5 BEST PRACTICES for Intralogistics 4.0.
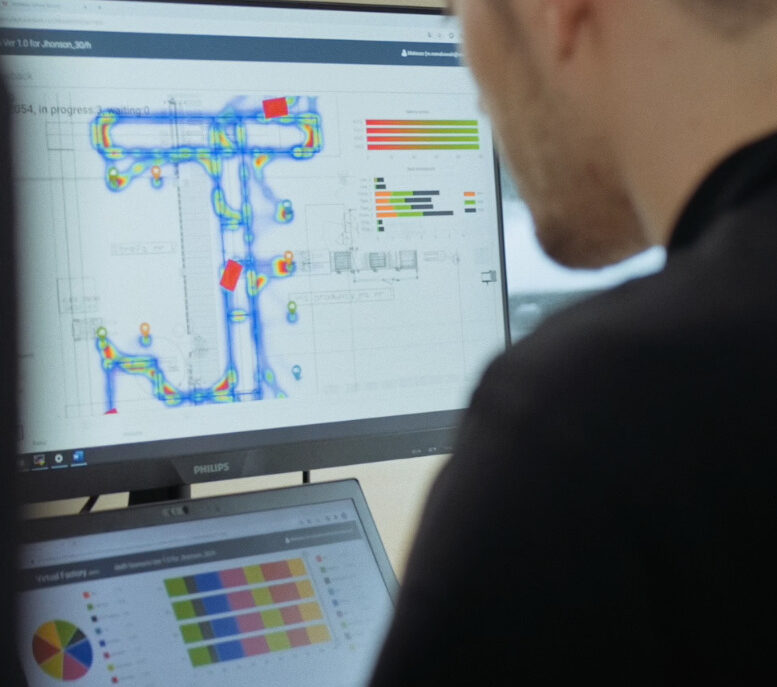
Intralogistics systems are innovative technological solutions for optimizing transportation processes in production and improving the flow of information within a company. They can make the internal transportation more effective, improve production processes efficiency, and smoothen the flow of goods in the supply chain and order picking. The prerequisite, however, is the use of appropriate solutions and good practices of the automotive industry.
A new era of production processes automation
Thanks to innovations in robotics, automation of manufacturing processes is entering a new phase today. According to an IDC study, so-called autonomous operations are one of the key areas of investment in the manufacturing industry today. Among them, investments in material and component transportation systems for manufacturing, based on AGV and AMR mobile robots (also referred to as collaborative robots), are leading the way.
AGV robots/vehicles have a long tradition of working in large industrial plants in developed countries around the world, but they often require considerable interference with the shop floor infrastructure during implementation. AMRs (Autonomous Mobile Robots) are a new category of devices. They do not require an infrastructure for navigation, are fully autonomous and can be deployed both in complex processes and in dedicated tasks “serving” the production lines, packaging stations, high-bay warehouses or logistics buffers.
This flexibility makes them applicable to plants of all sizes and production complexities, and the market for AMR robots is growing more than 40% annually.
5 good practices for implementing autonomous transport systems
Paul Strassmann, a researcher on the economic effects of computerization, wrote in his book “The Squandered Computer”: “Computers don’t make money, smart people do”. The same can be said of robots. It’s not the machines that are important, it’s the smartly automated processes that use their capabilities for specific benefits, such as increased productivity, better use of equipment, reduced costs, greater flexibility in production processes. Well-implemented intralogistics systems will give full control over internal transportation and improve inventory management.
Here are 5 best practices that any organization planning to implement such solutions in production automation should follow:
Practice 1: Plan automation comprehensively
Automating manufacturing processes should start with the concept of improving production processes by leveraging the capabilities of autonomous machines. This is a real challenge for companies for which autonomous systems are a new experience.
Many of them start the implementation of transport robots with limited pilots. Meanwhile, automation of manufacturing processes should be comprehensive, end-to-end endeavour to bring measurable, tangible business benefits.
In most cases, however, it is difficult to conduct comprehensive testing in an operating factory. No industrial or logistics company can afford to disrupt intralogistics processes or the flow of goods. In this situation, it is worth reaching out to simulation tools available on the market today. In particular, they are offered by providers of autonomous transport systems, such as VERSABOX.
Tools are also available that allow the creation of digital twins of production lines or even entire factories. These are very versatile systems, but require a lot of work to reliably reflect the operation of specific transport equipment. This is why VERSABOX provides tools which are focused on AGV based transport systems, are very fast to set up and easy to use by non-experts.
The VIRTUAL FACTORY system offered by VERSABOX will allow you to quickly build a realistic picture of how a transport system works. And while it won’t be used to create a digital twin of an assembly line or production nest, you can use it to quickly and inexpensively analyze many transportation system options.
Practice 2: Verify and optimize benefits
Spreadsheet models are not a reliable tool for analysing economic impact of autonomous systems. They are flexible but clumsy and can be bent to prove anything. A company’s P&L statement, however, is unforgiving, revealing the truth about how realistically we have assessed the return on investment. Here again, simulation capabilities play a huge role. The simulator allows you to design and test many variants of the transportation system, analyzing efficiency, energy consumption, lead time and many other factors that translate into production efficiency and, as a result, higher profits.
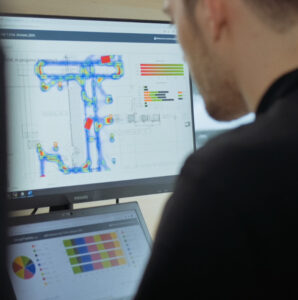
The return on investment of transportation robots can be significantly improved by making small changes to the design of transportation systems. The right choice of routes, location of docking and material handling points, or logistics buffers often results in system delivering the required performance with fewer robots than initially expected. Experimentation in the world of the “virtual factory” is simple and quick, while in the real world it often proves unfeasible. With a “digital twin,” you can test how the solutions in question will affect your company’s production processes without disrupting the real-world operations.
Practice 3: Verify key functionalities
Do you know what functional features and parameters transport equipment, and its software, should have? Which ones are critical to your process? Products differ in many features because vendors of products and solutions based on them seek competitive advantages by addressing their solutions to specific niches.
Once you know what your process needs, you can conduct very effective pilot tests – simply testing whether vendors meet specific technical or operational requirements. If you’ve planned comprehensively and optimized your process using simulations, they won’t last long, nor will they affect the normal operation of your plant. They will, however, bring confidence in the quality of the equipment and software you introduce to the shop floor.
Practice 4: When implementing robots, take care of people
The robotization of manufacturing processes always raises concerns among workers that when the equipment takes on work done by humans, jobs are at risk. Even where industrial robots perform work that is judged by humans to be mundane and unattractive, attitudes can emerge that hinder implementation.
Who can we guarantee will keep their jobs? Who needs to be helped to acquire the skills needed in a robotized plant? How can we use robotization to improve the quality of jobs? This is worth thinking about from the beginning.
Smart innovation makes plants grow, offering more jobs than those that close to modernity. Amazon is a case in point. According to a report by research firm LogistiIQ, the company has increased its workforce 7-fold since 2012, despite deploying 200,000 robots since 2012. During that time, the traffic handled by Amazon and the associated revenues have grown even more.
Companies which embrace robotisation are growing, creating more jobs as a result. Of course, these are different jobs. A worker on a production line, for example, instead of bringing components from the warehouse to the production line, will monitor robots shuffling the payload, intervening in situations beyond machine’s ability to act autonomously. The manager will organize the work of both people and machines, designing, configuring and monitoring processes through applications. There will be a growing demand for specialists managing fleets of autonomous equipment, ensuring their efficiency, integrating the equipment into cooperating systems.
Practice 5: Talk to users and their suppliers
Mobile robots in transportation processes are an innovation but no longer an experiment. This technology is proving itself in production deployments that require reliability, industrial safety standards. That’s why it’s worth talking to those who have successfully implemented autonomous material handling systems.
It may always be that you will find another user’s experience inadequate due to the nature of the industry or manufacturing/logistics processes you are implementing. It is worth remembering, however, that the statement “we are different” is the most common objection you hear from suppliers of innovative products and systems. Meanwhile, just being “different” does not always equal a truly valuable “competitive differentiation”.
Competitive differentiation based on innovative work organization creates value. A set of routine habits, or the “better is the enemy of good” philosophy sometimes destroys it. That’s why it’s worth talking to suppliers. Working in different organizations, they may be familiar with solutions leading to improved work efficiency, process flexibility, or cost reduction.
When listening to suppliers, it’s worth setting clear expectations of confirming the benefits presented through reference contacts, as well as by demonstrating a technical concept tailored to your organization’s needs (practices 2 and 3).
Intralogistics systems and their proper implementation – Summary
In this article I have tried to collect the most important issues to think about when implementing a transportation automation program.
If you are interested in more details I invite you to contact me. If you would like to learn more about the capabilities of our VERSABOTs and AUTONOMY@WORK system, I invite you to contact our sales team, who will competently present our offer and experience.