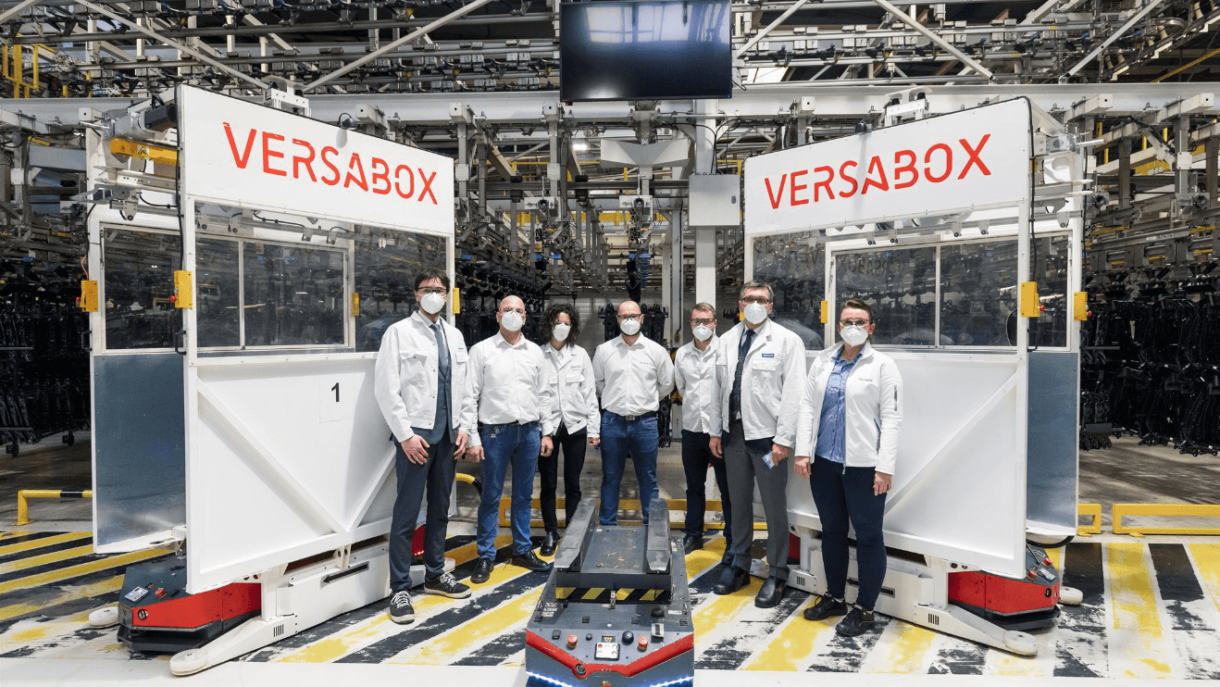
Faurecia Frames in Wałbrzych was looking for a way to improve the smoothness and efficiency of internal transport. That goal was to move from traditional material handling to intralogistics 4.0 based on Autonomous Mobile Robots (AMRs).
Faurecia decided to cooperate with VersaBox, the manufacturer of VERSABOT autonomous transport robots. The cooperation ended with success and satisfaction on both sides.
About Customer: Faurecia Frames in Wałbrzych
Faurecia Frames in Wałbrzych is a factory that belongs to the French company, one of the world’s largest automotive suppliers. Faurecia owns branches in 35 countries and employs over 100,000 people in 266 plants and 39 research and development centres. The factory in Wałbrzych has been operating for 20 years and specialises in manufacturing front car seats, which is supplies for brands such as Volkswagen, BMW, Ford, and Peugeot.
Initial conditions: organisational maturity and innovation orientation
Innovative thinking is part of Faurecia Frames’ strategy. The managerial staff sees robotisation and digitisation as an opportunity to constantly improve the efficiency of manufacturing processes.
Marcin Wójcik, Plant Manager at Faurecia Frames in Wałbrzych: “Our project consists of three main pillars: robotisation, automation of management processes, and automation of intralogistics. Processes in our factory cover all stages of the manufacturing of car seats: welding, painting, and assembly. The thing that binds the whole system is intralogistics, which ensures an uninterrupted flow of components between the warehouse and the manufacturing cells. Therefore, it became obvious to us that internal transport will become one of the first areas to be included in the robotisation of manufacturing.”
Three challenges
The manufacturing process at Faurecia Frames is characterised by a wide variety of products. Technically diverse car seats designed for multiple car brands are simultaneously manufactured on many assembly lines. Based on this, Faurecia Frames has set 3 main challenges to be met.
Challenge 1: increasing efficiency and smooth delivery
In the case of simultaneous production of diverse components, the challenge is to ensure a smooth and steady flow of all subassemblies to multiple locations. The flexibility and speed of reacting to an ever-changing environment, and the skills needed to operate the equipment, were the most important issues. The decision to delegate transport tasks to robots required a multiple factor analysis.
Anna Soćko, Head of Lean Manufacturing and Digital Transformation at Faurecia Frames: “We have set the bar quite high by entrusting robots with the transport of frames from the welding shop to the paint shop. We needed machines with a very developed navigation system, able to cooperate with other traffic participants in the plant, as well as maintain a very high manoeuvring precision. The choice of the VersaBox solution was determined by the perfect navigational capabilities of VERSABOT robots.”
“Thanks to the AUTONOMY@WORK intralogistics platform, the entire internal transport system can be designed from scratch. The implementation of all the above-mentioned functionalities does not require an investment in the IT infrastructure: our software can be easily integrated with the systems already in place in industrial plants and warehouses,” says Mateusz Wiśniowski, Head of Customer Success at VersaBox.
Challenge 2: ensuring manufacturing continuity
The managers at Faurecia Frames saw the robotisation of intralogistics as an opportunity to reduce the workload of their employees. The objectives were specific: to make factory employment more attractive, and to exploit the synergy of human and robot labour. AMRs took over the most strenuous, physically demanding and dangerous tasks. This allows people to focus on the coordination of processes and supervisory functions. As a result, work safety has been improved, while also increasing the efficiency and quality of the performed tasks.
Even after the first tests, VERSABOTs demonstrated excellent navigation and the ability to react quickly to changes in the environment. They proved their capabilities in the extremely demanding environment of a production hall.
Challenge 3: building employee trust and support for smart intralogistics
Every implementation, every innovation has a chance of success if it is positively received. Gaining the trust of Faurecia Frames employees accelerated the implementation process and ensured its success.
Bartłomiej Magiera, Production Manager at Faurecia Frames in Wałbrzych: “It quickly turned out that VERSABOTs behave like a well-coordinated team of digital employees. Intelligent machines controlled by an automatic fleet management system are on-time, reliable, and completely predictable. The problem of absenteeism and unplanned downtime has disappeared. It is currently difficult to imagine the implementation of manufacturing processes without the help of VERSABOTS.”
Success through cooperation
The cooperation between Faurecia Frames and VersaBox began with the deployment of a single robot.
Tomasz Biel, Plant PC&L Improvement Coordinator at Faurecia Frames: “We were aware of the outstanding navigation capabilities of VERSABOTs and the fleet management system. In practice, achieving the appropriate precision and accuracy of the entire system was a big challenge. Communication with VersaBox played an important role here. We gained a partner who not only offers a reliable product, but who understands industrial manufacturing needs and quickly responds to every inquiry from our side.”
Currently, VERSABOTs deliver components to 30 different locations. They make about 200 trips a day, which is about 70 tons of goods in total.
The initial goals set by Faurecia Frames managers have been achieved:
- significant increase of internal transport efficiency
- automation of frame transport while preserving existing trolleys with hangers
- reduction of errors in the delivery of components to assembly lines
- maintaining the continuity of a multi-shift transport process.