AI in industry
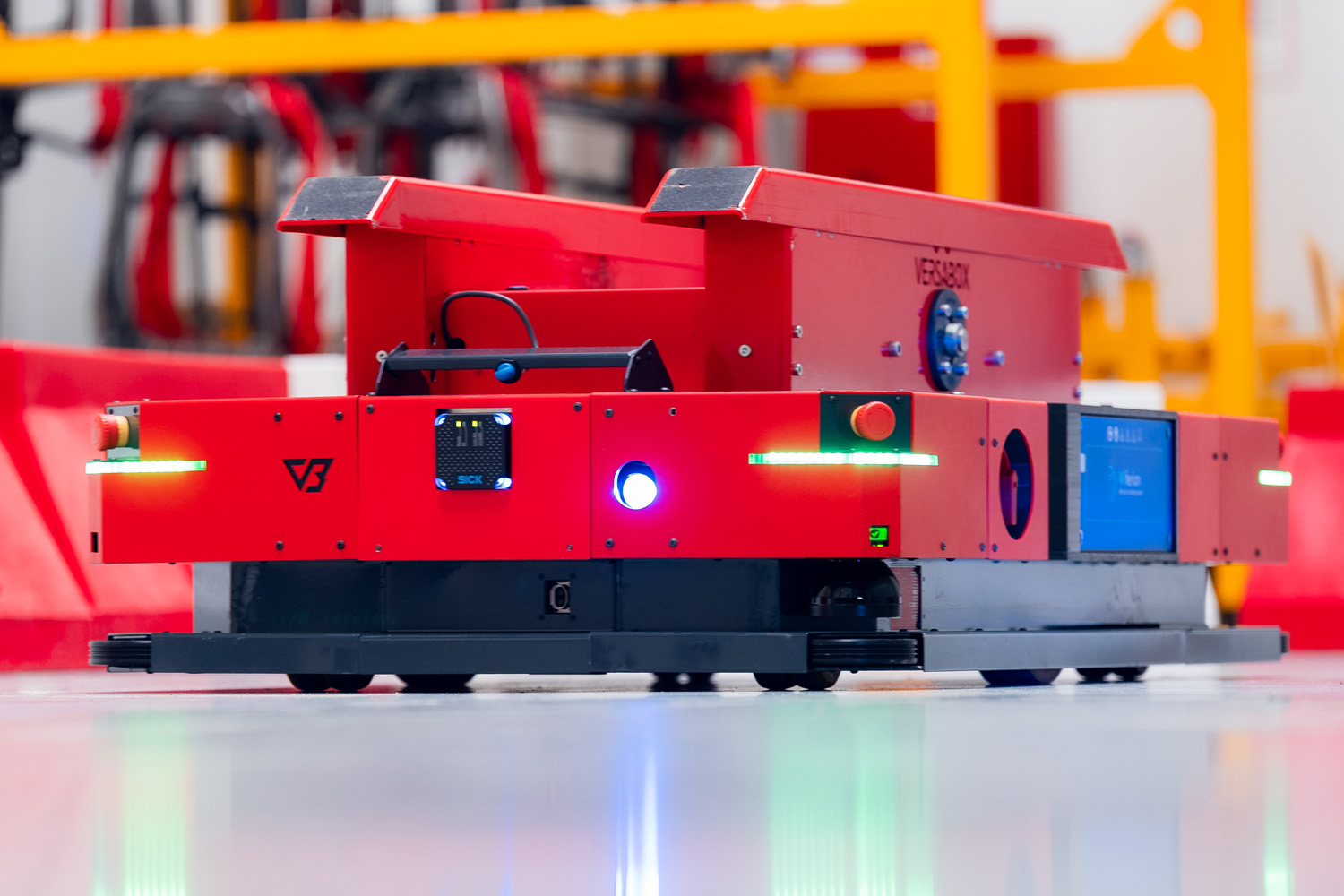
The “smart factory” concept originated from the 4th industrial revolution, also known as Industry 4.0. It emphasizes the integration of advanced technologies such as artificial intelligence, IoT, and automation in manufacturing processes.
Inspired by the sea change which has redefined the ecosystems in digital media, financial services or telecommunication, many experts have envisioned how the rising volatility, uncertainty, complexity, and ambiguity (often called “VUCA”) will affect the world of global production and logistics, and how technology will be used to radically reshape them.
VUCA affects global manufacturing and logistics in several ways:
- Supply chain volatility: VUCA can lead to unpredictable shifts in demand and supply, creating challenges for manufacturers in terms of raw material procurement and production planning.
- Uncertainty in transportation: Changes in regulations, geopolitical tensions, and natural disasters can create uncertainty in the logistics of transporting goods globally.
- Complex cross-border trade: The increasing complexity of cross-border trade, with its numerous regulations, customs procedures, and documentation requirements, can make global logistics more challenging.
- Ambiguous market trends: VUCA can result in rapidly changing customer preferences and market trends, making it difficult for manufacturers and logistics providers to anticipate demand and plan accordingly.
In order to mitigate the impacts of VUCA, companies in the manufacturing and logistics industries invest in technologies such as artificial intelligence, IoT, and blockchain, to increase visibility and flexibility in their operations. They are also exploring new business models and partnerships to increase their resilience in the face of uncertainty and unpredictability.
Smart factory is not about technology – it is about business value. The goal of a smart factory is to achieve a high level of efficiency, flexibility, and customization in production while minimizing waste and errors of “VUCA World”. The importance of the smart factory lies in its ability to improve the competitiveness of companies by reducing costs, increasing production speed, and enhancing the quality of products. Additionally, smart factories can lead to new business models, such as servitization and mass customization, which can further drive innovation and growth in the manufacturing industry.
Smart manufacturing challenges
The implementation of a smart factory faces many challenges. Perhaps the easiest one to approach – while still far from being easy – is the challenge of technical complexity: integrating advanced technologies such as AI, IoT, and automation into a factory environment can be complex and requires specialized expertise. Purely technical problems created by technology can also be solved by it. Perhaps the most important solutions comes in the form of platforms.
In automotive industry different cars can be designed and build using the same shared set of common design, engineering, and production efforts, as well as major components, over a number of outwardly distinct models and even types of cars. In a similar way, standardised digital platforms can be used to provide multitude of digital services from multitude of vendors to multitude of end user devices.
The concept of platforms can be (and needs to be) implemented to the world of manufacturing in the form of Industrial IoT platform or shop floor operations platforms linking the smart devices into processes and integrating them with master factory planning and process management systems, such as MES, WMS, or ERP. In many industries platforms have become an accepted solution to the problem of integration with legacy systems: legacy systems are wrapped in digital “adapters” which provide access to legacy functions and data in the form of standardised services plugged into the platforms.
Modern digital platforms can most often be deployed as services in a global cloud infrastructure. This possibility while being a major game changer is approached rather reluctantly by manufacturing industry players. Especially the area of OT (Operational Technology) is often focused on point solutions and point-point integration. This is where transformational opportunity hits the wall of “legacy thinking” which is a major cultural obstacle in and digital transformation effort.
What is arguably even more important is the Data integration and management. The smart factory is a data driven human-technology ecosystem. Collecting and integrating large amounts of data from various sources can be a technical challenge, and requires a robust data management infrastructure, and skills (eg data scientists). Moreover, it requires a solid management and governance approach to clearly assign business responsibilities and roles such as data ownership and stewardship. While this challenge has a natural support in lean management community and processes, at least as far as the manufacturing and logistics processes are concerned, it is again the realm of culture and management style (eg evidence based management culture) which makes almost all the difference in harnessing big data.
Another complex problem is cybersecurity: As smart factories rely heavily on connected systems, they are vulnerable to cyber threats such as hacking and malware, requiring strong cybersecurity measures to protect against these risks. While this problem seems to be related just to to technology it cannot be effectively solved without addressing enterprise culture, technology governance, and even basic human psychology.
There are of course many other challenges. Adopting a smart factory often requires a significant cultural shift within an organization, as it involves changing the way work is done, and may involve reducing the role of human workers in some areas. Advanced automation often requires workers to acquire new skills, which can be challenging for organisations with a large and diverse workforce.
Finally, implementing a smart factory requires significant investment in new technology, infrastructure, and processes, which can be a challenge for some organizations. To achieve pos
Despite these challenges, the potential benefits of a smart factory, including increased efficiency, meaningful insights and better informed decisions, reduced costs, and improved product quality, make it a compelling investment for many manufacturers. According to IDC more than 80% respondents of 2022 World CEO survey are beyond the tipping point of initiating a “Digital First” programme, and more than half are already executing with 27% have established their digital transformation priorities well before pandemics.
“Triple A” for Smart Manufacturing
Transforming a manufacturing plant into a smart factory is a complex issue. Complex problems can be simplified by breaking them down into smaller, manageable components, or by approaching them from a different perspective. However, finding a simple solution for a complex problem requires a deep understanding of the problem and the ability to think creatively, applying shortcuts in the form of heuristics.
We would like you offer the readers such a “thinking tool” in the form of “Triple A” Heuristics for smart manufacturing. This heuristics brings together a starting point, transformational business concept and an enabling technology which can assist you in planning your digital journey.
The triple A stand for Advanced robotics (starting pint), Autonomous operations (business concept), and Artificial intelligence (enabling technology). Let us see how they work:
“A” for Advanced Robotics
From “old school” robots to smart machines
Advanced Robotics refers to the use of advanced technologies and techniques to design, develop, and control robots for various applications. Robots have been present in manufacturing industry for decades. The ingenuity of robotic engineers provided means to automate laborious tasks such as painting, welding, production of electronic components, or food processing. But the focus of this wave of production process automation has been the mass production process.
The “old school” robots are programmable devices optimised for specific role in the production process. Smart machines marking the shift to advanced robotics can adopt to different process requirements, product characteristics, and can coexist and collaborate with humans and machines alike.
This includes the integration of artificial intelligence, machine learning, computer vision, and other advanced sensors and actuators into robots, which enhances their ability to perform complex tasks and interact with their environment. Advanced Robotics is used in a wide range of industries, such as manufacturing, healthcare, logistics, and others, to improve efficiency, accuracy, and safety, and to reduce costs. The development of advanced robotics is driven by the need for automation in various industries, as well as the increasing demand for flexible and intelligent systems that can adapt to changing environments and perform multiple tasks.
Laying the foundation
The assets based on robotic solutions – such as assembly lines or material handling solutions – have their natural life cycle. While planning a retrofit, modernisations or replacement of these assets start thinking differently – instead of specialisation and point integrations start looking for flexibility, open architecture and platforms.
In many cases a major opportunity lies in intralogistics. It is usually poorly automated, equipment utilisation is poor and uncontrolled, simple automation solutions are often rigid and expensive in terms of change management. If you see these symptoms – start investigating autonomous transport system devices and platforms. Material handling is – in the end – the bloodstream of manufacturing plants. Industry analysts, such as IDC, point out the fact that intralogistics can be the pivotal point of your digital revolution.
“A” for Autonomous Operations
Operations on autopilot
When machines are becoming smarter they also require much less attention from humans. Or at least the focus of human intelligence can shift from micromanaging the machines to governing the systems. As cars are getting smarter, the drivers do not need to check and tweak the car in their garage to get optimum performance, shift gears manually or have a detailed understanding of city streets to get from A to B.
Drivers need to decide on the driving style – eg. sport, eco, auto-pilot – to let the car adjust its internal workings to drivers’ performance expectations. and follow the indications of navigation computer vision while deciding on faster or more economic route. This shift will increase dramatically as the autonomous car finally hit the roads providing their passengers with the means to use transit time more productively or enjoyably (unless, of course a passenger enjoys driving a car).
A similar thing begins to happen in the world of manufacturing and logistics. Traditional automated operations involve the use of machinery, robots, and computer systems to perform repetitive tasks with a high degree of precision and speed. In this setup, the machines are programmed to perform specific tasks and are controlled by a central system, but still require human intervention to adjust parameters, make decisions, and perform maintenance.
From managing devices to managing operations
Autonomous operations, on the other hand, involve a higher level of automation where the machines are able to perform tasks independently, without human intervention. These systems are equipped with advanced sensors, machine learning algorithms, and decision-making capabilities, which allow them to adjust to changes in their environment and make real-time decisions based on data.
In summary, automated operations rely on a high degree of pre-programming and human intervention, while autonomous operations are capable of performing tasks on their own, without human intervention.
Again – intralogistics can be seen as the foundation of your autonomous operation. Autonomous intralogistics platform can take orders directly from WMS or ERP system, and it provides meaningful insights into the process performance and device utilisations, as the robots can collect data as they move around the shop floor.
“A” for Artificial Intelligence
Industrial AI Use Cases
Industrial AI applications include both operations and management. There are many examples of artificial intelligence applications in manufacturing. Let us present a few.
- Autonomous vehicles used for material handling – autonomous mobile robots and forklifts use machine vision and image recognition to navigate freely in the dynamic environment of modern factory and handle material handling tasks cooperating with factory devices and systems. Such systems often use various
- Virtual reality and digital simulation of physical assets (digital twins) employ machine learning models and advanced performance analysis to provide predictive maintenance capabilities: Artificial Intelligence algorithms and AI systems analyze sensor data to predict when equipment is likely to fail, enabling manufacturers to schedule maintenance before breakdowns occur.
- Quality control: Artificial Intelligence systems use image processing and machine learning to detect defects and deviations from quality standards in real-time, improving product quality and reducing waste.
- Production planning and optimization: Artificial Intelligence algorithms are used to optimize production schedules, reducing downtime, maximizing equipment utilization on assembly lines, and minimizing waste.
- Inventory management: AI systems analyze data on sales, production, and inventory levels of components and raw materials to optimize stock levels, reducing the risk of overstocking and stockouts.
- Augmented Reality (AR): AI-powered AR systems assist workers with maintenance, repair, and assembly tasks, improving efficiency and reducing errors.
Process optimisation and experimentation
These are just a few examples of how Artificial Intelligence is being used in manufacturing to improve efficiency, reduce costs, and enhance product quality. As Artificial Intelligence technologies continue to evolve, we can expect to see even more innovative applications in the future.
One of such applications is the use of advanced data science and digital twins for optimising the material flow for autonomous intralogistics operations. Such capability allows shop floor manager to evaluate multiple scenarios and select optimum solution for a given manufacturing or warehousing process.
Summary
Heuristics are mental shortcuts or rules of thumb that help individuals make decisions quickly and efficiently. Simple heuristics can be useful in solving complex problems because they allow for quick decision making – Heuristics help individuals arrive at a solution without having to consider every possible option. They reduce information overload – Complex problems can often involve a lot of information. Heuristics can simplify the decision-making process by reducing the amount of information that needs to be considered.
Heuristics can provide a fair starting point for solving a complex problem, and can often lead to solutions that are good enough, even if they are not optimal. This can be especially useful in situations where a perfect solution is not feasible or needs to be evolved in a considerable time perspective.
It is important to mention that the triple A heuristic is the foundation of the AUTONOMY@WORK autonomous intralogistics platforms, which includes smart machines driven by navigational AI, as well as data driven tools for process design and optimisation, supported by digital twin simulation.
We believe our “Triple A” heuristics can be used as one of the fundamental navigation tools while planning a digital transformation of production floors, or manufacturing plants, and the introduction of industrial ai applications. However, it’s important to keep in mind that heuristics can also lead to biases and errors in decision making, so it’s important to critically evaluate their use and results.