How to optimise intralogistics processes
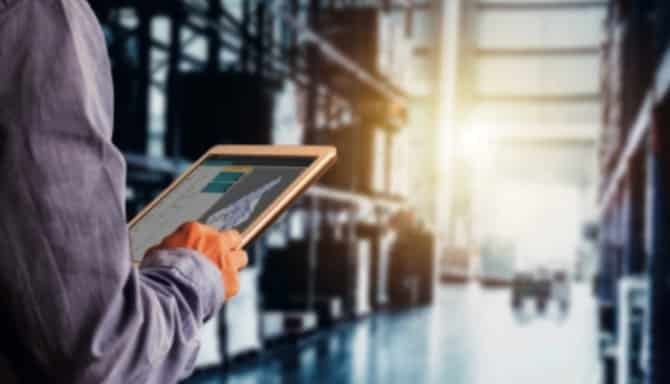
The challenge for Autonomous Mobile Robot (AMR) manufacturers is no longer just creating a reliable, efficient, and safe machine. The designs and the capabilities of autonomous robots are advanced enough to dominate intralogistics processes in production facilities and warehouses. However, the issue of efficient organisation of robot traffic is still a major obstacle, and in practice means traffic jams that look eerily similar to city congestion. The solution to this problem are optimisers of intralogistics processes.
“Our VERSABOT 500 and VERSABOT 1000 are able to handle building a map of their environment completely independently and autonomously,” said Jakub Michalski, Chief of Sales & Business Development at VersaBox. “They designate routes unassisted, exchange information, and overcome obstacles efficiently. Our goal is to maximise the potential of the entire fleet of robots, treated as a single entity, and not just individual machines. This is why we created the Autonomy@Work system – an optimiser, and a highly specialised tool for designing and modelling multi-robot intralogistics processes.”
The goal of optimisation is to unclog the system, clear the traffic jams and prevent them from happening. All this to make sure the robot is on the go and has as little downtime as possible, which could result from:
- waiting for the battery to charge,
- waiting for load collection or delivery,
- avoiding obstacles along the route.
How is a robot traffic optimiser developed?
An optimiser is a type of software that allows you to create a virtual twin of a real warehouse or production facility. After mapping the layout of the area to be optimised, the equivalents of real robots and other vehicles are added to the virtual space.
Once the ‘stage’ and the ‘actors’ are all ready, it’s time to assign roles and to start directing the ‘performance’. The better the script (i.e. data about the functioning of internal transport in a given environment), the better the results of the ‘performance’, that is, a virtual simulation of how processes function. A properly ‘taught’ virtual model can provide answers and solutions related to the functioning of real logistics processes, e.g. determine the number of necessary robots (especially at peak times) or their optimal speed. The model provides an opportunity to check the interdependence of individual factors and the impact of any introduced changes on the whole logistics system.
What are the objectives of robot traffic optimisers?
The purpose of virtual models is to optimise already existing intralogistics processes, as well as design, test and optimise new solutions before their implementation. There are three types of tasks the software is built for:
- Modelling and designing multi-robot intralogistics processes – creating a virtual model allows you to evaluate the efficiency of robots, determine the optimal number of robots for particular tasks, and identify system bottlenecks.
- Assessing the capabilities of an intralogistics system – the assessment does not only concern the mechanical properties of the robots or their ability to autonomously execute tasks, but also the possible use and efficiency of multi-robot systems, and the chance to harness their emergence potential.
- Assessing the flexibility of an intralogistics system – testing the possibility of introducing changes and a rapid assessment of their impact on the functioning of the entire system.
Modelling is not only about route designation, speed, and time or place of battery charging. It is also an excellent tool for creating contingency plans, for example system performance at peak times (during heavy workload) or in the event of machine malfunction. Rules for dealing with emergencies can be developed before the emergencies happen. A digital model is a very useful tool in the work of maintenance services.
Why does intralogistics modelling save big money?
The implementation of fleets consisting of tens or even hundreds of AMRs is a very complicated process. When dealing with such large fleets, it is effectively impossible to ‘manually’ develop a precise implementation without a virtual model. In a traditional industrial environment, the implementation of changes, observation of the consequences, followed by corrections, and the repetition of these steps until the desired effects are achieved, entail enormous costs. If a model, that accurately reflects the real working environment, can be developed, then an entire logistics system can be built and tested in the virtual world, and without the need to perform tasks in real life. This solution saves huge amounts of time, work, and costs wasted on failed modernisations.
Once created, the digital twin can accompany a production facility or a warehouse permanently. The virtual model, continuously supplemented with new data, will become an increasingly excellent optimising tool – it will allow testing of any planned changes, assess their impact on the system, and accurately estimate costs and potential profits. Interestingly, observing the inner workings of internal transport on a virtual model makes it possible to notice correctness and regularities that might go unnoticed in the real world. One of the reasons for this is that models can accelerate processes. Checking the impact of introducing more robots or changing the location of charging stations might take hours, days or even weeks in the real world. Model testing delivers results very quickly, within minutes or hours. Similar tests, using traditional methods, are rarely done because of the enormous costs associated with them. Virtual twins are not only cheap, but convenient too.
“At the moment, we input the data ourselves and provide our customers with results in the form of optimisation recommendations. Ultimately, however, our system will be made available through cloud technology in a Software as a Service model,” said Jakub Michalski. “In exchange for a subscription fee, our customers and subcontractors will be able to carry out tests and monitor the system independently. We will create the conditions necessary for conducting analyses based on process data, both historical and those collected in real time. The system will be available to use without the need to develop your own IT network – you will be able to use it directly from any device with Internet access”.
Optimising existing facilities and designing new ones
The modelling of logistics systems can also be successfully applied to facilities at the design stage. An internal logistics system based on VERSABOT 500 and VERSABOT 1000 robots can be built, tested and optimised, and the results can be used to create real spaces. The system created by VersaBox enables you to check the performance of the intralogistics system long before the first shovel touches the ground at the site of a new warehouse or factory.